Last month James Cameron became the third man to reach the ocean’s deepest point, dubbed Challenger Deep, at the bottom of the Mariana Trench near Guam. It’s an 11km journey that no one has taken for more than 50 years and it’s a place that scientists know very little about.
The journey was made possible by engineer Ron Allum, who designed the Deepsea Challenger submersible capable of taking Cameron down to depths where the pressure is 1,000 times higher than standard atmospheric pressure.
A broadcast engineer by background, Allum has worked with Cameron on his subsea projects for many years. In 2005 he orchestrated a live telecast from the wreck of the Titanic by fitting a Russian Mir submersible with a fibre-optic system. Later that year, he began work on the Deepsea Challenger.
Allum explains: “The main difficulty is that the pressure is absolutely immense, it’s really beyond the scope of normal engineering. The forces on the pressure hull are just incredible.”
The high pressure changes the size of everything from the bolts to the plastics, and this has to be allowed for in the design.
A 12m-long sphere forms the steel pressure hull. “It was quite a challenge to create the sphere,” says Allum. The submersible is designed to start its dive loaded up with enough weight to pull it down to the seabed. On nearing the bottom the thrusters kick in to slow down the vehicle. Once at the bottom, a trim weight is dropped to adjust the buoyancy to neutral.
The secret to the success of this lies in a special syntactic foam that Allum designed and manufactured to offset the weight of the heavy steel. The foam, which is made up of hollow glass microspheres bonded together with an epoxy resin, gains buoyancy as it descends, allowing the vehicle to stabilise at depth. This meant Cameron could stay at the bottom of the trench without sinking further or floating off. To get back to the surface, an ascent weight is dropped to lighten the vehicle and send it soaring up.
Before Cameron’s dive, Allum and his team tested most of the submersible’s parts individually in pressure chambers. One challenge was integrating an acrylic port into the design. During testing, stress cracks appeared in the port, leading to a redesign. Data collected during the tests was plugged into a finite element analysis program to inform the alterations.
Allum says: “It was quite a calculation to work out the changes in buoyancy, pressure, depth and salinity, and anticipate what would happen.” As there is no facility large enough to test the whole set-up, the final step was an unmanned dive to the bottom of the Mariana Trench. He says: “We literally had an egg timer on it.” The timer was set so that once the vehicle got to the bottom it sat there for an hour before dropping its weight to return to the surface.
With all tests complete, Allum had no qualms about sending Cameron down to the bottom of the ocean. Allum says: “I was very confident in the submersible, I knew the pressure hull was well engineered, we had tested pretty much every piece of foam and the bonding technique for the composites.”
Cameron spent three hours at the bottom of the trench collecting samples for research, and won the accolade of having made the first solo dive to the Challenger Deep.
California-based Hawkes Ocean Technologies was also once in the race to get to the bottom of the ocean. Chief mechanical engineer Adam Wright says the company’s approach to the design of a submersible capable of reaching the Mariana Trench was different to that taken by Cameron’s team.
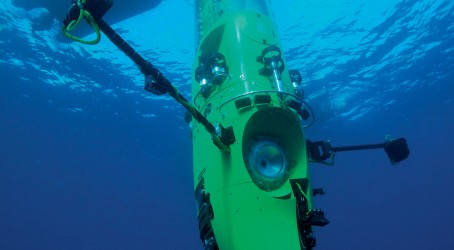
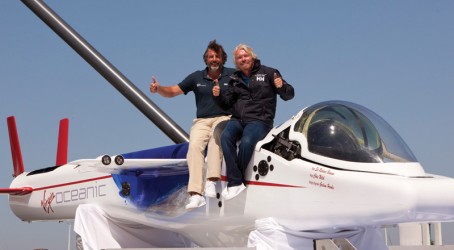
In the Hawkes submersible, called DeepFlight Challenger, the pressure hull is made of carbon fibre. It has a quartz hemisphere at one end and an aluminium hemisphere at the other with titanium interfaces between the materials. The Hawkes submersible is almost a third of the weight of Cameron’s vehicle and it operates on the principles of flight.
Like Cameron’s sub, DeepFlight Challenger gets to the bottom using a weight drop system and is neutrally buoyant at depth. But its cylindrical design and large-diameter propeller enable it to move around freely in any direction on the bottom, driven by electric thrusters using relatively little energy.
Research and development of the submersible was funded by millionaire adventurer Steve Fossett. Fossett held many world records, including being the first person to fly solo non-stop around the world in a hot-air ballon, and he had his eyes set on travelling to the bottom of the Mariana Trench.
But when Fossett went missing after his plane crashed in 2007, the project stalled. In 2008 he was found dead in the Sierra Nevada mountains. With its source of funding lost, the DeepFlight Challenger lay untouched in a San Francisco Bay workshop. The reins of the project were eventually picked up several years later by entrepreneur Chris Welsh but by then the plan had lost its magic.
“Personally I had already resigned the project when Steve went missing,” says Wright. “Everyone knew Cameron was building a vehicle. We didn’t know when it was going to happen.”
In the meantime Hawkes went on to develop a series of deep-water submersibles, including vessels for Virgin Oceanic owned by Sir Richard Branson. Now Hawkes has turned its attention to the remotely operated vehicle market. Wright says: “Cameras and remote technologies are so advanced now that there is no reason to put a man or a woman in the path of danger.”
He believes that the team’s latest creation, developed in partnership with Massachusetts firm Bluefin Robotics, will change the market for remotely operated subsea vehicles. The submersible is powered by batteries. This enables it to travel deeper than vehicles that do not contain batteries because it does not need a thick cable to supply it with power from the surface. The deeper a submersible travels, the thicker the cable needs to be to accommodate the voltage loss that occurs over the long cable length.
The new concept uses just a fibre-optic cable to carry the signal that tells the submersible what to do. As this cable is much thinner than a power cable, it can be spooled into the vehicle, which eliminates the need for a large ship to support the submersible.
Wright says: “We’ve reduced the cost of operating these things by a factor of 10.”
The vehicle can be kitted out with components such as mechanical arms, probes or cutters. The main buyers will be oil and gas exploration companies, but a significant military market also exists for harbour descents and mine countermeasures.
Engineers at DOER Marine in California tell a similar tale to Wright about their quest to reach the bottom of the ocean. The company also has designs and concepts for a submersible capable of reaching the Mariana Trench that are lying idle. Director of engineering Tony Lawson says: “As technology floats across our desk we put it in a file with the hope that it will gain interest.”
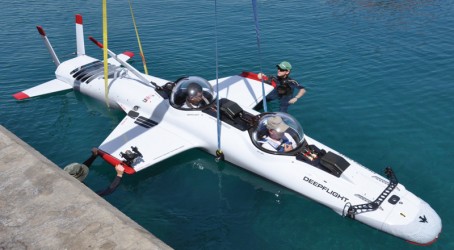
DOER’s project was not about one man’s quest to race to the bottom of the trench, but to replace a 50-year-old submersible called Alvin used by scientific researchers. The Deepsearch project got to the scale testing stage before funding was pulled by the Marine Science and Technology Foundation, whose president is Eric Schmidt, the former chief executive of Google.
Measuring just over 12m long, the Deepsearch sub would carry a pilot and two scientists. The aim from the outset was to use cutting-edge technology to get the submersible to the seabed as fast as possible so the researchers could spend most of their time there.
Instead of using the drop weight method to get down, Deepsearch would travel under its own propulsion using lightweight high-efficiency motors powered by a bank of lithium-ion batteries. This would enable scientists to stop at any point to make observations.
The vehicle comprises an aluminium frame and a glass sphere. Although glass is weak in tension, its amorphous structure makes it incredibly strong in compression. “The neat thing about a sphere underwater is that it is under hydrostatic pressure – an even pressure all around that puts everything under compression, so it is ideal for glass,” says Lawson.
Using glass does pose some problems, such as where to put the hatches, and how to stop them from creating a tensile load in the material. But Lawson believes he has some theories that could solve those problems.
Deepsearch would be floated using modern syntactic foam or a matrix of fist-size ceramic spheres filled with air. But the decision on the use of flotation materials was never made as the project lost its funding in 2009.
In the meantime the DOER team has got on with other projects, building subsea robotics and manned submersibles.
In fact the company developed the manipulator arm that went down to the Challenger Deep with Cameron. The implement is a customised version of the company’s Sea Mantis arm. DOER’s latest build is a 6,000m-rated manned submersible.
Lawson says: “Commercially, these things are out there everyday working and most people don’t even realise. The Deepwater Horizon oil spill was one of the first times that people really saw these subsea robots working hard at a very difficult place. Capping that well at depth was the engineering feat of the decade.”
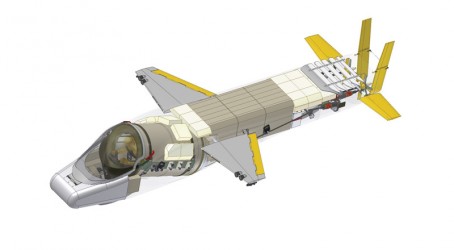
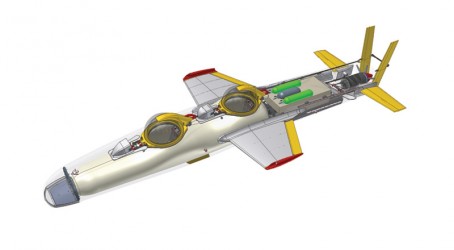