Advanced battery technology has been coming on leaps and bounds over the past few decades, with scientists and engineers around the globe racing to be the first to create superior batteries. This race is being run for good reason, with improved batteries set to push forward high-value technology such as electric cars and grid-scale storage for renewable power.
However, the methods and materials used to make advanced batteries is of continued concern. Many batteries contain harmful materials such as lead, cadmium, nickel or, more commonly for advanced batteries, lithium, which makes recycling a tricky issue. Not to mention the fact that lithium will become increasingly costly as it is a material in short supply.
The processes used to create materials such as anode grade graphite, used in today’s lithium batteries, can also be incredibly energy intensive, reducing the green credentials of the batteries they’re used in.
However, this could all change as researchers have found a way to convert atmospheric carbon dioxide into materials for advanced batteries, opening up the possibility of carbon negative electric vehicles.
The collaborative project has demonstrated how carbon dioxide gas can be recovered from the atmosphere, converted into carbon nanotubes and used to replace graphite electrodes in lithium-ion batteries to power electric cars.
The pairing of carbon dioxide conversion and advanced battery technology is the result of a collaboration between the laboratory of Dr Cary Pint, assistant professor of Mechanical Engineering at Vanderbilt University, Tennessee, and Dr Stuart Licht, professor of chemistry at George Washington University, Washington D.C.

Taking steps towards a ‘carbon commodity’
The research team has developed a solar thermal electrochemical process (Step), which is designed to convert greenhouse gas carbon dioxide into a “useful carbon commodity”. The process uses inexpensive electrode materials, a galvanized steel cathode and a nickel anode, and molten carbonate electrolytes that are heated and powered using concentrated photovoltaic (CPV) cells that convert sunlight into electricity at 39% efficiency.
The CPV cells provide both the electrical and thermal energy necessary to break down carbon dioxide into carbon and oxygen and to produce carbon nanotubes that are stable, flexible, conductive and stronger than steel.
Dr Licht told PE: “Producing conventional anode-grade graphite is expensive and the process creates waste. The cost is not so much the material but the purification process. The majority of anode grade graphite used in today's lithium batteries is synthetically made heat treating petroleum coke or coal tar pitch to 2500 to 3000°C and cleaning.
The Step process is not only more efficient, but also consumes, rather than emits carbon dioxide (unlike conventional methods).”

The researchers demonstrated that the carbon nanotubes created using Step can be incorporated into both lithium-ion batteries, like those used in electric vehicles and electronic devices, and low-cost sodium-ion batteries under development for large-scale applications, such as the electric grid.
Dr Cary Pint, assistant professor of Mechanical Engineering at Vanderbilt University, said: “This approach not only produces better batteries, but it also establishes a value for carbon dioxide recovered from the atmosphere that is associated with the end-user battery cost. Unlike most efforts to reuse CO2 that are aimed at low-valued fuels, like methanol, that cannot justify the cost required to produce them.”
Licht added that Step is readily scalable and that large scale manufacturing is achievable, not only with solar CPV’s but also with other renewable electricity used to power the carbon nanotube electrolysis production.
Making cheaper, greener batteries
Depending on the specifications, making one of the two electrodes out of carbon nanotubes means that up to 40% of a battery could be made out of recycled CO2, Pint estimated. This does not include the outer protective packaging but he suggested that processes like Step could eventually produce the packaging as well.
Licht added it would be theoretically possible to create a battery with more than 40% recycled CO2.
The researchers estimate that with a battery cost of $325 per kWh (the average cost of lithium-ion batteries reported by the US Department of Energy in 2013), a kilogram of carbon dioxide has a value of about $18 as a battery material – six times more than when it is converted to methanol – a number that only increases when moving from large batteries used in electric vehicles to the smaller batteries used in electronics. And unlike methanol, combining batteries with solar cells provides renewable power with zero greenhouse emissions.
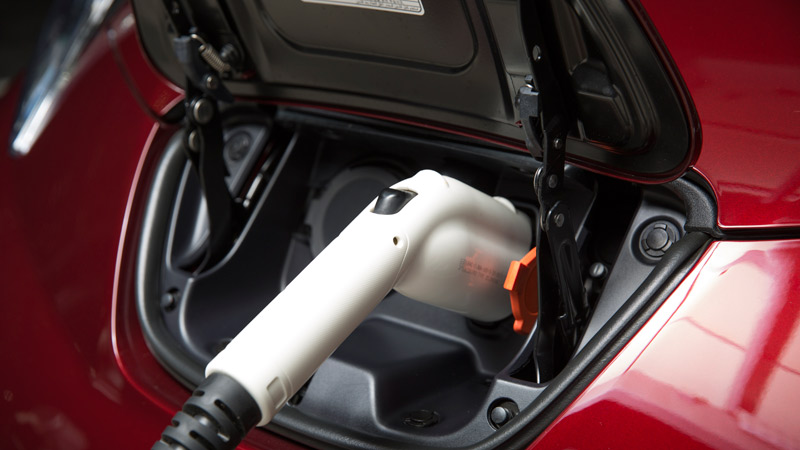
The next steps
Licht said the researchers plan to explore the full properties of low cost carbon nanotubes, including tailoring the synthesis for low-cost building materials with higher than steel strength, energy storage, nanoelectronic and catalyst applications.
They will also carry out theoretical modelling to gain greater understanding of the low energy, high yield route to CO2 transformation and look to scale up the process.
Licht has also proposed that the Step process could be coupled to a natural gas powered electrical generator. The generator would provide electricity, heat and a concentrated source of carbon dioxide that would boost the performance of the Step process. At the same time, the oxygen released in the process could be piped back to the generator where it would boost the generator’s combustion efficiency to compensate for the amount of electricity that the Step process consumes. The end result could be a fossil fuel electrical power plant with zero net CO2 emissions.
“Imagine a world where every new electric vehicle or grid-scale battery installation would not only enable us to overcome the environmental sins of our past, but also provide a step toward a sustainable future for our children,” said Pint. “Our efforts have shown a path to achieve such a future.”
Pint’s vision of a green utopia powered by clean battery technology is an inspiring one. Whether battery developers - fuelled by their government’s own vested interests and the promise of becoming a leader in a very lucrative industry - are swayed by his vision remains to be seen.