Multiphysics software, which allows engineers to combine different types of simulation, first appeared in 1978. Now it is becoming increasingly accessible, finds Ben Hargreaves
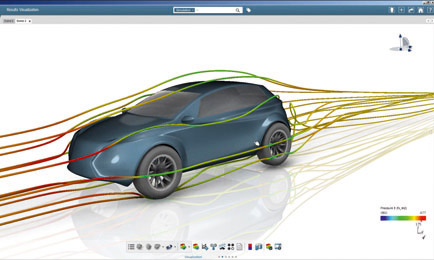
Powering design: Automotive engineers can analyse simulations of fluids and heat transfer using multiphysics
In the world of engineering software, multiphysics, or the combination of different types of simulation – such as merging equations modelling heat transfer with solid mechanics to solve a problem concerning heat flow and stress analysis in an automotive powertrain – is by no means new. For example, the first version of Abaqus, the Dassault Systèmes (DS) package that carries out this kind of work, was released as far back as 1978, following its development in the US.
Abaqus, which today falls under the French company’s Simulia brand, encompasses several technologies, including the finite element analysis for which it was originally designed, as well as computational fluid dynamics and simulation of electromagnetic phenomena. The aim of multiphysics has been to make it possible to understand the way in which an engineered structure will behave as a whole through simulation, so that, for example, it’s possible to ascertain how a design for a valve in a hydroelectric power plant will behave after it’s manufactured and put into operation.
“Typically, in a software structure you can’t solve equations of fluid flow and solid mechanics at the same time,” says Dale Berry of DS. “The nature of solving both of these [sets of] physics requires different code architectures. The goal is to link the solutions so that, as they run, they transfer information to each other.
“Today’s definition of multiphysics encompasses both ways of doing it: solving problems together as well as solving them separately, and then passing the data back between them.”
Multiphysics software from US-based firm Comsol has been used by engineers from Boeing to analyse the behaviour of a material added to the composites that are used extensively throughout the body of the 787 Dreamliner – the world’s first airliner to use them as its primary structural material. Expanded metal foil (EMF) is added to the composite structure lay-up as a protective measure, to dissipate extreme heat and current generated by a lightning strike. To ensure that protective coatings on the EMF remain intact when subjected to thermal stress arising from the flight cycle, engineers at Boeing’s research and technology division used multiphysics and physical measurements.
The impact of the EMF design parameters on stress build-up and displacement in each layer of the composite structure lay-up was evaluated in Comsol’s Multiphysics software. Subsequent physical experiments confirmed what the simulations had suggested, and that designs characterised by lower displacements also have a reduced likelihood of crack formation.
Comsol was started by graduate students at the Royal Institute of Technology in Stockholm, Sweden, in the mid-1980s. The first version of its Multiphysics package, released in 1998, includes tools for finite element analysis, computational fluid dynamics, and systems for modelling molecular flow and acoustics, among many others. The software is cross-platform, capable of running on Windows, Mac OS and Linux, and has interfaces to Matlab and CAD packages. It also allows for entering coupled systems of partial differential equations.
The aim, says Valerio Marra, technical marketing manager at the company, was always to develop an integrated suite of software tools, to simulate engineering designs. “The approach in the past was to create specialised codes for a specific set of applications, so you had the structural mechanics people, the thermal guys, and the acoustic people – and there were a lot of great products. At a certain point, engineers said: ‘We have the technology, and computers are getting faster and faster – can you give us software that can take into account more than one [set of] physics?’
“The market wanted us to come up with an integrated solution. Our engineers wanted to make the best mechanical and heat transfer codes work together, and they did it. We wanted multiphysics from day one,” says Marra.
“The idea was to couple different physics in a natural way, and that approach is in our DNA.”

Virtual currency: Using multiphysics helps reduce development costs
American engineer Chris Wolfe is the product manager for multiphysics at Ansys, which specialises in finite element and structural analysis software. She previously worked for computational fluid dynamics firm Fluent, which Ansys acquired in 2006. As well as acquiring Abaqus, DS has also bought up other companies to bolster its multiphysics offering. Despite the desire to link different types of software together, Wolfe says there will always be a place for single physics simulations.
“Multiphysics, no matter how you do it, is more expensive, and the pressure is on companies to get to market – they will use the physics they need to get the product out the door,” she says.
“You can still get a lot out of a single physics analysis. There are a lot of problems solved around the world that don’t even use an engineering simulation; they use a range of tried-and-tested empirical methods, or more traditional correlation that starts with a notebook.”
Wolfe adds that Ansys puts a lot of development work into single physics solutions. “They form the basis of the multiphysics simulation, when you start exchanging the data. But I think it’s an exciting time to be involved in multiphysics. Everybody’s talking about it and everybody’s doing it.”
At DS, much of the software development involves getting disparate codes to work together as smoothly as possible. For example, in automotive, engineers may wish to combine simulations of fluids, heat transfer and structural mechanics regularly.
“It’s not a luxury – it’s a requirement,” says Berry. “Every year, a new simulation comes along combining acoustics and electromagnetics. The power to do things in a virtual way, rather than with the expense of doing them in a physical way, is a huge driver.” He believes that all firms will have to offer multiphysics capabilities, and that DS is likely to make more acquisitions to enhance its own portfolio. “There is a tremendous amount of consolidation that has to occur to reach the limits of the multiphysics concept.”
With the giants on the acquisition trail, it’s difficult to see how a start-up could challenge them. “There will certainly be codes developed in academia that come out and contribute to the space, but to go from zero to leapfrogging DS, Ansys, or Comsys, or any of the multiphysics players who are investing so much in it – I don’t see that,” he says.
Getting different systems to talk to each other is a big area for research at DS. “There’s significant investment occurring on both the physics front and the co-simulation front,” says Berry.
Wolfe of Ansys believes the biggest challenge for a software provider is how it sends data between the different physics, as the meshes in each one aren’t the same, so accurate data mapping is a crucial consideration. “Because Ansys has grown by acquisition, our solvers aren’t the same,” she says. “Our challenge is getting these things working, making data transfer, and making things nice and usable.”
Berry agrees that working on user interfaces is an important area for simulation software firms. “If you have a user interface tailored toward finite element analysis, and a second interface tailored toward computational fluid dynamics, the user has to be comfortable with two different software products. The software industry is trying its best to provide commonality by removing some of
these hurdles.”
Comsol, with a multiphysics offering developed from scratch, believes it has solved some of these problems. “There is a lot of effort involved in getting the different codes to talk to each other and making sure that the physics and the mathematics are right, says Marra. “The advantage of Comsol is that we can be sure that we are replicating nature – the physics, the equations, and the ways in which they talk to each other are really accurate.”
He adds that engineers want to spend more time designing, and less time simulating. “If you’re an engineer, do you want to spend time coupling code, or designing? That’s the question.”
While multiphysics may be widespread in the engineering community, it tends to be the domain of specialists. Simulation firms would like to see this change. “The future is to take this technology and make it more accessible, so it’s not for highly trained PhD level engineers,” says Berry.
Marra agrees. “We are working toward a phase where a physicist who developed a model in Comsol can easily share it with co-workers. This is the next direction. You need experts currently, and it can take years to get there.”
Wolfe says large companies tend to have engineers who specialise in either fluid analysis, or structural mechanics, or electromagnetic analysis, but the set-up is different with smaller firms. “At small companies you tend to have the ‘Swiss army tool’-type engineer, who use any tool they can to solve the problem in hand.”
And Berry believes that this approach should become more commonplace. “Everybody should be able to benefit from the results of a multiphysics simulation,” he says.
Cobham software helps CERN to prepare LHC for high-luminosity operation

Opera electromagnetic simulation software from Cobham Technical Services is helping scientists at CERN to design the magnets needed for the forthcoming upgrade of the Large Hadron Collider (LHC) in preparation for high-luminosity operation.
Both the 2D and 3D versions of Opera are being used to model a wide variety of the LHC injectors’ normal conducting (NC) electromagnets and permanent magnets, starting with the magnets of the new 160 MeV H- linear accelerator and including upgrades of those used in the transfer lines and other accelerators on the way to the LHC.
Several tens of different magnet types and variants are being analysed using Opera-2D; these are then remodelled in Opera-3D. By accurately simulating end effects, the Opera-3D tool facilitates design of more efficient magnets, and allows local effects such as saturation and field harmonics due to non-planar symmetry to be taken into account during early design.
CERN’s technology department is also using Opera to design NC particle accelerator magnets for numerous other projects. Daniel Schoerling, project engineer for NC magnets at CERN’s technology department, says: “With most of our magnet designs, we require high prediction accuracy of the magnetic field quality in the good field region – typically of the order of 1/10,000 or better. Over the years we have gained confidence in Opera’s magnetostatic simulation performance for solid and laminated yoke magnets, supported by the effective correlation between simulation results and magnetic measurements obtained from manufactured units.
“When we observe differences higher than a few parts in 10,000, we can usually attribute them to factors such as mechanical error or uncertainty of the BH curve of the material used for the magnet’s manufacture. In fact, because of the accuracy of the software’s magnetic length and field quality predictions, with many of our magnet designs we no longer need to incorporate any means of performing post-production field quality correction.”
The core finite element analysis technology behind Opera was originally developed to support the design of particle accelerator magnets, starting with a project in the 1970s by scientists at the UK’s Rutherford Appleton Laboratory. At that time, the software required a mainframe computer and was intended principally to help solve design problems with the move towards superconducting magnets for higher energy particle accelerators. Today, the software addresses multiple types of physics – including electromagnetic, thermal and stress – and offers 2D and 3D design, simulation, analysis and optimisation facilities.
Ansys rating highlights power of simulation

This year’s Software 500 index has positioned engineering simulation firm Ansys at 105th place in recognition of its 2013 software and services revenue of more
than $860 million.
“The annual inclusion of ANSYS on the Software 500 is continued proof of the power of simulation-driven product development,” said Jim Cashman, Ansys president and chief executive. “Companies from around the world are using our multiphysics solutions to create innovative products while reducing development costs and speeding time to market. Ansys solutions drive a real return on our customers’ investment, which is why they continue to turn to our software.”
The Software 500 is a revenue-based ranking of the world’s largest software and services suppliers, targeting medium-to-large enterprises, IT professionals, software developers and business managers involved
in software and services purchasing.
The report, published this month, provides a quick reference source on vendor viability.