Supacat, a UK firm with a workforce of just over 100 people, has been developing military personnel carriers for more than 30 years. During the past decade, the company, which is based on the fringe of Dunkeswell airfield, near Honiton in Devon, has been responsible for two vehicles that form a core part of the requirements of the UK’s armed forces in Afghanistan. These are the HMT 400 and HMT 600, a 4x4 patrol vehicle and a 6x6 logistical counterpart called, respectively, in British Army service, the Jackal and the Coyote.
Jamie Clark, the company’s sales and marketing manager, says more than 460 Jackals in three variants and more than 70 Coyotes are now being used by the British Army. The vehicles are in use with three other customers, but the nature of the business is that “we are not allowed to say who they are”, says Clark.
The sheer number of vehicles in service was made possible by a collaborative venture that the company operated during 2007-10 with its much larger counterpart, Babcock, that saw the latter’s plant in Plymouth carry out the bulk of the assembly operations. Supacat, however, emphatically remained the “design authority” with the ultimate responsibility for ensuring that the vehicles manufactured under the arrangement were fit for purpose.
That format could now well provide a model for the future. Clark says that countries in key export markets are increasingly preferring to carry out final assembly domestically. Hence Supacat’s perception of its future as being primarily that of a design, development and prototyping operation with only limited in-house final assembly capabilities of perhaps one vehicle a week, yet one that can form the hub of a high-volume manufacturing set-up.
In practice, this means Supacat is a small company that has to possess many of the attributes of a larger operation. For instance, it already operates the ISO9001 quality management standard and is working towards gaining the ISO14001 counterpart for environmental efficiency.
Supply chain issues also figure large. Managing director Nicholas Ames says the company has around 30 suppliers, mostly in the UK, with sub-systems such as chasses, drive trains and suspension systems – the latter to Supacat’s own design – bought straight in.
Engines, for instance, come from Cummins and gearboxes from Allison. The partnership with Babcock, Ames adds, was a catalyst to Supacat taking a “more analytical” approach to supplier selection. This process, he says, has seen a few of the company’s previously established suppliers “fall by the wayside”.
A concomitant of this strategy is that the company does not require a significant internal resource of manufacturing personnel. Nor does it need to recruit large numbers of assembly staff in response to orders. Instead, it can focus its resources on design and development, and keep them constant with a degree of independence from external factors.
A breakdown of the company’s employees, provided by chief engineer Sean Limbrick, makes the point. He says that just over 30 staff – almost one-third of the company’s total complement – comprise the “engineering team”, with another third as “workshop staff” and the remainder involved in project management, customer support, procurement and administration.
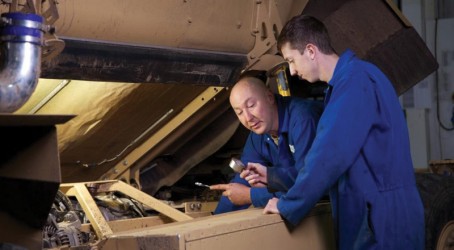
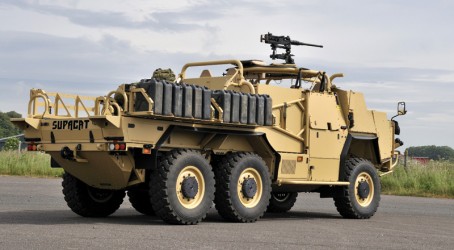
But attitudes and character also play their part. Ames says employees need to fit in with the company’s ethos of flexibility and entrepreneurialism – the opposite of a “big company, bureaucratic” approach. But to achieve the procedural efficiency required to work on equal terms with much bigger partners, the company does carry a slight “top load” of purely administrative staff.
One type of experience that is of particular value to the company is that of life in the military. Seven employees have that experience in their background, including Clark, who was an officer in the Army.
The company has a “rapid prototyping” capability in which the output is not models but “real vehicles”, says Limbrick.
Supacat also makes full use of appropriate design and analysis technologies. The core system for the generation of design geometry is the SolidWorks 3D CAD modelling software, but this is supplemented by several other, more specialist, programs. Limbrick mentions the Hypermesh finite element (FE) system and beyond that – and crucially, given the extreme test to which the company’s vehicles may be subjected – the LS Dyna and Altair OptiStruct programs, which can help model the effects of external blasts on vehicles.
The calculations involved leave no room for approximation, says Limbrick. When a vehicle is caught in the blast of a bomb, then the way it reacts over “the first 10 milliseconds” is what will determine whether its occupants survive.
Armour is crucial and it is a subject on which the company has largely had to educate itself. “We started looking at armour 2007,” says Limbrick, adding that there is relatively little information on the subject that is easily available. For Supacat, then, the way forward was through an iterative process, involving in-house design and analysis with external verification by a specialist external testing house.
“We are confident that we understand what happens,” says Limbrick. “In fact, we think we can now provide the protection in a 7.5 tonne vehicle that previously required one weighing 25 tonnes.”
Both the Jackal and Coyote vehicles look the part, and their specifications are impressive. Jackal has a weight of 5,500kg with an additional payload capacity of 2,100kg. Range is 800km in road conditions with a top speed of 120km/h and an ability to tackle 60 per cent gradients and 35º tilts. For Coyote, the figures are 10,500kg, 3,900kg and 700km with identical speed, gradient and tilt capabilities.
Both can be fitted with extensive horizontal mine-blast protection, mine-blast protected seats and similar vertical anti-ballistic protection. Both feature air-adjustable suspension systems that allow the bodies to be lowered right down to the stops to reduce vehicle height for helicopter transport.
But, as Ames says, the UK’s Ministry of Defence has now “stopped buying trucks”. The consequence is that a company which, over the three years 2008-10 saw its income rise from £14 million to £60 million to £110 million now has to cope with a similarly precipitous decline. Income was down to about £21 million in 2011.
Supacat’s response has been a textbook one: it has sought to develop new products and look for new markets.
The company already has in place the vehicle that it hopes will form the basis of a further batch of sales. This is the SPV400 – a “clean sheet” design for a vehicle that achieves versatility through a high degree of modularity, without compromise to protection. Supacat believes the vehicle sets new standards for survivability of its crew when subjected to explosive blasts despite its restrained, almost innocuous appearance – at least in its initial enclosed “patrol” version without a gun mounting – compared with its aggressive-looking predecessors.
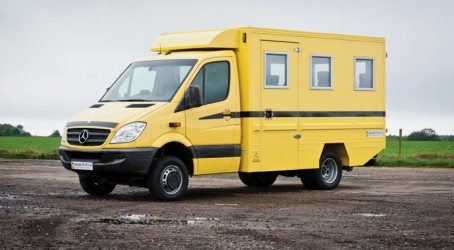
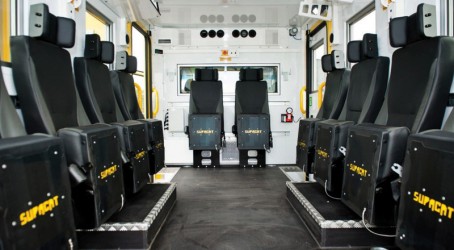
The crew compartment is a separate module sitting on top of an underbody in which the front and rear axles are mounted on sacrificial sub-frames that both absorb and deflect blast resulting from a wheel triggering off a mine. The underside of the hull also forms a V-shape that extends upwards and outwards from a midpoint under the centre of the chassis and terminates directly above the outer face of the wheels, thereby deflecting any blast under the vehicle away from it.
The armour is an integrated blast and ballistic protection system designed by composite materials specialist NP Aerospace. Supacat claims it represents a significant advance over previous steel-based systems – not least in weight saving, but most of all in sheer resilience. In tests, says Ames, it has “survived a blast that would destroy a 20-tonne truck”. The vehicle was unveiled a little over a year ago, and the company is now seeking a launch customer.
Providing protection against blast and bullets also forms a basis for ensuring insulation against more impersonal, but equally hostile, forces. Hence another vehicle that took shape at Dunkeswell last year, the PTV (protected transit vehicle). In appearance, it seems little more than an oblong box with a wheel at each corner, almost like a caravan, but in reality it is a ingenious mix of custom fabrication and off-the-shelf adaptation.
The latter aspect, off-the-shelf adaptation, is represented by the PTV’s chassis – that of a Mercedes-Benz Sprinter van. Custom fabrication is provided by the bland-looking body which is, in fact, an airtight compartment that is capable of slight over-pressurisation compared with the external atmosphere. This is a necessary attribute when that atmosphere contains high proportions of the colourless, flammable and poisonous gas hydrogen sulphide. External temperatures in the projected operating environment also vary across the range, from -36ºC to +42ºC.
The vehicle, says Ames, was the first of a batch of eight ordered from Supacat by oil and gas exploration company Agip KCO for use as personnel carriers to support operations in the Caspian Sea area. As such, the prosaic exterior belies a range of clever technical solutions to the challenges involved.
These include:
- A water-based cooling system for the turbo and exhaust systems, including the exhaust manifold, to help keep surface temperatures below 100ºC in normal operating conditions – and a maximum of 200ºC for all surfaces in all conditions – to stop the vehicle itself causing explosions
- An external gas monitoring system that can automatically trigger the shutdown of unprotected vehicle systems
- Similar automatic closure of external air ingress to the passenger compartment when poisonous gases are detected
- A simple “traffic light” system to provide unambiguous information to the driver on vehicle operating condition and the surrounding environment.
Ames says the initial lead came from Supacat placing an advertisement in an oil and gas trade magazine. A rigorous supplier selection process followed – something Ames feels the company could accomplish because it combines “small company” adaptability in tactics with “big company” thoroughness in procedures.
Then again, achieving that mix of contrasting capabilities in its products – speed and manoeuvrability with robustness and sheer resistance to external forces – is the company’s fundamental purpose. Quite simply, lives depend on it doing so.