These are troubling times in the offshore sector. Ongoing high supply has seen oil prices fall 70% from 2015 peaks, down to $30 a barrel. Some energy industry analysts think this figure could go much lower, even as far south as $10.
Such a drop is forcing the industry into a period of reflection and restructuring as it faces a new reality in which operating returns are ‘lower for longer’. Shell has abandoned its Arctic development plans, while BP has cut $6 billion in operating costs and is planning to sell $3-5 billion of assets over the next two years.
Pressure to cut jobs
Difficult decisions are having to be made across the board, and this pressure on operators is being pushed down the supply chain, affecting everything from headcounts to new infrastructure projects.
The challenge for the offshore sector is how to balance cost-cutting programmes with the need to ensure that safety standards don’t drop. There is a temptation among operators to postpone or shelve maintenance activities at a time when financial pressures are being felt.
Koheila Molazemi, a risk management adviser at DNV GL, the international certification body and classification society, worries that there are already signs that costs have been cut in the wrong areas by some companies. “We can’t lose sight of the requirement to make sure assets continue to operate safely,” she urges in a DNV GL report on the offshore sector published last month.
“Any of the cost savings that these companies are considering would be dwarfed by the costs associated with a major accident. I would encourage the industry to ensure that the cuts they are making are sustainable.” The cost of not addressing this, says Molazemi, is the risk of another incident like the Macondo deep-water oil spill in the Gulf.
Indeed, there is anecdotal evidence that financial pressures are already impacting on attitudes towards safety. Some MPs with large numbers of offshore workers among their constituents have been voicing fears that the North Sea sector is using the oil price slump as an “opportunity” to postpone or shelve some maintenance activities. And there are also worries that the threat of job losses mean workers could turn a blind eye to safety concerns for fear of being labelled as troublemakers.
Alex Cunningham, the MP for Stockton North, has been vociferous on this issue. “I talk to a lot of employees in the oil and gas industry, and to union representation at the RMT, and they tell me that there has been a change in attitude towards safety,” he says. “There has been a huge increase in the number of applications to delay maintenance work, or to get some form of exemption. This is very worrying.”
Cunningham also says that he has been made aware of workers being less prepared to make challenges about safety concerns. “Issues are not being reported to the extent that they might have been,” he adds. “There have been a lot of job losses recently, and people are worried about that. This lack of engagement with safety representatives is something that needs to be addressed. We cannot risk a return to some of the horrors of the past.”
In fairness to the North Sea sector, safety performance in recent years has continued to improve. Major and significant hydrocarbon releases, which are a key indicator of asset integrity and maintenance quality, decreased by 60% between 2009-10 and 2014-15. In addition, there have been year-on-year reductions in reportable dangerous occurrences. Sustained levels of good occupational safety performance mean that the oil and gas industry now claims to be safer than many significantly less hazardous sectors.
Mick Borwell, health and safety director at trade association Oil & Gas UK, says that good maintenance is essential to achieving high standards of safety and operational performance. He says that poor maintenance regimes make no business sense, as they result in asset shutdowns, with severe cost implications. “The current business climate makes good maintenance even more important, as the drive for efficiency improvements is heavily influenced by equipment reliability affecting production uptime.”
Crucial role of maintenance
Borwell argues that maintaining plant and equipment is crucial to the industry’s goal of maximising recovery, particularly in a mature basin where coping with asset ageing and life extension are daily operational challenges.
“There is no business or safety benefit to be gained by allowing maintenance standards to be diminished,” he says. “If we don’t maintain the kit it is almost certain to fail at some stage and we are then faced with production losses and unplanned repair costs. Setting aside the industry’s focus on effective maintenance, the North Sea regulatory regime is regarded as world class and works to ensure that installation operators stay on top of plant and equipment maintenance and manage major accident hazards.”
Borwell says that North Sea companies are always striving to identify better ways of optimising safety-critical maintenance. The management of ageing assets and the ability to extend their operational lifespans is crucial to maximising the life expectancy of the sector.
Maintenance efficiency improvements are being sought in several areas, such as refining contracts and materials management to improve work flows and reduce downtime. Operators are also reviewing equipment performance standards and associated assurance and maintenance routines to make sure they are aligned and are not duplicating effort. There are efforts to upskill core staff to reduce the reliance on specialist vendors, to cut outsourcing costs. There are also attempts to standardise processes and documentation to reduce non-productive time on preparatory activities such as planning meetings and work permits.
Technology has a role to play, too. The industry is making better use of advances in sensor systems, allowing more accurate realtime monitoring of assets, which feeds into preventative maintenance. Big data is also a hot topic, with operators making efforts to better understand the condition of assets. And drones are being used for remote aerial inspection of assets, work that previously would have required costly helicopters and manned rope access.
Borwell says: “Given the maturity of the industry, most of the technology gains have already been made and we have always been early adopters of innovative technology and work methods. As assets get older and production declines, the economic driver for adopting costly new technology becomes a business challenge.
“That said, the industry does remain open to considering new technology that might improve efficiency. A good example might be around the internal inspection of process vessels – which has always proven to be time-consuming and costly. Much time and effort is associated with cleaning a vessel to make it safe for people to enter and work in. New methods of cleaning and gas-freeing are now available that reduce preparation for entry time from three days to less than 24 hours. That gain has a massive effect on the time taken to complete the internal work scope and to return the vessel to service.”
It’s clear, then, that the North Sea sector has a difficult balancing act to perform during a period of unprecedented cost pressures. Staying true to a long-term strategy, with effective safety standards at its heart, while still making necessary short-term cost cuts to ensure profitability is going to require careful implementation.
“The industry needs to maintain a medium-term outlook, whilst not taking its eyes off the short-term position,” concludes Graham Bennett, vice-president at DNV GL. “The industry is correct in focusing on cost saving at the moment, but it also needs to think about how to be sustainable and resilient beyond the two-year horizon.
“We need to be in a situation where we are replacing reserves, and looking at future challenges so that we don’t keep going through boom-and-bust cycles.”
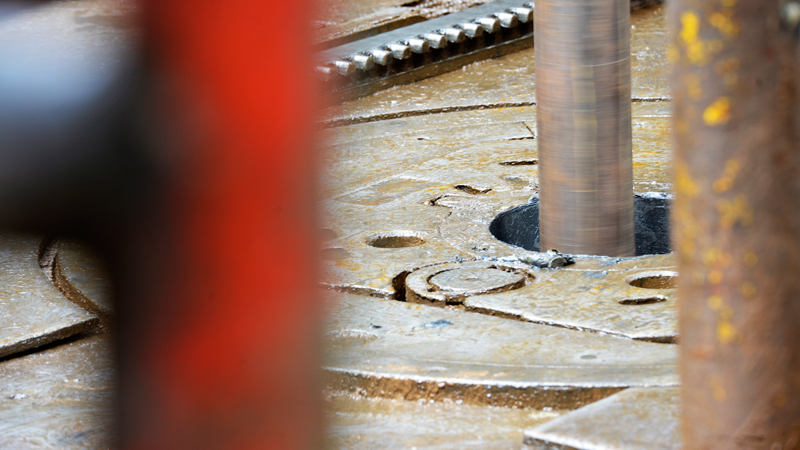
Struggling to contain costs in the oil and gas sector
Most senior oil and gas professionals believe that the industry is repeating the mistakes of previous downturns and have concerns over the loss of jobs and experience and lack of efficiency, according to a report published by DNV GL. A new phase of cost management is needed, as 73% of senior oil and gas professionals globally are preparing their companies for a sustained period of low oil prices.
According to A New Reality: The Outlook for the Oil and Gas Industry in 2016, a report based on a global survey of 921 senior sector players, cost management is the top priority for 41% of respondents. The top three measures prioritised to impose stricter cost controls are: tougher decisions on capital expenditure, down from 44% in 2015 to 31% in 2016, suggesting that opportunities for further capex reductions are limited; prioritising job losses, up from 25% last year to 31% in 2016, signalling further job cuts; and increasing pressure on the supply chain, down from 31% in 2015 to 27% in 2016, indicating that suppliers have been squeezed as much as possible.
Elisabeth Tørstad, chief executive of DNV GL – Oil & Gas, says: “With the low oil price, the industry has taken painful short-term cost-cutting measures by reducing the capex and headcount and squeezing the supply chain. Although 74% say they achieved their cost-efficiency targets last year and 65% believe the industry will be successful in cutting costs in 2016, not all parts of the sector have achieved lasting lower cost levels during downturns.
“To prevent repeating past mistakes, real change is needed now – cutting complexity, increasing collaboration and driving standardisation. These measures will enable the industry to adjust to the new reality and put it on a sustainable growth path for the long term.”
There are some promising signs that the industry is adopting longer-term thinking on cost management: 61% of respondents agree that operators will increasingly push to standardise their delivery globally, up from 55% in 2015 and 52% in 2014. Even in the current price environment, 49% say their company is taking a long-term approach to innovation and R&D. However, nearly one in five companies (18%) do not have a strategy in place to maintain innovation.
The most common strategy for maintaining innovation with lower budgets is to increase collaboration with other industry players (45%). One in three companies plan greater involvement in joint industry projects in the year ahead.
“Innovation and collaboration are even more important in this current price environment,” says Tørstad. “It isn’t just about finding the breakthrough technologies – although that’s important too – it’s also about making things simpler and more efficient and ultimately helping the industry to safely cut costs.”