Pod cast: RDM aims to produce its first pods by the end of 2014
If driverless cars are one day seen en masse on the streets of Coventry, RDM Automotive will be able to claim some of the credit. The supplier, based at the city’s Bilton Industrial Estate, is the manufacturing partner for the Low Carbon Urban Transport Zone Pathfinder project, which will see electric-powered pods used in Milton Keynes next year. RDM, which works closely with OEMs and suppliers in the West Midlands automotive industry, was selected by the Transport Systems Catapult – part of the public/private group of innovation centres – following an open tender process. It will work with Oxford University’s mobile robotics group to create three vehicles.
For David Keene, who founded the company in 1993 when he was just 29, being involved in the project is more than just a speculative exercise. “It’s interesting, but not superfluous – there are lots of applications where people will want those pods.” For example, they could be used in airports to transport passengers between terminals. Keene adds: “In 10 years’ time, when Jaguar Land Rover has an autonomous vehicle, there’s no reason why we couldn’t supply the systems or the products.”
RDM’s story over the past six years has been one of survival and renaissance against the odds. When the financial crisis hit in 2008-09, the automotive sector in the UK suffered dreadfully – many suppliers in the West Midlands went to the wall. RDM saw JLR, its biggest customer, decide it didn’t want a particular product for a period of nine months. “We went from a load of orders every month to virtually nothing. We survived, so obviously we had something. But it was a massive drop,” says Keene. Turnover shrank by £800,000, from £2.5 million to £1.7 million during 2009. Keene had to ask RDM’s workforce to take a 10% pay cut and reduce working hours.
The prospect of a further cut loomed, says Keene, but never materialised. The measures taken meant the company survived, and when OEMs started looking for suppliers again, RDM was able to mop up some of the work from companies that had gone bust. The key was “hanging on to our people”.
Since that period, RDM has thrived, with turnover recovering to hit a record
of £3.1 million in 2010, and another record of £4.4 million in 2011.
This financial year, turnover is expected to hit a staggering £8 million. Staff numbers have doubled from 24 to more than 40 people since the crisis, with RDM able to attract new members easily enough until “JLR started hoovering everyone up,” according to Keene.
Such expansion is a sign that the sector has recovered well – but it brings its own problems. When times are good, the OEMs pay wages that the suppliers can’t match, so there’s the chance of losing valuable staff to bigger companies.

Chamber music: Howard Andersen (left), deputy chief executive of Coventry Chamber of Commerce, and his colleagues aim to boost manufacturing
The health of the automotive sector in the West Midlands is good for Coventry, which relies heavily on it. According to Howard Andersen, deputy chief executive of the Coventry and Warwickshire Chamber of Commerce, manufacturing supports 44,000 jobs in the county, sustained by around 12,000 engineering firms. Automotive sector employment in the region is five times the UK average.
“All the indicators are that this figure is set to grow”, says Andersen. He has set
up an initiative called the Clearing House at the Chamber to help manufacturers
and other firms access support such as from the Manufacturing Advisory Service (MAS) and UK Trade and Investment.
To give firms advice at the Clearing House, specialist account managers are on hand. These include a former managing director of Coventry steering systems firm Pailton Engineering, and a manager seconded from MAS.
The aim, over time, is to help firms create scores of new jobs – perhaps as many as 9,000 extra advanced manufacturing and engineering positions in Coventry and Warwickshire by 2025, says Andersen. “It’s a jungle out there when you’re trying to run a business. It’s making sense of everything that’s out there and putting it in a form where it can be understood by a business owner, particularly those with small firms.”
He adds: “Traditionally manufacturing has been at the heart of Coventry and Warwickshire. During a recession, it’s a case of holding on to what you’ve got and surviving. As things pick up, we want to get behind the sector, and do what we can to increase its resilience.”
For RDM, an important part of that process is involvement in the Automotive Council, which was set up at the height of the crisis in 2009 by former business secretary Lord Mandelson and is now chaired by current business secretary Vince Cable. The popularity of the council’s introduction can be measured by the fact that Labour has said that it will persevere with the council should it win next year’s general election, along with other elements of current industrial strategy.
If the council was to be scrapped, the reaction wouldn’t be good, says Keene.
“If Labour didn’t carry on with it, a lot of influential companies would be really surprised,” he says. The forum gives suppliers such as RDM, and many other small firms, an unprecedented level of access to and influence on the OEMs, which include council members JLR, Honda, Nissan, Toyota, Aston Martin, Bentley, and so on. “Before the crisis, the automotive industry was quite old-fashioned in the way it did things,” Keene explains. “There was no real collaboration going on. If you were selling something for a pound and someone else said they could do it for 99p, companies would look at it.”
All this changed during the crisis, Keene says. “The recession rocked the automotive industry. OEMs realised the role of suppliers was more than just supplying goods. If every company making exhaust systems or electronic control systems goes bust, where’s a vehicle maker going to get the supply from if it’s not indigenous? Holding out on the supply base in critical areas isn’t any good for the supply base, isn’t any good for the OEMs, and isn’t a lot of good for employment throughout the UK.”
Fortunately, Mandelson recognised that something needed to be done, says Keene, who praises the former business secretary’s attitude to manufacturing. “For all the negativity, I thought he was extremely good. Mandelson was inspirational. To have a politician saying ‘We can’t rely on the financial sector and we need to make stuff’ was really interesting. It was also really interesting that someone thought automotive was important. In the dark days of the 1970s and 1980s, automotive and manufacturing were basically jettisoned.”
This change of approach is echoed by Andersen. “Manufacturing had a bad press. It was thought of as yesterday’s industry – and that was wrong. We’re now making more cars than we did when we had British Leyland and Rover.”
Keene now acts as a voice for automotive suppliers on the council. “At the lower tier, getting into a big OEM is really difficult,” he says.
Larger suppliers such as Unipart Manufacturing may make themselves more easily heard, but they can suffer from the same problems that afflict companies lower down the chain, such as a lack of skilled engineers and manufacturing personnel in the recruitment market.

Training ground: An artist's impression of the AME building that opens this month
Unipart’s joint venture with Eberspächer in Coventry, which produces exhaust and fuel systems, will host a new Institute for Advanced Manufacturing and Engineering (AME) that will train undergraduate and postgraduate engineers from this month. Unipart hopes that many of these students will go on to become its employees.
The project, which is being funded by the Higher Education Funding Council for England and Unipart, and is running in conjunction with Coventry University, will train students studying for a BEng, MEng, one-year MSc or PhD in practical shopfloor skills, using some of the latest automation, manufacturing, metrology and machine tool technology. The aim of this ‘faculty on the factory floor’ is to develop industry-ready engineering graduates. The success of the scheme will be measured in the number of graduates who go on to engineering careers, and the number of jobs created in industry as a result of research and innovation at the AME.
For Unipart, the initiative could mean that skills gaps at the company in the future are filled more easily, although students won’t be obliged to work there.
Dr Carl Perrin, director of the AME and a former Rolls-Royce chartered engineer, says: “These’s no benefit in people studying for three years and all this investment going into the institute, and then them leaving and going on to do something else.” However, he believes their prospects should be better now than in recent years. “I can remember when it was difficult to find a job in manufacturing because the sector was contracting,” says Perrin. “Now we are reversing that.”
The equipment at the centre will be state-of-the-art, and focused on joining, forming, measurement, product verification, metallurgy, automation, simulation and computer modelling. “All of these are important to the Unipart business today,” says Perrin. “It’s really a strategic flow.” But it wasn’t thought necessary to replicate standard technology. “The equipment Unipart has can do the job well, but they want to do it even better, and this facility will give them the opportunity to do that.”
Students might innovate manufacturing processes and technologies, he suggests, and these innovations could ultimately feed into Unipart’s business. The AME may also help to bridge the gap between early-stage and commercially useful technology. Perrin believes there’s often a gulf between early-stage technology and its further development, later down the line.
In terms of skills, the company often hires people with good generic capabilities and trains them to do specific jobs.
“For joining and forming technologies such as welding, it can be difficult to find someone with the right track record and a good CV. What we tend to do is hire people who have a good attitude to work and a good engineering background and then train them up,” says Perrin. The theoretical study of engineering is different from its practice on the shopfloor, he says, and it’s this divide that the AME aims to bridge. “From an academic point of view, working on a PhD is a very different process from working in industry.”
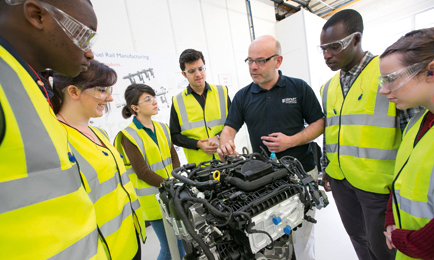
Factory floor: Coventry University students learn new skills at Unipart
Students will spend most of their time at the AME – three days a week – and the rest at Coventry University. The links to the campus and ordinary student life are important. One research project will look at producing components with ‘zero prototyping’, says Perrin – or designs that are as manufacturable as possible. A possible outcome could be new types of exhaust with lightweight characteristics that retain good acoustic performance.
“Unipart want to move to no prototypes at all and to get the design right first time. Design for manufacture is really important. We can come up with beautiful, elegant designs, but the real question is – can we actually make them?” Still, none of this will be possible without high-calibre staff. “People are the heartbeat of the business, and without good people we don’t have one,” says Perrin.
Another hub of innovation is Coventry’s Manufacturing Technology Centre (MTC), housed in a 12,000m2 purpose-built facility at Ansty Park, which was opened in 2011 and founded by the University of Birmingham, Loughborough University, the University of Nottingham and TWI. At another MTC site in Coventry is machine tool firm Hybrid Manufacturing Technologies (HMT). The company has developed a machine-tool technology that combines additive manufacturing in a traditional subtractive machine to combine the speed and relative low cost of machining with the design flexibility of ALM.
Engineer and machine tool specialist Peter Coates runs the company with business partner Jason Jones, who manages the firm’s operation in Texas. Coates says the project grew out of a Technology Strategy Board-backed research scheme originating at Leicester’s De Montford University.
“In 2008, there was a concept to integrate 3D printing in a milling machine, but it was something that stayed in university-land for a time.” But Professor David Wimpenny, now technology manager for Netshape Manufacturing at the MTC, and Jones realised they could combine a laser cladding head in a milling machine to lay down material, combining additive and subtractive processes.
HMT’s aim is either to retrofit existing machine tools with the technology or to license it to machine tool firms so they can incorporate it into new designs. Coates says the technology could help to alleviate some of the problems with ALM, such as poor finishes requiring subsequent machining and slow build rates. One promising application is in the repair of aeroengine turbine or turbocharger blades. Some other firms are working on similar concepts, but the idea has yet to become mainstream, says Coates.
It proved impossible to patent the idea of combining the two technologies together, but there is intellectual property in the company’s tool, which is produced by local suppliers in Coventry and features four separate powder ports, two individual argon gas ports, and a patented docking system. The powder ports allow different metal powders to be mixed on the fly. It’s also possible to closely control the rate at which powder is laid down, saving material for different parts of a component with different thicknesses or geometries. The system’s laser can also be used as a drill to remove material, burning holes while gas blows away debris.
Where the machine excels is in taking a substrate or a big existing part and adding a small amount of material, explains Coates. For example, forgings can be made and then have extra features added using the technology. “The trade-off is that building a new component layer-by-layer from scratch is a slow process, it’s low-quality, and it has a lot of stress in it.
“If you can CNC barstock, on the other hand, all that technology is relatively well understood – the machines are efficient at doing that. You can add on the features you want using a 3D printing technique. You can buy a cheap four- or five-axis machine tool that can mill all day and something that can produce ALM parts.
It’s a more stable structure.” However, adding HMT technology to a standard tool might bring it up to the cost of a typical ALM machine, he says.
Being based at the MTC is important for the company. “We wouldn’t exist if it hadn’t been for the TSB-funded project and the MTC Catapult Centre,” says Coates. “This is a technology developed in the Midlands, produced in the Midlands – and now sold in the Midlands.” In his other job, Coates runs a firm specialising in repairing machine tools all around the world. “My background enables me to integrate equipment into existing machines,” he says. “We have those skills in Coventry. Laser cladding has been around for years, but bringing it into a machine tool is relatively new. The big challenge is to take all the different available elements and successfully integrate them together.”
Coates believes that the machine tool industry in the UK has pretty much disintegrated. Even if the machines are imported from overseas, technicians who can support them are required. “You can take apprentices who know how to load a CNC machine, program it, and cut parts. They don’t know how to make anything. The toolmakers are the missing part of the puzzle – that’s the problem. The machine tool repairers are missing.
“But to support manufacturing, you need to be able to support the machine tool sector. Those specific skills exist in many other countries – but they don’t necessarily exist in abundance in the UK.”
If cities such as Coventry and the surrounding region are to continue to thrive, they need support. Keene of RDM singles out Milton Keynes Council for praise in that it’s willing to encourage technological developments such as driverless vehicles. “Nothing fazes Milton Keynes. They will take a risk. Coventry will also take a risk.” He says the city has improved since the automotive industry’s decline in the 1980s. “If you walk into Coventry city centre now, you won’t find a bombed-out, reconstructed 1960s concrete jungle. Masses of money has been invested in redevelopment, which makes it a nice place to live and work.”
Andersen of the Chamber of Commerce says the city has the infrastructure to succeed. “We have everything in place, including JLR and customers, the skills base, and the supply chain. We also have two prime universities in Coventry and Warwick. The driving force behind economic recovery has to be engineering and manufacturing.”
RDM is due to deliver its first autonomous pod at the end of the year, and will produce the majority of the vehicle. The pods will drive independently of each other initially, but may ultimately be used in platoons.
“We want to end up being a company that can provide these systems to manufacturers,” Keene says.
RDM will be hoping that it plays a significant role in the future of a British automotive industry – and manufacturing more generally – that was so cruelly ignored for so long by so many.