In an underground laboratory in central Sydney, the robot and drone are being put through their paces. From time to time, the engineers hunch over their respective offspring, fine-tuning movements and adjusting software.
Croc, an autonomous robot inspired by the movement of an inchworm, is edging its way along a customised tunnel in the corner. With its magnetic feet, Croc can climb vertical steel walls, avoid obstacles and pivot through small spaces inside steel structures. Meanwhile an autonomous drone, which navigates using its own camera instead of GPS, inspects the outside.
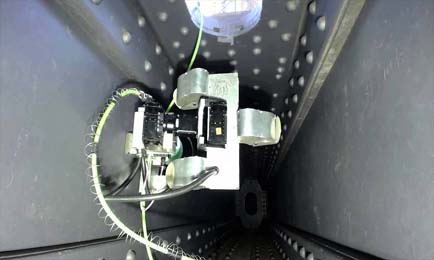
Drone on the inside
The researchers believe Croc could be used to inspect structures such as bridges, ship hulls, transmission towers and oil rigs, recording inspection data and comparing it with data from previous visits as it moves.
Croc sees and thinks for itself, answering questions such as “Where am I?”, “Where do I want to go now?”, “How do I get there?”, “What do I want to do now?” and “How do I do that?”
Croc has been developed over five years by a team of nine engineers at the University of Technology Sydney, which claims the robot is the world’s first autonomous climbing robot for steel bridge inspection.
Peter Ward, team leader for the Croc's hardware and testing side, has had a passion for robots since he was a kid growing up in Perth. Ward says other researchers internationally are developing inspection robots, and some are in commercial use. But “those robots have limited intelligence and face difficulties overcoming challenging obstacles”.
Croc is a different beast. Ward says: “First, it needs sight and an idea of how far away objects are. Once it has explored its environment and constructed a map, it figures out where to go next and how it’s going to get there, all the while making sure it won’t collide with anything.”
Ward says the research has focussed on developing algorithms to perform Croc's “exploration, mapping, localisation, planning and collision avoidance” functions.
Associate Professor Jaime Valls Miro says that Croc is set apart by the level of industry involvement in the project, with the Australian Research Council project receiving funding and support from Roads and Maritime Services.
He says: “Many other similar projects are just confined to a lab whereas Croc is a deployable solution to a real-world problem.”
“It is an industry-driven project that is actually achieving something from the data it collects, including high-definition photos of the current status of the Sydney Harbour Bridge.”
Drone on the outside
On the other side of the basement lab, researcher Dr Dinuka Abeywardena is calibrating a tiny camera as part of his project to develop an intelligent drone. Most drones rely on GPS for navigation, Dr Abeywardena says, but those signals can be disrupted, especially in urban or indoor environments, reducing the drone’s effectiveness.
“What we are doing differently is improving the perception capabilities of the drone,” he says. “We’re using a camera as its eye, so that it can explore its environment and collect data around it.
“The images from the camera get processed by an on-board computer, to estimate how it moves and flies, its speed and tilt and the direction of the wind.”
Dr Abeywardena’s team is seeking industry partners to help field-test the drones and navigational algorithms that have been successfully tested in the lab.
“Our drone eventually could be used inside a warehouse, working closely and safely with human employees,” he says. “It could also be used outside, measuring wind speed and monitoring the effectiveness of wind turbines, for example.”
While Croc inspects the inside of bridges, the drone could inspect the outside. It could also monitor tree growth along power lines and conduct bushfire inspections, saving time and money for companies that now use manned helicopters.
Original article via
University of Technology Sydney. Photo: Andrew To