Ratan Tata, chairman of Tata Group, officially declared open the Bladon Jets engineering centre in Coventry recently. At the same time he unveiled a masterclass of manufacturing technology that Bladon Jets engineers have brought together to produce micro gas turbines destined for generating sets and hybrid electric cars and vans.
Tata is one of several organisations giving financial support to Bladon Jets. Jaguar Land Rover, part of Tata Motors, is providing technical support – the microturbine also powers Jaguar’s C-X75 concept car.
“What I have seen here vindicates the faith I had in what seemed like a tremendous idea,” said Ratan Tata. “It is far more sophisticated and impressive than I ever imagined. I think this company has a great future, and I feel very proud to be a small part of it.”
The single-shaft microturbine comprises only 49 parts. It has a four-stage axial compressor and a centrifugal compressor, an annular reverse-flow combustion chamber and a radial inflow turbine. Maximum speed is 100,000rpm.
At this level of technology, support comes in many guises, and several businesses provide Bladon Jets with technical expertise. Rolls-Royce, for example, which has made very small gas turbines too, has been supportive.
One of the most remarkable components that investors and supporters alike could inspect was the engine’s nickel superalloy nozzle guide vane (NGV) assembly, together with the compressor/turbine, both central to the micro gas turbine.
The highly complex, one-piece NGV is manufactured by Materials Solutions of Worcester, a small company focusing on additive layer manufacturing (ALM). Materials Solutions, founded in 2006, is a specialist in metal powder bed ALM using EOS 200W argon laser machines to produce functional parts – so-called “make to print”. The firm has developed processes to deliver materials with mechanical properties equivalent to those of cast or forged parts.
The Bladon Jets NGV demonstrates the fine art of ALM, namely high-value, thin-wall engineered components that might otherwise be extremely difficult to make or, if they can be made, would require heavy machining.
The size of component that Materials Solutions can comfortably handle is determined by the capacity of its EOS machines. The NGV is just within the limits of the machine, namely 250mm in diameter and 200mm high. It would be very difficult to manufacture this complex part by any other means.
The entire microturbine design is generated in CAD and this forms the basis of several manufacturing processes. In addition to the NGV’s design features, which are transferred to Materials Solutions, the CAD model is a driver for parts inspection on the co-ordinate measuring machine, as well as offering data for A&M EDM of Smethwick. This company makes the tools that generate individual compressor and turbine blades on blisks (disks that contain either compressor or turbine blades). The CAD model is the driver for an electro-discharge machine (EDM).
Materials Solutions can receive CAD data in multiple formats but makes a virtue out of the fact that it is not an engineering design resource and has no interest in the function of the shapes it builds. It does, however, assist customers’ designers with their designs for the manufacturing process. It is rare that a part, as designed for machining, will be optimal for building by the ALM process.
Carl Brancher, chief executive of Materials Solutions, says: “We frequently find break lines between components need to move and possibly we can make complete assemblies, obviating the need for machined faces and fastening systems. We can make castings designs, but with far thinner walls. As such we have two deliverables: manufactured parts and technical capability.
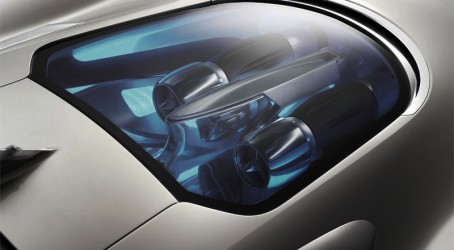
“We work in high-grade stainless steels and specialise in high-temperature nickel-based alloys such as Hastelloy and Inconels,” adds Brancher. “We focus on jet engine and gas turbine engine parts for the pragmatic reason that such engines contain many parts of the type we can build, using materials we can build in and with a major supportive customer in the form of Rolls-Royce.
“So we have made jet engine parts our ‘home’ and expanded out of it into other related high-temperature applications, such as motorsport. The aerospace industry accounts for 90% of our business and exports run at over 50%. Medical and dental sectors are already addressed by others.
“We are an approved vendor for Rolls-Royce, Rolls-Royce’s nuclear sector and Rolls-Royce Canada. And we are approved by ITP in Spain and Mercedes-Benz AMG. Among customers in the last few months are: Sumitomo Precision Products (Japan), Tusas Engine Industries of Turkey, Alstom in Switzerland and Parker Aerospace in the US.”
Besides the NGV component, Materials Solutions makes other parts, including the microturbine’s crucial central bearing housing.
A&M EDM is another young company. Just nine years old, it is one of the largest EDM firms in the UK with 20 wire/EDM machines. Among its components for Bladon Jets are: combustion housing, exhaust ducts, compressor casing and air bleed chamber, main shaft, bearing housing, centrifugal system housing and a deswirl diffuser. It has made parts sufficient for two development engines.
A&M EDM also makes the graphite electrodes that Bladon Jets needs for “sparking” in its newly delivered Sodick AQL325L EDM machine to generate the blade profiles on the crucial compressor and turbine blisks. A&M EDM produces these electrodes on five-axis milling machines. CAD data for the blade components are supplied by Bladon Jets and these are used in the EDM machine to generate the three-dimensional cutting strategy that creates blade profiles.
Surface finish, accuracy and precision are crucial to rotating components, including labyrinth seals, as these can affect the entire performance. This is especially so with compressor and turbine blades that are very small (20mm high) – it is vital to hold fillet radii and tip clearance within tolerance. Aerodynamic surfaces produce losses, especially end losses, and to reduce these requires excellent surface finish, accuracy and precision.
Computational fluid dynamics is just one tool that Bladon Jets uses to optimise compressor and turbine blades. However, it is only through bench testing that engineers can verify their initial assumptions and then optimise further.
Blade tip and other clearances, acceptable at cold, can quickly change as the engine reaches operational temperatures, creating “rubbing”. These require an iterative development process to optimise the final design. Typical turbine temperature is 1,050°C; exhaust temperature is 650-700°C.
Finally, Bladon Jets can see the day when microturbines serve as 100kW generator sets, and these will require heat exchangers to improve thermal efficiency. To this end, Bladon is working with Brayton Energy Canada of Gatineau, Quebec, whose patented wire-mesh heat exchangers are said to offer enhanced heat transfer and efficiencies better than those of a diesel engine. Brayton expects to ship its first full-scale unit to Bladon in July with engine testing beginning in 2013. Meanwhile, Brayton has been asked to build a full-scale prototype intercooler for a hybrid truck development programme. This will take the form of a gas turbine with an intercooler and recuperator. Brayton claims the ultra-compact plate-fin counter-flow wire-mesh exchangers will dramatically improve overall cycle efficiency.
Brayton expects to begin small-scale production in 2013 with ramp-up in 2014. Full-scale testing will take place in Canada, the US and the UK this year.