Articles
A British company has used an unmanned aerial vehicle to inspect a flare stack at an oil and gas refinery in Scotland without shutting down the plant – a world first. The vehicle, loaded with high-definition video and still cameras, flew within metres of the tip of the 100m structure.
The drone was operated remotely from the ground and made technical inspection of the flare stack cheaper, safer and quicker, according to the company behind it, Cyberhawk Innovations.
It replaced the need for cranes, scaffolding or helicopters that would have been traditionally used to get workers close enough to the flare tips to scrutinise them. Although hiring such equipment can be expensive, the highest costs for refinery operators come from the need to shut down the plant.
The constant flames emitted from a live stack make it too dangerous for workers to get close to the equipment. Malcolm Connolly, co-founder and technical director of Cyberhawk Innovations, said: “It’s not safe to fly a helicopter over the big onshore refineries like Grangemouth because the consequences of it going down are horrific.”
If a fault is spotted during a normal flare stack inspection it can take up to six weeks to get hold of spare parts – often longer than the plant is switched off during a planned shutdown. This means refinery bosses can be faced with the decision to restart the plant knowing that the flare system is not up to scratch. “They are probably going to have to do an unplanned shutdown at a later stage to replace the flare-tip part. That can cost upwards of millions of pounds a day,” said Connolly.
So live inspections can make planned shutdowns run smoother, he explained. The fact that nobody has to work at height makes inspections safer too. Falling from height is one of the main causes of fatal injury in the workplace. At least 35 people died and 4,600 were injured in such accidents in the UK in 2008-09.
Using a flying device can bring an extra dimension to the images available for assessment. The drone’s cameras can provide close-up detailed photos of the stack’s components as well as others that give an overview of the tip from further away. But, unlike a person, the drone cannot do any physical work as yet. Connolly can see this happening in the future: “The vision of where this technology is going would parallel that of the underwater remotely operated vehicle industry.”
He went on: “At first these submerged vehicles were developed to do inspections. But as technology has moved on, they can now use manipulative and robotic arms to do work underwater.”
Cyberhawk’s flying vehicle is a multi-rotor device that runs on batteries. “It has got eight rotors and keeps its position by speeding up and slowing down each of the motors rather than changing the pitch of the rotor blade like a conventional helicopter. So from a mechanical point of view there are very few failure points,” said Connolly.
Cyberhawk has inspected most of the onshore oil and gas installations in Scotland and is now looking to get the technology used offshore too. The company will soon start using drones to inspect power lines for Scottish and Southern Energy.
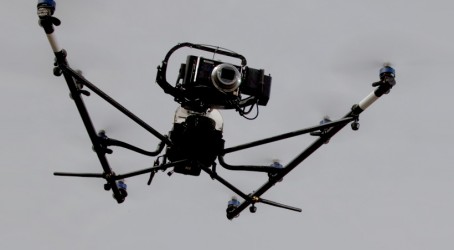