The drone swoops down towards our position from an altitude of 100ft, buzzing angrily. “It’s like a swarm of bees, isn’t it?” says Malcolm Connolly.
Descending further, the tiny aircraft looms larger in view as we are assaulted by legions of midges with a quieter – but highly irritating – agenda of their own.
Mid-June amid the stunning scenery of the Highlands of Scotland, and we are blessed with clement weather, allowing Connolly and his team to demonstrate what unmanned aerial vehicles (UAVs) have to offer for the inspection of oil and gas and electricity infrastructure.
The prevalence of such drones in the military sphere is well-known: for the first time air forces in the West are training more UAV pilots than conventional ones. But others are looking at how this rapidly developing technology can be used in civilian roles, and it’s here that Connolly’s firm Cyberhawk is establishing a niche.
“I don’t think we’ll have manned aircraft in a generation,” says Connolly, a chemical engineer by background who after university specialised in industrial rope access – getting to hard-to-reach locations to carry out inspections or maintenance of plant. Realising the potential of UAV technology to perform this type of work, he set up Cyberhawk six years ago.
He has since gone on to develop a client base that includes Shell, Exxon Mobil and several other big oil and gas companies, which are using the aerial robots to inspect flare stacks at refineries and offshore installations, scaling heights that are difficult or dangerous for people to attain. Utilities such as Scottish and Southern Energy are also interested in the technology’s ability to survey electricity infrastructure such as pylons.
The next development will be to use UAVs for blade inspection of offshore wind turbines. “The maintenance issues there haven’t been fully encountered yet,” says Connolly. The technology could be used to identify discontinuities in the blade surface such as bulging or cracking, where very fine details need to be inspected. “It’s not clear how effective it would be to use abseiling teams or cranes for this work,” says Connolly.
In the oil and gas industry, it is typically necessary to shut down a flare for the
purposes of inspection. However, Cyberhawk’s technology allows for the live remote inspection of flares. The aim is to identify any problems before the shutdown takes place so that maintenance is more efficient and potentially can be carried out more quickly, which can mean substantial savings.
Offshore, inspection work sometimes has to be carried out by a team in a helicopter with a camera. Such operations are expensive, says Connolly, and the UAV has the potential to be more reliable. And he argues that using UAVs rather than helicopters for inspection purposes is a much safer solution.
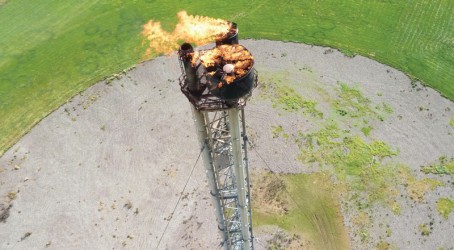
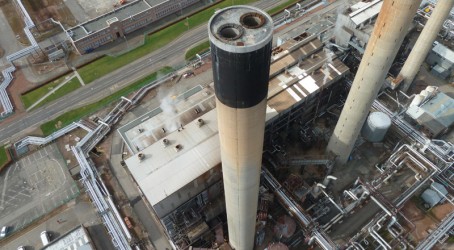
It can take a year to a year-and-a-half to train a pilot to fly one of Cyberhawk’s UAVs, and the most demanding application is flying it offshore. The company has brought in an ex-RAF commander to train Cyberhawk engineers.
The small aircraft can fly with a high degree of autonomy and can follow preprogrammed flight paths, with manual control when necessary.
We watched a drone inspecting an electricity pylon, hovering to take hundreds of pictures through a high-definition digital camera and video that is decoupled from the aircraft, allowing it to focus independently of the UAV’s movement.
The drone has eight rotors, driven by highly reliable brushless motors. It has a lightweight, 2kg carbon-fibre structure, with the fuselage arranged in a transverse shape to ensure that the camera can operate. The machine can fly in winds of up to 20 knots, and can operate even if two rotors fail. The reliability of the motors is such that one failure might be anticipated every 150,000 hours.
The technology is imported from Germany to specific requirements. Connolly says: “Although the base platform of the hovering UAV we use has come from Germany, we have had to spend significant time and money ourselves on front-end development of the off-the-shelf system to overcome key technical challenges, such as it being flown close to objects and in areas of high magnetic field – next to power lines or metallic structures like flares. This is the key reason that we have not had any credible competition appearing.”
The maximum allowable altitude for the UAV is 120m. To fly higher, special dispensation is required from the Civil Aviation Authority. Pylons for inspection are chosen from a map. They are sometimes damaged by lightning strikes and the aim is to identify wear to components such as conductors and insulators. Some are at more risk than others, for example because of exposure to prevailing winds.
Normally, if carried out by a person, pylon inspection requires a shutdown. “With our system, there’s no need for a circuit outage. We can inspect 10 towers a day, and there’s no one climbing up the structure,” says Connolly.
The future looks bright for the business, with staff numbers expected to double in the coming year. There is plenty of infrastructure out there that could perhaps benefit from the approach – not just onshore and offshore flares but also chimneys, vent stacks and other high structures. Another area where the technology could be used is profiling gas clouds as they leave flues or chimneys – for pollution control, for example.
Connolly is confident that Cyberhawk will play a leading role in the development of UAV technology for inspection and maintenance roles. “We’ve only just scratched the surface of what systems such as these are capable of achieving,” he says.