When the Bloodhound supersonic car is unveiled at Newquay airport in Cornwall on 26 October 2017, it will be the most important milestone of the project so far.
Thousands of visitors are expected to witness the car hit 200 miles per hour on the 1.7 mile runway. The Newquay runs will provide vital data on Bloodhound’s performance and give the driver, Wing Commander Andy Green, a chance to get a feel for the car. They will also let the team practice the procedures for the car’s record-breaking run at Hakskeen Pan, South Africa, next year.
Fittingly, Bloodhound’s first run on 26 October also coincides with when its predecessor, Thrust SSC, became the first land vehicle to break the sound barrier in 1997, when it reached 763mph at Black Rock Desert, Nevada.
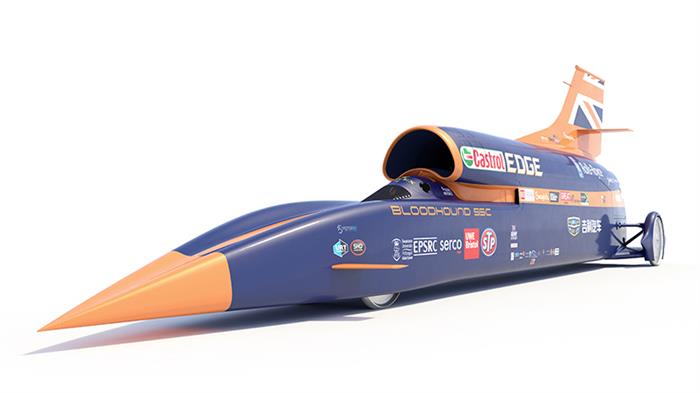
Cost and time
It seems almost fated that Bloodhound’s first run coincides with Thrust’s 20th anniversary. But, the symmetrical timing wasn’t part of the initial plan. Bloodhound was originally planned to have completed its 1,000mph run in 2012.
Therein lies one of the most apparent and contentious differences between Bloodhound and Thrust – the time and cost of each project. Bloodhound’s total bill stands at around £60 million – so far – after almost ten years. Thrust SSC cost £2.48m and took five years to design, build and run.
It’s a difference that has been high on the agenda for the Bloodhound management team and causes some consternation with Ron Ayers, chief aerodynamicist of both Bloodhound and Thrust SSC.
“They are very different cars is appearance, philosophy and objectives,” he says. “There a lot of contributing factors to why Bloodhound costs more and is taking longer.
“I get a bit fed up with the comparisons because it gives Bloodhound SSC a bad reputation and makes it look like the engineers don’t have the project under control.”
As the main designer behind both cars, Ayers has an in-depth knowledge of both cars. He has been preparing a report that analyses and explains the reasons for the differences in the cost and duration of the Thrust and Bloodhound projects. The report compares the two cars and their development.
-small.jpg?sfvrsn=e066db12_2&MaxWidth=700&MaxHeight=400&ScaleUp=false&Quality=High&Method=ResizeFitToAreaArguments&Signature=DEF4857755F44E634F9558FF5DFA108E)
The 1,000mph difference
One of the largest reasons for the higher cost of Bloodhound is that with Thrust there was no rocket to develop. Engineers were also able to use “orthodox” off-the-shelf technology to achieve Thrust’s 763mph.
Bloodhound is shaped like an arrow, and is powered by an EJ200 jet engine, as used in the Typhoon fighter aircraft, and the hybrid rocket motor developed by Nammo, which sits on top of the jet engine. There is also an 800bhp Jaguar engine, which drives a pump to supply high test peroxide (HTP) to the rocket, and delivers hydraulic power to the jet engine.
Bloodhound’s cockpit, where Andy Green will monitor and control the car, is below the intake for the EJ200. Bloodhound also uses front-wheel steering.
The setup is very different from Thrust’s, which used twin Spey 202 afterburning turbofan engines from Rolls-Royce and rear-wheel steering, with the cockpit in the middle between the engines.
“The design is radically different because I had a decade to think about how I would improve it after Thrust,” says Ayers. “I knew a rocket would be needed and that a combination of a jet engine and rocket would be essential if the car was going to be developed in the UK, so we could do the research and testing in this country cost-effectively.
Thrust was also designed, built and run by a much smaller team of mostly volunteers, with more “in-kind” contributions. Bloodhound’s team is much larger, with people running and involved in the education outreach program, media, marketing and sponsorship management. “Thrust had a low cost base, so much of the funds could be raised below the radar. There were no large sponsors on board that could promise money, then change their minds and let us down,” says Ayers.
Engineering approach
As a technical project, the approach to Bloodhound’s development and manufacture is fundamentally different to the approach that was taken with Thrust SSC. Where Bloodhound is tackling lots of difficult engineering challenges to reach 1,000mph, which demands brave decisions and extensive R&D, Thrust’s engineering and design was more cautious.
“Engineering and design decisions were always defensive with Thrust. We’ve had to be a lot more aggressive with Bloodhound,” says Ayers.
The cautious approach to Thrust’s development was borne from the relative poverty the small team was working in, he explains. “The first line drawing was the final one, and the final car was the first prototype. We could only afford to use technology we were comfortable with.
“Thrust was designed so nothing was hardwired and so that it was overpowered. We didn’t try to integrate systems in the same way as Bloodhound does, so we could change individual parts easily.
“We were only concerned with being the first to break the speed of sound with Thrust. Bloodhound has different aims. We started it to inspire a new generation of engineers, not to increase a record, which could well stand for a very long time as no-one else shows signs of breaking it.”
The defensive decisions and use of established technologies also meant the Thrust team were certain that its engineering would stand up to the rigours of breaking the sound barrier. Lots of test procedures, done to aviation standards, also instilled confidence in the design. “We were confident in our abilities, but we were also confident that there would be things about breaking the sound barrier on the ground we didn’t yet know about,” says Ayers.
That same level of certainty has not existed from the outset with Bloodhound. The project has been much more about engineering “unknowns”.
“We started from scratch and we ditched all the cautious assumptions we had made with Thrust. We expected to evolve Bloodhound’s design as we progressed,” says Ayers. “Safety assumptions have never been relaxed, but we knew it would be tough. We’ve always called it an engineering adventure to see if 1,000mph on land is possible.
“It’s been a very different approach with Bloodhound. We started off knowing we were going to have to use cutting edge technologies to reach our objectives We’ve done a lot of research.
“It took three years to define exactly a car shape that was satisfactory.”
Industrial partnerships
The scale of the challenge is so much greater with Bloodhound than Thrust, it has also been necessary to closely partner with engineering companies, who have supplied industry-leading technology and expertise to solve Bloodhound’s many challenges, such as the wheels.
For Bloodhound’s Newquay airport runs, amazingly, the same tyres that were used on Thrust SSC and its predecessor, Thrust 2, will be used. The tyres, which were originally developed for the English Electric Lightning jet fighter by Dunlop, were made in 1979 and have been checked by the company that they can still be used.
However, the steel high- speed “desert wheels” which will be used for the runs at Hakskeen Pan are very different. Each weighs 95k and have been designed and rigorously tested to spin at over 10,000rpm and be subjected to a force of 50,000G at the wheel rim. [http://www.bloodhoundssc.com/project/car/wheels/desert-wheels]
The wheels were developed by Lockheed Martin UK, made by Castle Precision Engineering and tested by Rolls-Royce. “It turned out we can produce wheels that will go 1,000mph but only if we partner with Rolls-Royce and Lockheed Martin,” says Ayers.
Running and stopping
Although the reaching of 1,000mph and then stopping is a massively different design driver compared to Thrust SSC’s breaking of the sound barrier, it’s not the only factor that has influenced Bloodhound’s design. Just as importantly, if not more so, is that Bloodhound is designed to achieve its maximum speed over a significantly reduced distance. This is because the 30 mile track used for Thrust SSC at Black Rock Desert is no longer available.
“It’s a key design constraint with Bloodhound that we didn’t have with Thrust,” says Ayers. “We had 30 miles to build up speed and come to a stop with Thrust. The Hakskeen Pan track is only 12 miles long. That’s 5.5 miles to accelerate, followed by ‘the measured mile’, and then 5.5 miles to decelerate, averaging 1.15G all the way.”
“It also means that the air brakes have to be of a higher standard of safety, because we’ve got to stop in such a limited space.”
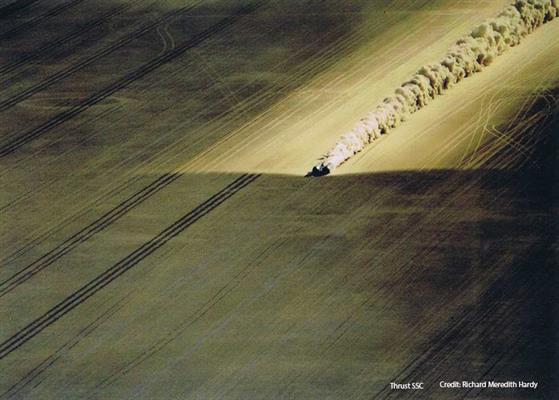
Tools and materials
Challenges such as the reduced run distance have required modern design tools to overcome. Computer simulation is probably the most important tool at Bloodhound engineers’ disposal that wasn’t available to the same extent for the Thrust SSC team.
Computational Fluid Dynamics (CFD) has underpinned the evolving design of the Bloodhound car, its structural changes and the design method employed. “We are pushing the boundaries of CFD with Bloodhound,” says Ayers, “Swansea University are now world leaders in CFD thanks to the knowledge and expertise built up for the Bloodhound project.”
Ayers says they could have tried to design and build Bloodhound immediately after Thrust in the 1990’s, but that they would have probably failed. There were several things the team learnt about breaking the sound barrier in Thrust that could be applied and mitigated for in Bloodhound’s design.
He says: “There was a series of lessons to learn from Thrust. It was only by running Thrust that we discovered that shockwaves from breaking the speed of sound affect the surface and that the dust thrown up added four tons of drag. This allowed us to use CFD in Bloodhound’s design so that shockwaves do not affect the surface.”
The two cars also use very different materials. Thrust has a welded steel space frame, because of the cost and because you can cut and change steel more easily than other materials. This was one of the “defensive decisions”.
Bloodhound uses composites and light alloys needed to reach its target speeds, which can’t be cut, shaped and changed in the same way. “It means you have to commit fully to the design,” says Ayers.

Maximising the legacy
Once Bloodhound’s run has happened, the team’s work will also not stop in terms of the educational outreach program, which aims to inspire young people to become engineers.
This outreach program is in many ways a result of Thrust SSC. For many years after the car successfully broke the sound barrier, Ayers says he would meet engineers and students who were getting into the profession because of Thrust.
However, the “halo” effect of inspiring people into engineering was an accidental side-effect of the endeavour. A key difference with Bloodhound is that the team has had the aim of maximising the inspirational effect from the start of the project.
In the last year, the Bloodhound education outreach program has engaged with more than 110,000 school children through its network of ambassadors. “That’s personal interactions, not through a screen,” Ayers is keen to stress.
Other evidence that the “Bloodhound effect” is creating the legacy of young engineers the country so sorely needs can be found at University level. Swansea University’s engineering department, which has pioneered the advanced Computational Fluid Dynamics (CFD) simulation work used in Bloodhound’s development has trebled in size, says Ayers. The University of West England has maxed out its student intake this several year, he adds.
“We know we are having the effect we want to have. I’m absolutely satisfied we are inspiring more people to become engineers with Bloodhound than we did with Thrust. It was an accident with the first one, now we have gone out to maximise the effect.”
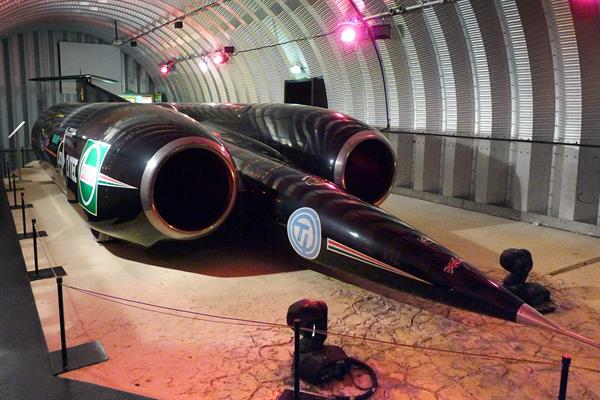
Bloodhound vs Thrust
But the question that begs to be asked of the man who has played such a key role in the development of both vehicles – is which he likes best?
The answer is typically equivocal – Ayers says he has enjoyed working on Bloodhound as much as Thrust, “I enjoy the technical challenge, but they are so different, I wouldn’t like to make the comparison in that way.”
He is also diplomatic about which will be remembered as the greater success. “I’m too close to the project to make that type of an assessment of the cars. Besides which, it’s probably better to make that assessment after Bloodhound has run.
“When we all finished Thrust, we all said never again. But here I am now on my third. Breaking speed records is addictive.”
The addictiveness, passion and adventure of breaking the land speed world record is perhaps the strongest similarity between two very different cars. That Bloodhound aims to communicate and inspire that passion and addictiveness for engineering so explicitly from the outset of the project, is perhaps the biggest difference.
Find out more about
Bloodhound's Newquay run