Read on to understand the vision and philosophy driving their factory design, from minimising energy needs to eliminating fossil fuels and much more, providing an example for others looking to achieve similar objectives.
Please can you briefly explain your current role and expertise on this topic.
Andy Joynson (AJ): At innocent my job title is Chief Blender (we all have slightly unusual names). I’m the Site Director, responsible for the team designing and building the blender, our new factory here in Rotterdam. That means the leading the physical design and build, the energy and process equipment solutions and the best bit, finding the team that will run and operate the blender.
Kindly explain the objectives of your innovative manufacturing site
AJ: The blender plays a key role for innocent in becoming what we call ‘good all round’. For us, this means becoming a company that does the right things for the planet, for our people and the communities around us, and for our business.
First and foremost, the factory will play a major role in helping innocent reach its goal of being carbon neutral by 2030. As one example, by choosing the Port of Rotterdam as our home, we’re taking millions of miles off the road which means we’re reducing our carbon footprint dramatically. The factory itself will be one of the world’s first operationally carbon neutral factories. It has been designed to minimise our energy needs, by bringing together industry leading minds in the design, we’ll make this an all-electric site, so no fossils. All the power needed will come from new renewable energy generation that we will commission specifically for the Blender. We are aiming to achieve BREEAM Outstanding accreditation, so every element of the build has had sustainability in mind and we’ve looked to source as many materials locally too.

The technology in the process means we radically reduce the amount of water we need too, and any waste we may have will be reused or recycled locally.
On the people side of things, we want the blender to establish a new kind of factory work. It will be the first WELL-certified factory in the world, meaning that it has all the things a great working environment needs like plenty of light, space to move around, great air quality and healthy food. It will be a safe place where people are empowered to do be the experts in their field. Inclusivity, diversity, transparency, and fun are our top priorities. Beyond the well-insulated walls of our factory, we want to make sure we’re being good neighbours and helping to support the local community. Think: hiring local workers, investing in local suppliers, teaming up with schools so students can learn about sustainable factories and so on.
Finally, we want the blender to be a shining example of a sustainable factory that will inspire businesses to push the boat out when it comes to their own factories – and hopefully do it even better than us.
What were the key challenges to overcome in its development?
AJ: Building a factory from scratch is never an easy job, but we’re making steady progress and are very excited to start our operations by the end of summer 2021.
Probably the biggest challenges for us were:
- Getting to a design of a factory from scratch. innocent has never built or owned a factory before so pulling in the right expertise and experience to help has been critical. Because of our relative inexperience we’ve made some mistakes and sometimes design has not always taken a direct route. The added factor has been that we wanted to build an operationally carbon neutral factory. That made us to continuously challenge ourselves, and the design, until we found a way through. Specifically, the energy demand side was a problem at the start – heat pumps to recycle energy have been key and also, raising high temperature (close to boiling) water also. The clever energy design meets our needs there too.
- Building a factory in the centre of a global pandemic has been ‘interesting’. The team we’ve hired has mostly been hired virtually. Arrangements on site have been designed to help us manage everyone’s health while managing progress at the same time. So, I am still amazed that after more than 12 months of Covid measures we are still on track to hit our start-up date.
What features of your new site could be adopted by those in other industries?
AJ: Inspiring wider change is one of our key objectives and so that’s why we’re going to ‘open source’ everything we’ve learnt with anyone who wants to hear about it. From the mistakes we’ve made, via the technology we use, to the sustainability work we’ve done. That information will be made available to everyone, meaning all features of our site can be adopted by those in other industries in case they are of value to them. Two particular elements should be of interest, I think. Maximising the recycling of energy with heat pumps is one, and the second is in the design of our process cleaning – our design slashes the water footprint of the factory versus peers.
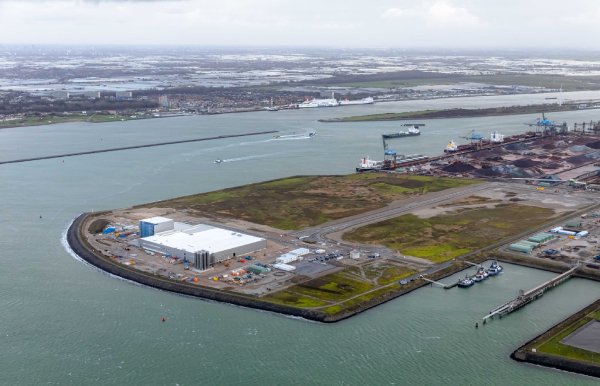
There are some who say that decarbonisation is not a priority to them as the target is 2050, what would you say to them?
AJ: We all need to do our bit to keep climate change below 1.5 degrees. We’re the first generation that can’t say ‘we didn’t know’ about the crisis we face and the last generation that’s able to something about it. If we don’t act now the consequences are disastrous for our kids and grandkids.
If you want to do things well and make real change, you will have to consider that working towards a carbon neutral supply chain/organisation takes time. So, better start now. The sooner we get more organisations to prioritise decarbonisation, the better our chances of reaching that target.
What has been your progress and/or biggest achievements when it comes to decarbonisation?
AJ: Let’s focus on the blender for this one. We’re not there yet, as we’re still building the blender and continuously implementing all kinds of projects – whether they’re at the blender or in other areas of the wider supply chain we influence or interface with. When it comes to the design and construction of the blender, we’ve already achieved some great milestones.
- The blender is a major milestone in the overall company’s path to de-carbonising – the location and build will remove 20% or our emissions and benchmarking our performance and using our learning can apply into our co-packer and supply chain partnerships.
- The design of the energy system and its management is clearly a key milestone.
- We have identified a path to build incremental renewable energy generation capacity that will supply the factory needs.
- We have the very first high gross vehicle weight BEV trucks in Europe running at full permitted weight on the kind of duty cycle that will test and generate learning for the next generation vehicles.
It’s all starting to come to life. Supply strategies, technology, innovation, and a bit of luck.
What do you think is the number one challenge for organisations looking to reduce their emissions?
AJ: It all starts with the overall business strategy. If a business doesn’t fully commit to certain targets related to reducing your carbon footprint, then the likelihood is it’ll start slow and feel the pain later. None of us has a crystal ball but my guess is that the business and regulatory environment that allows us to use the atmosphere as a free dustbin for CO2 is coming to an end. I think carbon taxes will be around a corner not far away.
So, while costs are a big topic, for us too, the idea is that investing in ways to reduce emissions is good for the planet and good for profit.
What is your advice to organisations just starting their work towards a more sustainable process?
AJ: Start now. Understand your business; scope 1, 2 and 3. Identify the threats (regulation/tax for example) and start building a business case. Research and find experts who can advise on zero or low fossils design but do things in order. Energy efficiency is key and first priority in any plan, so minimising demand through efficient pumps, motors, and air handling right-sized etc is fundamental.
What are the next steps in your journey to net zero?
AJ: Innocent aims to be net zero by 2030. To reach this target, we focus on 2 areas:
- We plan on cutting the carbon emissions from ‘farm to fridge’ in every drink by 50% by 2030. The blender plays a key role in this but work with growers on things like carbon capture in the fields will feature too.
- We will have to balance the rest of our carbon emissions by using trusted carbon offsets which give back to nature.
What breakthroughs in terms of technology do we need for a more sustainable industrial sector in the future?
AJ: On the energy technology side I believe the core of what we need is known and deployable and our challenge is to do that, and to avoid paralysis driven by a search for the next new or in some cases trying to resurrect past ideas that are technically interesting but energetically inefficient and therefore uneconomic.
So, we know how to generate energy – we just need to go much faster at deployment of wind, solar, geo-thermal, hydro etc. And accelerating the development of deployable storage will be key.
Why do you feel it is important for all engineers and professionals involved in manufacturing to be part of the conversation about preparing for net-zero?
AJ: Engineers and professionals are part of the problem and part of the solution. Until we’re all engaged and educated about the challenges and solutions then we continue to put a greater load on the planet’s capability to sustain life.
As we learn, we need to be involved, because people with the capability to understand energy, thermodynamics, the laws of physics, entropy, etc. will help the businesses and communities we live in, make wiser choices.
The Institution's Decarbonisation In Industry seminar will take place on 24 June 2021
This event will focus on the steps towards a more sustainable and competitive organisation including energy demand analysis and adapting processes to reduce energy use and increase efficiency, led by presentations from Rolls-Royce, HVM Catapult, innocent, BMW UK and Climate Change Committee.
Gain insight into reducing energy demand in the most energy-intensive industries: cast stone and steel as well as considering alternative green energy supplies, such as hydrogen. Expert-led virtual break-out rooms will allow you to join the discussion and network with your peers.
To read the full programme and register your place, visit the event website.