Fast acting: GKN’s all-wheel drive system in the Range Rover Evoque includes disconnect technology
The popularity of all-wheel drive on SUV platforms hasn’t gone unnoticed. Slowly but surely, the technology has started to migrate to B- and C-segment vehicles, as customers demand better grip and performance in both on- and off-road conditions.
But all-wheel drive comes with a trade-off. It adds weight and complexity to a vehicle, with frictional losses resulting in lower fuel efficiency. So while all-wheel drive has had many converts in recent times, engineers are being challenged to deliver constant refinement.
There is certainly a big prize at stake, though. A recent report from industrial assessment specialist Research and Markets suggests that demand for all-wheel drive is surging, driven by the popularity of the technology on traditional SUVs, but also on emerging platforms such as hybrids. The report suggests that several key tier-one suppliers – including BorgWarner, GKN Driveline, Magna and ZF Friedrichshafen – are jostling for position in the lucrative market sector.
That is certainly true at GKN Driveline, which has invested heavily in the development of more fuel-efficient all-wheel drive systems and has scored some notable successes with OEMs such as Jaguar Land Rover and Fiat. “There has already been a major shift in the market and the public’s perception of the technology,” says Rob Rickell, president of group technology at GKN. “Traditionally many all-wheel drive systems were based on rear-wheel drive truck platforms, and converted to four-wheel drive. They were quite heavy and quite robust. What has been happening over the past few years is a trend towards developing all-wheel drive on lighter passenger cars, often on front-wheel drive-based platforms.
“And in the past couple of years technology developments have given the ability to disconnect the all-wheel drive system automatically, so that the driver only notices the benefit of the technology when needed. This brings the advantage of much better fuel consumption.”
A good example of this was GKN’s development of an all-wheel drive system that was integrated into the Range Rover Evoque. This included a ‘disconnect’ technology, which reacts to the driving environment by automatically disconnecting the major rotating driveline components to reduce losses. Traction and driving stability were optimised by the active torque-biasing feature offering advanced control on the distribution of the torque between the front and rear wheels.The system included a power transfer unit (PTU), linked to the transmission’s final drive differential, containing a synchroniser and brake to disconnect the all-wheel drive system upstream of the PTU hypoid gears. At the rear of the system a rear drive module drives each rear wheel via an independent wet multi-plate clutch. These clutches can disconnect the all-wheel drive system downstream of the rear drive module hypoid gears.
The PTU synchroniser and the rear drive module are controlled by a dedicated driveline control unit designed to constantly monitor vehicle dynamics, disconnecting during steady-state driving speeds above 22mph and automatically reconnecting (within 300 milliseconds) when required. The rear drive module also acts as an electronic differential combining drive vectoring and limited slip differential technology for active torque biasing.
The success of the Evoque project encouraged GKN to develop what it says is the world’s first disconnect all-wheel drive system for A-, B- and C-segment vehicle platforms. Again, the system responds to driver inputs and road conditions, connecting and disengaging drive to the rear axle on demand. By eliminating rotating losses from the driveline, during steady-state cruising fuel efficiency can be improved by up to 4% compared to permanent all-wheel drive systems.
GKN’s offering is a tightly packaged design, which replaces features such as the standard PTU with a monoblock housing that fully integrates the propshaft’s constant velocity joint. The arrangement also yields superior noise, vibration and harshness characteristics, benefiting the vehicle’s overall refinement.
“You will see quite a few more vehicles with all-wheel drive technology coming to market in the near future,” says Rickell. “And there is a definite migration from full-time all-wheel drive systems to on-demand technologies, as drag and friction losses on the latter are much better, improving fuel economy and reducing emissions. The disconnect and reconnection all happens within 300 milliseconds, without any noise, and without any vibration in the vehicle. It’s completely seamless,” he says.
Technology partners: GKN’s eAxle module
A natural extension of torque vectoring and disconnect systems is the development of hybrid all-wheel drive technologies. More recently, GKN has been working with car manufacturers on such vehicles using what it calls its eAxle technology. Most notably, German sports car maker Porsche recently awarded GKN coveted technology partner status for the successful completion of an eAxle for the 918 Spyder, an advanced plug-in hybrid supercar. GKN Driveline’s eAxle module supports full-electric mode, all-wheel drive, with a boost function.
The initial criteria for the 918 Spyder were challenging, admits Christian Hauck, Porsche powertrain manager. “We wanted to realise our vision for a super sports car capable of setting a record lap time of the Nürburgring and of achieving fuel efficiency of 3 litres/100km, and that placed huge demands on our engineers and all suppliers.”
The technology that supplements the 918 Spyder’s hybridised 4.6-litre V8 is an evolution of GKN’s eAxle drive. The module has maximum power of 95kW and can deliver up to 1,500Nm of torque to the front wheels via a fixed gear ratio. A special compact differential engages the torque, giving the car optimum power distribution at all times. The differential also disengages the module to minimise drag losses and maximise efficiency. At speeds above 265km/h (164mph), a clutch isolates the electric motor to prevent it from over-spinning.
A key target for the 918 Spyder was to have the lowest possible centre of gravity and ground clearance. To achieve this, GKN’s engineers opted to position the output overhead, using an innovative lubrication concept to manage the oil flow. The oil reservoir was positioned above, not below, the geartrain. Oil is gravity-fed down onto the bearings and gears until it reaches the high-speed input at the bottom where it is then circulated back to the oil reservoir at the top.
This design minimises the amount of oil on the input shaft, keeping churning losses to a minimum. To ensure the critical areas remain lubricated even in disconnect mode, the motor is driven for intermittent intervals to maintain a constant oil flow.
The Porsche 918 Spyder’s tight packaging also meant there was almost no air flow around the transmission and so water cooling was needed to manage the heat generated by the module’s high power density.
Technology partners: GKN’s eAxle module is fitted in the Porsche 918 Spyder
The Spyder project presented a unique set of challenges. And that, says Rickell, is par for the course when it comes to all-wheel drive technology. “There’s many different ways of achieving all-wheel drive. One size does not fit all. Each carmaker has different system performance specifications. We can use building blocks of technology that we like to have as standard on these systems, but how they come together to meet customer requirements is where the skill of a company like GKN Driveline lies.” That was certainly the case for two other projects – an all-wheel drive technology designed for the Chrysler Jeep Renegade and Fiat 500X. “These systems have the same mechanical components, but it was the software and the control algorithms that were different, giving the DNA that Jeep wanted for what was very much an off-road vehicle, while the 500X was more of a sporty, on-road car,” he says.
Going forward, GKN is planning continued refinement of its all-wheel drive technologies, specifically in terms of lightweighting and packaging. There are other challenges, too. Rickell says: “We are constantly working on the drag torque. When all-wheel drive systems are disconnected, there remains some residual drag, because some parts are still rotating. But we are now talking of drag torques of 1Nm in disconnected mode. That really is very little. But we are always looking at improving that. And we are also concentrating on the speed at which the system goes from a connected to a disconnected drag state. How quickly it transitions is a hugely important factor.”
Another area of improvement will be GKN Driveline’s greater integration on carmaker platforms. “Complete system development is important,” he says. “If we are doing all of the software, all of the actuators, all the mechanical parts, the driveshaft – if we had complete responsibility for that, as we have had on some of these recent vehicles, then we can optimise more than if we were just supplying some components.
“On the Fiat/Chrysler projects we fully integrated the constant velocity joint on the propshaft into the power transfer unit, which wouldn’t have been possible if we hadn’t had responsibility for the complete system. That enabled us to optimise efficiency and weight,” he says.
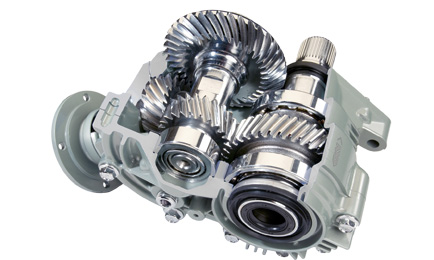
GKN’s principal all-wheel drive components
Power transfer unit (pictured below) –aluminium construction that gives full-time or on-demand all-wheel drive torque distribution for front wheel-drive based systems.
Propshafts – can incorporate Cardan joints, flexible couplings or a range of high-speed constant velocity joints, connected by steel, aluminium or composite tubes. One-, two- and three-piece designs are available with various options for intermediate bearings, slip devices, crash optimisation, vibration damping and plunge capacity.
AWD couplings – control the transfer of torque to the secondary axle in an on-demand all-wheel drive system. They are equally functional acting across a centre differential in a full-time AWD system to tune the behaviour of the base mechanical system. Viscous couplings are purely mechanical and respond tuneably to the speed difference across them. Active couplings receive information about vehicle behaviour and environment to direct torque in the driveline, achieving the goals of the vehicle manufacturer. Geared centre differentials, including the innovative DualDiff, provide a differentiated alternative to on-demand all-wheel drive.
Final drive unit – aluminium or cast-iron construction, final drive units are supplied for front and rear independent axle applications. Differential options include open, limited-slip, locking and active differentials.
Disconnects – manufacturers are increasingly seeking ways to disconnect the all-wheel drive components when not required to reduce emissions and improve fuel economy. Disconnects act as torque management devices, providing an opportunity to adapt existing solutions to meet this emerging requirement. By combining products such as ‘free running differential’ and ‘electronic torque manager’, all-wheel drive systems can now be offered with negligible disconnected drag and seamless reconnection in a fraction of a second.
First BMW front-wheel drive car uses all-wheel drive technology
US-based automotive components maker BorgWarner has also emerged as a prominent supplier of all-wheel drive technology, most recently supplying its GenV coupling for BMW’s new 2 Series Active Tourer.
The electro-hydraulically actuated all-wheel drive coupling automatically distributes power between the front and rear wheels of BMW’s first-ever front-wheel drive vehicle. In addition to optimising traction and vehicle dynamics, the GenV enhances the vehicle’s driveline efficiency and features an Efficient Mode for reduced driveline losses.
BorgWarner adapted the GenV integrated electronic control module to match BMW’s driving characteristics and its specifications for improved traction and handling. The advanced software calculates and delivers pre-emptive as well as immediate response with high torque accuracy based on data supplied by the on-board electronics to provide exceptional dynamic performance. Without any driver input, the electronically controlled multi-plate clutch distributes power between the front and rear axles automatically.
In addition, the GenV AWD coupling improves fuel economy by providing only the requested amount of torque to the rear axle, optimised for nearly all driving situations. If necessary, full locking torque is available at any given time and speed, depending on road conditions and vehicle load distribution. For the first time, BorgWarner’s GenV coupling is equipped with the Efficient Mode functionality featuring an intelligent valve that manages the clutch lubrication to reduce losses. In this mode, the coupling provides better fuel economy when the all-wheel drive function is not needed.