Global reach: Gordon Day in the labs at GKN Hybrid Power
It’s not often that a technology developed in the high-octane world of motorsport filters down to the lurching buses that stop-start their way around the streets of London.
But that’s what’s happened with an electric flywheel which was originally developed by Williams Formula One and proved on the race track by Audi and Porsche. The system will be fitted to 500 buses in the capital over the next two years, generating predicted fuel savings of 20%. The flywheel is a tremendous example of concerted efforts by bus companies to reduce day-to-day running costs and ultimately cut the amount of CO2 their vehicles emit in cities.
The flywheel has been developed by GKN Hybrid Power, which has grand ambitions for the technology both here and abroad. “We have targeted the flywheel system at the bus market, locally first, and then hopefully it can be used on a global scale,” says Gordon Day, general manager for GKN Hybrid Power.
“Other applications include a portion of the HGV market with high stop-start content, such as fuel-delivery vehicles, airport vehicles or refuse vehicles. There’s also now a strong focus on the cost of the technology and as we drive that down, we anticipate that more of the worldwide truck market will become accessible.”
GKN Hybrid’s offering is a kinetic energy recovery system based on a high-speed flywheel made of carbon fibre that’s used to store the energy generated by a vehicle as it slows down to stop. When the driver brakes, a traction motor on one axle slows the vehicle, generating electricity at the same time. This electricity is used to charge the flywheel, spinning it at up to 36,000rpm. When the driver accelerates, the system works in reverse. The energy is drawn from the flywheel and converted back into electricity to power the traction motor. This reduces the work done by the internal combustion engine, and tests have shown that it improves the fuel economy of buses in urban settings by at least 20%.
The seeds of this technology were sown in 2007 at Williams Formula One, which wanted to develop KERS for the 2009 season. The flywheel went through two design iterations and was tested in an F1 car, although it was never raced.
Williams then formed a partnership with Porsche, developing a new version of the flywheel for the 911 GT3R, a hybrid car that won several races over two seasons. The technology proved its motorsport credentials again earlier this year, helping Audi to win at Le Mans with its R18 e-tron hybrid car.
“We have learnt an incredible amount from our relationships with Porsche and Audi, and are now on our eighth iteration of the flywheel,” says Day. Improvements to cooling conditions and thermal flows have enabled the GKN Hybrid team to more than double the average power from the system, boosting it from 23kW to 50kW, significantly improving performance.
The extreme environments found in motorsport have also delivered improvements in system reliability, while lessons have been learnt in the area of manufacturing process. “We have matured significantly and learnt a lot about quality control, getting each flywheel performing within a very tight tolerance window,” says Day. “Our end-of-line sign-off test is also comprehensive and well matched to both rig and track testing. Such testing is applicable to our bus ambitions as well; streamlined for much higher volumes.”
After its motorsport successes, Williams started to look at ways of commercialising its flywheel. The company quickly realised that its technology would be perfectly suited to the high stop-start nature of a bus with its high mass and large power requirements. “They were the same sorts of requirements that we had encountered in racing applications,” says Day.
He felt that the technology Williams had developed was unique. “It’s an electric flywheel. It has an integral motor generator unit; it has no dynamic seals, so there’s no shaft or power drive coming off it – you connect to it with electric cables. It’s a battery equivalent, so it’s charged and discharged as a battery would be.
“The advantages of this electric unit, in terms of packaging and flexibility in a retrofit bus environment, gives operators real options. Then there’s the efficiency of the transmission of power between the flywheel and the vehicle drive. That’s a particular strength of our technology.”
Williams started knocking on the doors of bus and heavy-duty vehicle makers, but found it difficult to get taken seriously. “Not surprisingly, a bus operator became our lead customer as it’s the operator that feels the result of the fuel bills.”
A relationship was built with Go-Ahead Group, one of the largest transport operators in the country, and a company that runs dozens of bus routes across the capital. A trial agreement was thrashed out, and Williams started looking at how it could make the motorsport technology work in an urban drive-cycle environment.

Gyro scope: GKN Hybrid Power's Gyrodrive technology is easily modified for use in other vehicles
ne area of alterations found necessary was a sturdier casing for the flywheel and Williams approached automotive group GKN as a supplier. That coming together proved to be seminal moment: GKN was so impressed with the technology that it bought Williams Hybrid Power from Williams Grand Prix Engineering to form GKN Hybrid Power.
The new company is focused on a complete hybrid solution, known as Gyrodrive, which includes the flywheel, an advanced electric motor, a gearbox, and installation. The Gyrodrive system is designed to last for the life of the bus and eliminates the need for battery changes.
Small-scale trials of the technology were carried out on a handful of Go-Ahead buses, producing real-world fuel savings of 20% – a figure that correlated closely with earlier modelling.
“Performance was largely as we had anticipated,” says Day. “There were perhaps more benefits than we had thought in heavy traffic conditions. The technology was shown to be working at every small braking event. The trials were also very positive when it came to drive-ability. The information coming back from Go-Ahead drivers was either neutral (they didn’t feel that there was a system onboard) or positive (with increased responsiveness while braking).”
Go-Ahead has placed an order for 500 Gyrodrive systems to be retrofitted to its buses over the next two years. The units will be built at a new GKN plant in Telford, with further development for other mass transit applications, including trams, construction and agricultural equipment.
“Initially, all production will be carried out in the UK. That’s our strategy into the medium term,” Day adds. The Go-Ahead order will lead to a significant ramp-up in production. “Compared to Williams, GKN is a truly global engineering company with a global footprint. So in terms of manufacture and deliverability, it offers an immense advance in terms of quick growth potential for the technology.
“It also has a wealth of engineering expertise across a range of sectors including aerospace, automotive, construction and mining. And it has a lot of composite expertise on a high-volume, process-orientated basis. So there are considerable advantages when looking to grow quickly into volume manufacture.”
Day and his team will continue to refine the flywheel technology. Retrofitting the Gyrodrive system to existing buses takes several day, but design and packaging optimisation can reduce that. GKN also wants to offer the technology to bus-makers and is developing a specific original equipment version of the flywheel system that will be more closely integrated with manufacturing procedures.
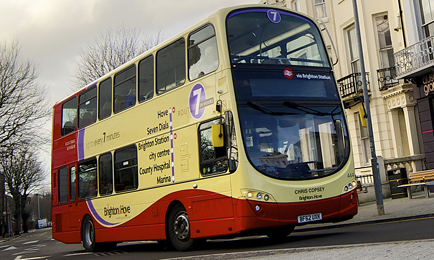
Driving range: Pems allow realtime measurements of operating vehicles following their normal duty cycles
Monitoring technology allows emissions to be reduced in Brighton
Brighton and Hove City Council is to redesign traffic systems to reduce emissions from buses at city-centre pollution hotspots.
While the exhaust emissions of new buses are tested over regulatory drive cycles during the development phase, little information often exists as to their actual emissions when in service. The council decided to run trials using an advanced Portable Emissions Monitoring System (Pems) to give a better understanding of the spread of pollution.
An area of air quality concern for Brighton is the central east-west thoroughfare of North Street. Bus route 7 was selected for the tests as it goes through this hotspot, travelling 9km in each direction with significant gradients throughout. The tests were carried out on a Euro IV vehicle fitted with exhaust gas recirculation (EGR) aftertreatment, a Euro V vehicle fitted with selective catalytic reduction, and a Euro V SCR-equipped diesel-electric hybrid vehicle. Each bus was instrumented with Horiba’s Pems equipment and artificially loaded with ballast representing a 70% passenger load.
The vehicles were tested on multiple trips and stopped at regular bus stops as they would on a passenger service. Different drivers and driving styles were used in testing one of the three vehicles so that the effects of these variables could also be assessed.
Measurements of each vehicle’s emissions of CO2 and NOx were recorded in real time. By detailed consideration of the type of emissions technology installed on the vehicle, estimates were also made of the proportion of NOx emitted as NO2. The emissions data was correlated with GPS measurements so that an accurate analysis of the effects of route topology could be made.
The three vehicle types followed the expected trend of CO2 and NOx – reducing from the Euro IV to V and from the Euro V to Euro V hybrid. However, it was also found that the certification level wasn’t necessarily a reliable predictor of the lowest comparative emissions performance at a particular location or instance in time.
No obvious influence of driver or driving style was observed on either CO2 or NOx emissions in this study (based on the data acquired while testing the Euro IV bus).
Looking at the results in detail across the whole of the route, it was clear that poor traffic flow on the westbound journey was perhaps the major contributor to higher NOx emissions in North Street. Erratic stop-start operation on this uphill stretch of the route, demanding multiple cycles of acceleration and braking, would be expected to challenge the performance of EGR and SCR emissions aftertreatment control systems, and rapidly depletes the batteries of hybrids. This strongly correlated with the realtime vehicle emissions data, which demonstrated significantly higher levels in the westbound and uphill direction.
A conclusion to draw from the study is that initiatives aimed at smoothing traffic flow at this location, and allowing buses to operate without unnecessarily frequent stop-start cycles, could have a positive impact on NOx emissions and fuel economy.
The results of the research were presented to Brighton and Hove City Council in July.
Jon Andersson, manager of aftertreatment and chemical analysis at Ricardo, which oversaw the trials, said: “The work provided some valuable insights into vehicle emissions at a location of known poor air quality. Pems equipment allows us to take realtime measurements of operating vehicles following their normal duty cycle.
“This approach allows us to understand exactly where and how emissions are being created. Armed with this information, fleet operators and local authorities will be better placed to make informed judgements as to the vehicle technology and traffic management improvements that will be most effective in reducing emissions at source.”