There’s a strong sense that the modern automobile stands at a crossroads in its development. For decades we’ve had the internal combustion engine, and a multitude of incremental advances that have been made with that technology. But now there’s a new contender – the electric vehicle. And the next couple of years will define whether this radically alternative approach will have mass-market appeal.
Nowhere can this transition be more clearly seen than at the gigantic Nissan car factory in Sunderland. Here more than £420 million is being spent to prepare the plant for the manufacture of the Nissan Leaf electric vehicle and to build a new plant to make 60,000 lithium-ion battery packs per year.
That sort of investment provides a clear indicator of expectations for the global electric market: it’s highly unlikely that a shrewd operator like Nissan would spend such an amount if it wasn’t certain that the market was there to pay for an acceptable return.
The battery plant will go into operation by 2012, and the new Leaf will start rolling off production lines in 2013. Those upcoming milestones make Sunderland a hive of excitement and anticipation, with dedicated teams of engineers already committed to both projects. The preparation work is being supported by Richard Ebrahim, director of engineering at Nissan Motor Manufacturing (UK). And he’s keenly aware that it represents a momentous opportunity.
“We are at a historical stage in the automotive industry,” says Ebrahim. “When we talk to our grandchildren in years to come we will be able to say that we were part of the first mass-market electric vehicle manufacturing project.
“The main attraction, as an engineer, is that it is all so new – electric vehicles are very much in the development stage and we are actually playing a part in that transition. It’s a technology that will change the way we work and live. It’s a huge motivational feeling being part of such a big change.”
Ebrahim says that, technically, the project gives him and his team the chance to break new boundaries. The challenges are immense: Nissan will be manufacturing an all-new product platform with an entirely new powertrain technology, and one that has never been put into truly high-volume production before. There are also concerns about scaling up the Leaf’s lithium-ion battery pack so that it emerges from the new plant in shape to meet the demands of excited customers. But those are exactly the sort of challenges that enticed Ebrahim in the first place.
“On an internal combustion plant project you might get to squeeze out another 1 brake horse here or there, or you might get to develop a V8 or a V12 so that it gets to be a little bit faster, but you won’t be changing anything radically. However, electric vehicles are different as they are still in their infancy – so we get to be at the cutting edge of change. We all feel part of the transition, and that’s really exciting.”
The Leaf itself is a five-seater, C-segment hatchback, powered by an 80kW electric motor. The lithium-ion battery pack contains 48 modules with a capacity of 24kWh and a maximum power of 90kW. The batteries will give the car a real world range of 110 miles (NEDC mode) and a top speed of more than 145km/h. The car will be built on an all-new dedicated electric vehicle platform, with the batteries located in the wheelbase to give it a low centre of gravity.
Construction of the plant that will supply the batteries is already well under way. The shell of the 25,000m2 facility is erected and fitting-out of the interior systems will take place over the next couple of months. The factory is based on a horseshoe-shaped layout comprising clean room, ageing process and assembly. The cell-to-module-to-battery-pack journey will take around 30 days, after which the finished product will be transported to the assembly facility.
Nissan’s engineers in Japan have spent many months refining the battery manufacturing process, working out how to optimise battery performance while minimising lead time. The ageing process is arguably the most critical part of the transformation. The battery cells progress through giant ovens and have to endure exact temperatures for specific periods to allow chemical reactions to take place.
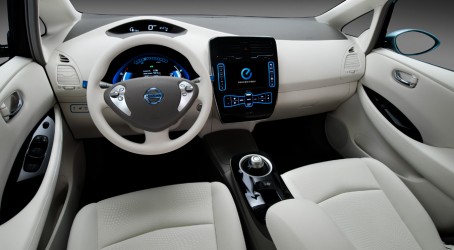
“The battery plant has gone up at real speed and will be on time and on budget,” says Ebrahim.
“It has been a real learning process, because what we are doing is taking what not too long ago was a laboratory-based technology and transforming it into a mass-production process. We will soon have a capacity of 60,000 units a year, creating 200 jobs and another 600 in the supply chain. It’s quite a project.”
Work to integrate the Leaf into Sunderland’s manufacturing process will begin in 2013. The car will be made on the plant’s No 2 production line alongside the Juke compact crossover, which entered production last year.
That integration process is being overseen by Ian Ferrier, manager of trim and chassis within Nissan Europe Production Engineering. The main challenge, he says, is safely inserting the battery pack into the car – it’s quite a different proposition from handling an internal combustion engine.
“The battery is a significant energy source so we have to be very careful during this process,” says Ferrier. “We have got a series of control sheets which set out the process to be followed. It’s a structured system with facilities and training designed to ensure that the control documents are followed.”
Ferrier says that Nissan has a manufacturing philosophy that mitigates risk and that the handling of high-voltage electrical components will be covered by that method of doing things. “People are sometimes a little bit nervous about the safety of batteries but if we were introducing the internal combustion engine for the first time we would be talking about a flammable fuel. This is simply a different energy source,” he says.
The modifications to the assembly plant are currently being made, with funding being allocated to several different projects. Ferrier says that by the middle of the year Nissan will have completed that process and will then embark fully on purchase and preparation of the production line. He says that everything is going to plan and the plant will be ready on time.
“It’s a great project to be involved with,” he says. “It’s certainly been a rapid increase in our knowledge base.”
Assembly of the Leaf will begin at Sunderland in 2013 with an initial annual production capacity of 50,000. The car is already in production in Japan and has already won accolades, being named last December as the 2011 European Car of the Year, the first electric car to take the award. The driver experience is impressive with the three-phase AC permanent magnet-type synchronous motor giving an entirely new sense of acceleration. In contrast to a conventional car, in which output increases along with the number of engine revolutions, the Leaf motor can go from zero to maximum torque of 280Nm the second the driver hits the accelerator. In addition, because there is no shift involved, the ride is remarkably smooth and quiet.
Ebrahim says that the reception of the Leaf has been gratifying, especially as it is essentially a proof-of-concept car. “It is proof that electric vehicles can be marketed and can be successful,” he says. “The end product is excellent. The European Car of the Year award isn’t given for electric vehicles – it’s a car award. To win it with an electric vehicle would have been unthinkable even a couple of years ago.”
So it’s evidently all systems go for electric vehicles at the Nissan plant in Sunderland. The only slight area of concern on the project, says Ebrahim, is that the company is struggling to attract enough engineers with the right kind of skills. He says: “We need skilled engineers; we need people who are capable of helping us deliver the project. And we need a lot of them.
“That’s one of the biggest constraints on the Leaf project. We need good engineers coming in and it has been hard to attract them – there is a real shortage. We are struggling to attract the numbers of people and quality that we need.”
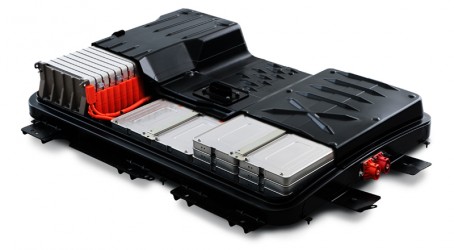
Technical briefing
Lithium-ion battery system
The lithium-ion battery is the core technology, with an enormous influence on the performance of the Leaf. Nissan says that, compared to conventional batteries, the Leaf’s lithium-ion battery is more compact and lightweight, and has about twice the energy density. The battery has a capacity of 24kWh, maximum power output of 90kW, and a total voltage of 360V. The battery is expected to maintain about 80% capacity for more than five years. The battery comprises manganese positive electrode material. Manganese is an abundant resource, and its spinel crystal structure is stable. The laminated cell structure has excellent cooling efficiency and a simple configuration, which makes it possible to develop long-life cost-efficient batteries.
Motor
The Leaf features a three-phase AC permanent magnet-type synchronous motor. The high-output and high-efficiency motor reduces energy loss from its copper wiring with an optimised magnetic circuit and high winding density. During deceleration, some of the deceleration energy is converted to electricity as a power generator. The motor has maximum torque of 280Nm, maximum power output of 80kW and maximum speed of 10,390rpm.
Inverter
The inverter converts DC to AC and controls the motor’s power output by controlling the amount of current. It uses specially designed components, including an original power module that mounts semiconductors directly onto wiring boards, eliminating the use of costly PCBs.
DC/DC converter
Apart from the lithium-ion battery used for powering the car, a separate battery is included for electrical components such as the audio system, navigation system, and headlights, which operate on a 12V power supply. This battery can be charged by stepping down the 360V power of the lithium-ion battery to 12V using a DC/DC converter.
Handling
Nissan says its engineers have paid particularly close attention to the ride quality offered by the lithium-ion battery and AC synchronous motor control technologies. Handling performance has also been considered. The Leaf offers a low centre of gravity and good front-back weight balance by placing the battery in an optimal position in the wheelbase. Because the Leaf runs on a silent motor, the sound of tyres and the wind is more pronounced than with internal combustion engine vehicles. Nissan’s engineers solved this by controlling air flow to make the car quieter. To minimise wind sound, which comes primarily from the door mirror area, they adjusted the shape of the headlights. Because long, large headlights are positioned higher than the bonnet, the wind flow generated by the lights does not hit the mirrors. This reduces wind noise and friction.
Charging
Rapid charge can be achieved to 80% capacity from battery level warning light in less than 30 minutes, while normal charge to full capacity can be achieved in 8 hours. The Leaf has a range of 110 miles on a full charge under NEDC mode. However the range of electric vehicles can be more heavily impacted by driving conditions than a petrol-powered car would be. Nissan says that factors such as continuous high-speed operation and road gradient will affect range, which may drop to about half if driving conditions are especially severe.
Range
Range anxiety is a concern, and Nissan has made efforts to alleviate this through the development of an IT system that displays remaining battery charge and the location of charging stations. The system also enables the driver to operate heating and air conditioning in the vehicle from a smartphone and can be programmed to send email alerts on remaining charge.
A team effort
The Leaf project is a real team affair at Sunderland, with dozens of engineers already involved. PE spoke to a selection of those at the forefront of the electric dream
Richard Ebrahim
Richard Ebrahim began his career in 1977 as an apprentice at Avery Dennison in Cramlington, Northumberland, where he rose in the ranks to become a project engineer in 1986.
He joined Nissan Motor Manufacturing (UK) in June 1989 as an engineer responsible for bodyshop facility specification and procurement. In October 1995 he was promoted to senior engineer responsible for new model body process specifications, plus body-in-white quality improvements. In November 2004 he was promoted to manager in charge of new model body process and facilities.
Ebrahim was appointed as engineering director at the plant in April 2007 where he has overall responsibility for all Nissan UK engineering functions which also incorporate the plant’s environmental department and maintenance department.
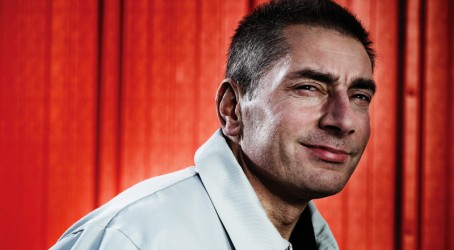
Jeff Pratt, engineering manager, battery plant
“When Nissan decided to go into electric vehicles, it was a brave move. The technology advances with batteries are still developing. We are now going into mass production while the technology is developing at the same time, and we are going from small ovens to a massive industrial ageing process. It’s a difficult and challenging job to satisfy what’s required in terms of getting the process right.”
Carly de Silva, engineer, battery plant
“The level of confidence with electric vehicles is steadily growing. Leaf has been featured on North News and I’ve put comments on Facebook telling people to take a look at it, because I am really proud to be involved. In general discussion with people I can see that people are getting more interested in this technology.
Normally when I get into conversation with people and talk about my job, if they aren’t interested in cars you lose them. But even people who aren’t into cars are interested in electric vehicles because of the environment factor.”
Rob West, engineer, battery plant
“We’ve got a group of people here who 18 months ago were all working in different areas and all came from different backgrounds. Now we have come together to form the battery group and we are working on a project that is at the forefront of what Nissan is doing for the future. None of us expected that. It’s all moved on tremendously quickly. But this is us now and this is what we are doing. There is a sense of privilege working on this project. Most other engineers at Nissan are envious that we are working on this project.”
Chris Miller, senior maintenance supervisor, battery plant
“It’s innovative, it’s exciting, and there are a lot of wonderful technologies involved. We are all enjoying it. It’s stretching us but it’s very exciting. I went on a one-week visit to Nissan in Japan last year and by the second day I knew I wanted to be involved in this. Yes, I knew it was going to be very hard but it’s a fantastic opportunity. I’m learning new skills.”
