Full details of the 122kN (27,000lbs) prototype hybrid rocket that will hopefully fire the Bloodhound supersonic car to speeds in excess of 1,000mph have been revealed, marking a notable step forward for the land-speed record attempt project.
The rocket will be test fired for the first time at an as yet un-named location in the UK in the summer.
The rocket has been designed and manufactured by The Falcon Project, a specialist rocket company based in Manchester, led by 27 year-old self-trained rocketeer Daniel Jubb. It combines solid fuel with a liquid oxidiser to create its power. Although technically demanding, this approach is deemed the safest and most controllable, with driver Andy Green able to shut off the flow of oxidiser and extinguish the rocket if required.
At 4m (12 feet) long, 45.7 cm (18 inches) in diameter and weighing 400kg, the Falcon rocket is the largest hybrid ever designed in the UK. It will burn for 20 seconds per run, during which time it will consume 181kgs of solid fuel and 963g of oxidizer to produce 122kN (27,500 lbs) peak thrust.
This will be in addition to the 90 kN (20,000lbs) of thrust provided by the car’s other main engine – an EJ 200 jet from a Eurofighter.
There are four main elements to Bloodhound’s propulsion package: the solid fuel combustion chamber, the liquid oxidiser and its pumping system, and the associated control system.
The rocket itself consists of a solid fuel made from synthetic rubber (HTPB, or Hydroxyl-Terminated Polybutadiene, similar to that used in aircraft tyres) with metal powders and burning rate modifiers added to the mix. This is contained within a composite case mounted beneath the EJ200 jet engine.
Just as the car design team made extensive use of computational fluid dynamics (CFD) to predict airflow over the aluminium and carbon skin of Bloodhound, so Jubb’s seven-strong team used CFD to model the flow of gasses inside the rocket. They then optimised its performance by varying the composition and geometry along the length of the solid fuel grain.
High Test Peroxide (HTP) is the liquid oxidiser used to burn the solid fuel. HTP is non-toxic and relatively safe to handle. This makes it the ideal choice for use in a land speed record car that will be refuelled in a desert environment during a record attempt.
The need to deliver 963kg of liquid HTP to the rocket in 20 seconds presented a significant technical challenge in its own right. Bloodhound’s solution takes the form of a Cosworth CA2010 Formula 1 engine, mounted to a pump from a 1960s’ Blue Steel cruise missile. Upgraded by the original designer, the pump is now 15% more efficient that its airborne predecessors and able to convert the 800bhp produced by the V8 race engine into 1100lb/in2 (76 Bar) of pressure and a flow rate of 105 lb/sec (47.6 kg/sec) – enough to fill a bath in three seconds.
Prior to commencing a high speed run the Cosworth engine will be started and left idling at between 3000 and 4500rpm. The oxidiser tank will also be pressurised to 24psi using inert nitrogen gas.
With the car accelerating under the power of the EJ200 jet engine alone, Green will engage the engine with the pump via a clutch and gearbox.
Twenty seconds into the run, with the speed approaching 230mph, he will prime the rocket by filling the fuel lines and pump with oxidiser and injecting a small quantity of HTP into the rocket. This will react with a silver oxide catalyst pack mounted in front of the main propulsion chamber to create superheated steam and oxygen. As the solid rubber fuel begins to char in the 600°C temperature, heat haze and black smoke will issue from the rocket nozzle. As low-level combustion starts, this will turn into a powerful flame. The rocket is now primed, ready to deliver full power at Green’s command.
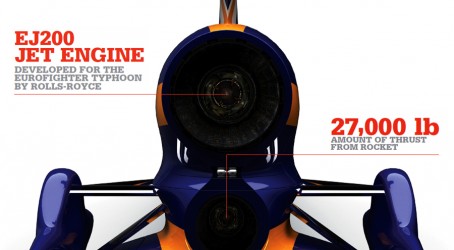
At around 350mph, 25 seconds into the run, the driver will depress the right-hand trigger on his steering wheel, summoning the full force of the Cosworth engine. As the maximum flow rate of HTP reaches the catalyst vast quantities of oxygen will be produced, supporting the combustion of the fuel grain, and generating 27,000lbs of thrust, a 3000°C temperature at the nozzle and a 25-foot long plume of flame studded with incandescent shock diamonds.
After a further 20 seconds of acceleration, at up to 2.5G, the Bloodhound car will have reached its maximum design speed of 1050mph. Once through the measured mile, Green will use airbrakes, a parachute and finally wheel brakes to bring the car to a halt, having covered 10 miles in a mere 100 seconds.
Bloodhound will feature a complex control system designed by Formula 1 systems specialist Dr John Davis. Cosworth electronics and custom-written software watch over key vital signs including HTP tank temperatures and pressures, pump pressure, inlet and outlet pressures, valve positions, rocket chamber pressure and the temperature of the outer rocket casing along its length.
In the event of an abnormal reading the control system will automatically shut down the supply of oxidiser, thereby extinguishing the rocket. Green will also be able to shut the rocket down manually.
The three-year long development of the hybrid rocket has had a major influence on the overall design of the car.
In early configurations it sat on top of the larger, heavier jet, the rationale being to keep the centre of gravity low to aid stability.
As the aerodynamic modelling data from Swansea University’s super computer revealed in ever increasing detail the herculean power needed to reach 1000mph, the rocket increased in power and size.
By late 2009 it became clear that the enormous thrust from the now 400kg rocket would pitch Bloodhound’s nose downwards, thanks to its position high above the centreline of the car. This would increase steering loads, reduce the weight pressing down on the back wheels and disturb the airflow over the rear of the car, potentially causing lift.
The decision was taken to redesign the entire rear section of the car and mount the rocket underneath the jet, which is the position it occupies now in the final build configuration.
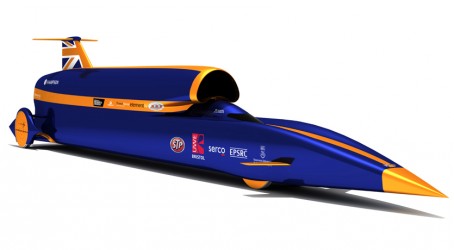