Human factors aims to minimise human errors and enhance human performance through early agreement to a structured approach to new system implementation, and ongoing design and safety assessment projects. Human Factors should also be considered in the design and running of an organisation, e.g. design of safety management systems, becoming a learning organisation, promoting safety culture.
Human factors integration is concerned with providing a balanced development of both the technical and human aspects of equipment procurement. It provides a process that ensures the application of scientific knowledge about human characteristics through the specification, design and evaluation of systems.
Ergonomics and human factors – what’s the difference?
The two terms are often used interchangeably. Ergonomics is often the more favoured term in the UK and human factors more common in the USA. Some people have tried to distinguish between the two, but most believe that any distinctions are arbitrary and that, for all practical purposes, the terms are synonymous. However, some specialists may still debate the correct use of these terms.
The breadth of the topic makes it more important to check for relevant experience in the area of competence where expertise is needed.
How human factors is involved with the design process
The aim of human factors input into design is not to relieve the designer of the responsibility for incorporating humans in the design solution, but to support correct consideration of human factors issues in the design. This process relies upon the designer requesting input from human factors, as a specialist area, to ensure compromises in the design solution are minimised. Human factors advice should be sought for all new designs, or when design changes are proposed.
It is important that human factors is involved early in the design process. Early consideration of human interactions with a design provides improved reliability of identification of potential safety and operability issues. The potential for costly rework to address these issues late in the project is also minimised.
User-centred design
"A multi-disciplinary activity, which incorporates human factors and ergonomics knowledge and techniques with the objective of enhancing effectiveness and productivity, improving human working conditions, and counteracting the possible adverse effects of use on human health, safety and performance." - ISO 13407
To achieve a design that meets these quality requirements, user centred design activities must begin at the earliest possible stage, and be maintained throughout the design process shown in figure 1:
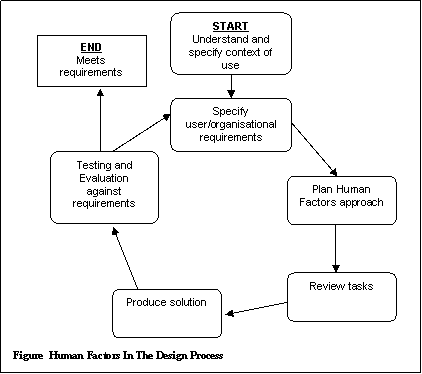
Human factors/ergonomics methods
Task analysis: The name given to any process that identifies and examines the tasks that must be performed by users when they interact with systems. It is a fundamental human factors approach which assists in achieving higher safety, productivity and availability standards. It helps the analyst collect information about the human involvements within the system, organise this information, and then use it to make various judgements or design decisions.
Allocation of function: Usually takes place at the concept phase of design, it is used to assign tasks to either humans or machines based on their respective strengths and weaknesses to ensure best system performance.
Workload analysis: A workload analysis is conducted in order to assess the level of physical and mental effort required from operators within specified operational scenarios.
Operability evaluation: Conducted to ensure that the system being designed/assessed is operable by the available personnel, under representative scenarios and conditions. If equipment is not ‘fit for purpose’ in this way there will be an increased risk relating to operator error.
Maintainability evaluation: Conducted to ensure that the system being designed/assessed is maintainable by the available personnel, under representative scenarios and conditions. If equipment is not maintainable, maintenance actions that are assumed to be carried within the limitations/scope of the design may not be done, resulting in a detrimental effect on component and equipment reliability.
Training Needs Analysis (TNA): Carried out in order to recommend the most cost-effective and operationally effective training solution for the system in question. TNA provides a basis for demonstrating that personnel are suitably qualified for conduct of the required tasks.
Environmental assessment: The environment can have a significant effect on the operator or maintainer’s ability to conduct tasks without error, irrespective of their skill level or the extent of their knowledge.
In addition, an inappropriate environment can cause health hazards to personnel. An environmental assessment may include a thermal, noise, vibration or lighting assessment, or assessments in combination. By conducting such an assessment, the environment in which operators and maintainers work can be designed to be within limits acceptable to humans, both in terms of comfort and safety.
3D-modelling: Many human-modelling CAD systems now exist such as SAMMIE and JACK. These design tools enable evaluations of postural comfort and the assessment of clearances, reach and vision to be conducted at early stages in the design process.
Find further reading