It’s the smell that tells you that the Morgan car plant in Malvern is very different from any other. It’s a heady mix of leather and wood, two of the vital components of everyday operation. Then you’re hit by the quaintness of it all: craftsmen in well-worn overalls using traditional tools to piece the vehicles together carefully, bit-by-bit.
But appearances can be deceptive. Morgan might be famed for the classic styling of its cars and employ a coach-built approach to manufacture, but it’s all underpinned by the latest technology that enables the firm to remain competitive.
Most recently, Morgan has invested heavily in visualisation software to help it go from sketches to first production of new vehicle models in just a matter of a few months. And other innovations, such as the use of magnesium alloys and alternative powertrain technologies, are also in the pipeline.
Managing director Charles Morgan says the success of the company in recent years can be attributed both to its agility and its ability to embrace technology. “Although we are steeped in history, we pride ourselves on the fact that we are quite innovative,” he says. “That’s particularly the case with the materials we use: we started with super-forming, which was an aircraft technology that we brought into the industry to make an aluminium car, and we have moved forward with a bonded chassis. To back that up we need the latest software to keep designing cars relatively rapidly. We have set ourselves a task of bringing out new models even perhaps a bit quicker than most of the major manufacturers.
“We have a very small team here but that’s good in a way, it means we are very focused. Our designers and engineers are always thinking about the whole car, rather than just, say, the door hinge.
“Generally speaking I’d like to think we are respected throughout the industry as producing fantastic cars, especially considering our size.”
Morgan, which was founded more than 100 years ago, is going through a golden period at the moment, with near-record production levels of 1,200 cars a year. Its range of traditional roadsters, Plus 8 sports cars and four-seaters is now complemented by more modern interpretations of its design philosophy as characterised by the Aero Supersport and Coupe. Perhaps the biggest surprise has been the popularity of the new 3 Wheeler, which is a reworked version of a Morgan classic, fitted with a V-twin fuel-injected engine and Mazda five-speed gearbox that delivers acceleration times of 0-60 in under 6 seconds.
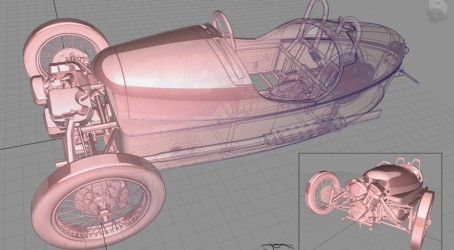
The 3 Wheeler, which is priced at around £25,000, has sold extremely well since it was launched in 2011, and as a result the Malvern facility is bursting at the seams. “We didn’t expect the 3 Wheeler to be such a huge success,” admits Charles Morgan. “We were thinking that we would sell 200-250 a year, but in reality we are now looking at producing quadruple that number.”
The immediate challenge, then, is to meet this soaring demand while retaining control over quality and ensuring that lead times don’t become too stretched – they now stand at 3-6 months, but in the past have reached several years. The solution might be to make greater use of the local supply chain, which could produce larger subassemblies.
“One of the challenges going forward, particularly if we have a big success with a smaller, more practical type of Morgan, will be manufacturing,” admits Charles Morgan. “We have been looking at using the West Midlands as a source of manufacturing to ensure we can make the volumes required. People want to see a car come out of Morgan, and they want our assemblers here to have a hand in it, but in truth we might have to use a lot more subassembly.
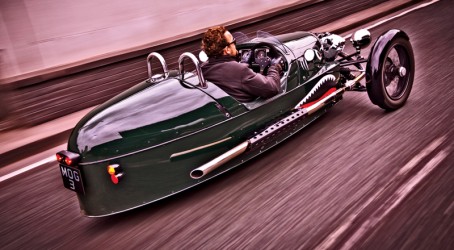
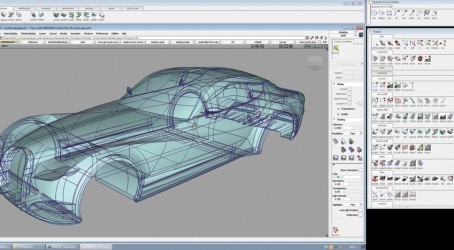
“Fortunately, places like Coventry and Birmingham have a lot of capacity for sheet-metalwork with some really good laser-cutting equipment. It would be my first choice to use them rather than manufacturing sources abroad.”
Another area where Morgan has made changes in recent months has been with the greater use of visualisation software, primarily to help accelerate time to market for new car models. Indeed, Autodesk software helped it to go from sketches of its new 3 Wheeler to first production in just five months and to meet deadlines for marketing material before the car was actually produced.
According to Jon Wells, senior designer at Morgan, the company was too reliant on the use of 2D sketches, which were interpreted by eye into panel-beaten aluminium bodies – a time-consuming process requiring high skill, while providing little margin for in-process evolution. Now the company uses Autodesk Alias software to rapidly transform concept ideas into 3D digital prototypes and then into concept cars. Visualised using Autodesk Showcase and 3ds Max software, designs can be refined until they are well-established. The surface data is then five-axis machined directly from the Alias data. Once painted and scanned, this model enables further evaluation and adjustment to be made in Alias software.
“The skills and charm of traditional coachbuilding are not lost at this point,” says Wells. The Alias model is then chopped into cross-sections and an accurate 3D wooden buck produced. Skilled panel beaters accurately replicate the surfaces in sheet metal and then paint and lower the body over one of the existing platforms. “The concept car is born and ready to be exhibited worldwide,” he adds.
Autodesk software also helps to meet tight media deadlines that precede completion of the concept car. Photo-realistic visuals are generated in Autodesk Showcase and 3ds Max software to launch the concept to the press and to build excitement.
Once the car is ready for the product development stage, the Alias surfaces are modelled to class A standard, passed to Morgan’s engineering department, and used to manufacture the tooling for the panels at production.
“Although Morgan cars are known for their retro style and quality workmanship, we also need to take the best from the latest technology to enable us to be competitive and keep up with the demand for new ideas,” says Wells.
Those new ideas are coming thick and fast. Perhaps the most ambitious is the launch of the Plus E concept, an electric sports car designed by Morgan with the support of technology specialists Zytek and Radshape. The car is based on a tailored version of Morgan’s lightweight aluminium platform chassis clothed in the revised “traditional” body from the V8-powered Plus 8. Power is delivered by a derivative of Zytek’s 70kW (94bhp), 300Nm electric engine, which is already proven with US vehicle manufacturers.
Mounted in the transmission tunnel, the Zytek unit drives the rear wheels through a conventional five-speed manual gearbox. The clutch is retained, but because the motor provides torque from zero speed the driver can choose to leave it engaged when coming to rest and pulling away, driving the car like a conventional automatic.
Morgan says that a multi-speed transmission allows the motor to spend more time operating in its sweet spot, where it uses energy more efficiently, particularly at high road speeds. It also allows the car to provide lower gearing for rapid acceleration.
The Plus E programme will deliver two engineering concept vehicles. The first, with the five-speed manual box and lithium-ion batteries, will be used for preliminary engineering assessment while the second will be closer to potential production specification, with alternative battery technologies and possibly a sequential gearbox.
“The Plus E is interesting because of the number of green zones coming into use around the world,” says Matthew Humphries, chief designer at Morgan. “If you have got to have Euro 5 or 6 to go into London, for example, then many classic cars will be instantly taken out of the equation. It will be great for us that customers will be able to buy a modern classic and will be able to use the car where they want.”
Humphries says that the Plus E will combine Morgan’s traditional look with a powertrain that delivers substantial torque instantly at any speed, making it fantastic to drive. “The manual gearbox and electric motor means drivers will get the best of both worlds: top speeds, acceleration, as well as distance, while being fun to drive. It’s a very fast car.”
Progress is also being made in the area of new materials. Morgan is running a project to develop appropriate technologies to enable magnesium alloy to be used as the primary material in the construction of a body-in-white structure to produce improved performance at reduced weight. Magnesium is the lightest structural metal available, 30% less dense than aluminium.
The use of sheet magnesium for vehicle structural applications will require hot-forming, which is increasingly being adopted by premium carmakers as it can produce larger and more complex panels. Morgan says it intends to provide the initial route to market by adopting the developed technologies on its next generation of premium sports cars, becoming the basis of a new UK manufacturing supply chain.
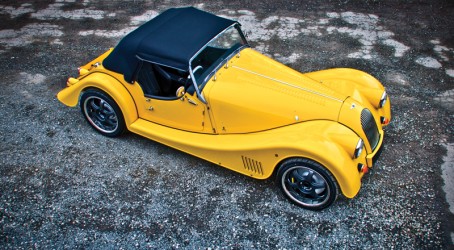