Even hundreds of metres away, on a raised platform, the heat from the red hot steel slab is debilitating. As it snakes through a succession of presses, rollers and jets of water, the slab is repeatedly squeezed, flattened and cooled.
Eventually the steel will be the body of a car - maybe the door, roof, or a structural component. But first, in the hot strip mill at the Arcelormittal Nippon Steel (AMNS) Calvert plant in Alabama, USA, it must be subjected to a process of sheer industrial machismo.
The slabs are heated up to 2300℃ in a triple furnace and sent down the line into a descaler to remove the first layer of oxides from the carbon steel surface. It then goes into the slab sizing press, a processing step unique to AMNS Calvert, that squeezes the slab down to 350mm thick. It then passes through a roughing mill to reduce it to between 125 and 80mm thick.
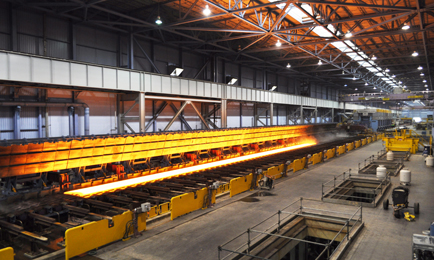
The hot strip mill at AMNS Calvert operates 24/7
The strip is then cooled through a 50m long laminar cooling section, the longest such section in the world, before being treated in a secondary descaler. It enters the finishing mill, where its thickness is reduced from between 30 and 65mm to between 1.8 and 28mm and its ends are sheared off. When the strip enters the finishing mill its temperature is between 960 and 1270℃. When it leaves it is 550℃. Finally the strip is rolled into a coil in the rolling shop.
The hot mill is cavernous, impossibly long and very hot. It operates 24/7 with a capacity of 5.3 million tonnes – one coil of steel is made out of every single steel slab. Engineers manipulate the cooling rate, thickness, and width of the strip to create steel of different grades for different applications. Any defects are detected by a series of cameras that are better than the human eye. The inspection system automatically classifies any defects according to severity and then decides how to proceed with the strip, which can be sent back to be rerolled.

Steel slabs arrive at the mill on barges from Brazil
These automated electronic inspection systems are integrated into the production lines throughout AMNS Calvert and are one of the features that its owners, Arcelormittal and Nippon Steel, cite as evidence that Calvert is the most advanced steel finishing plant in the world. Greg Ludovsky, vice president of global research and development for Arcelormittal, says that the hot mill is the standout feature of the plant. He says: "The hot strip mill's functionality is unmatched in the world. You can have a very unique deformation throughout the plant. The runner table allows you to do thermal treatment. Its power and cooling flexibility allows you to do things that other mills cannot. The hot mill is the crown jewel of Calvert."
Calvert is the largest newly built steel processing facility in the US for forty years. Lou Schorsch, chief executive of Arcelormittal in the US, says: "Calvert is a game changer for our company and the entire industry. Our most greedy engineers can't think what else to put in this place."
Despite its manteaux as world’s most modern steel mill, Calvert’s history has not been glorious. The plant has only recently come under the ownership of Arcelormittal and Nippon Steel. It was originally designed and built by Thyssenkrupp for almost $5 billion. It was opened in 2009, but was beset with teething problems and issues with the steel slabs it receives from a Thyssenkrupp plant in Rio de Janeiro, Brazil. In February this year Thyssenkrupp sold Calvert to a joint venture between Arcelormittal and Nippon Steel for $1.55 billion. Part of the deal is an agreement for Calvert to source its steel slabs from the ThyssenKrupp Brazil plant for six more years.

AMNS Calvert is spread over two miles in a straight line from the river its steel slabs arrives from
AMNS Calvert is a 2300 acre site, a series of extremely large, guadily coloured, monolithic buildings arranged in a two mile straight line from the Tom Digby river, from which it receives the steel slabs it processes. The plant employs 1550 people but is highly automated - combined with its remote location, it almost seems like a ghost town. From the hot strip mill to the cold strip mill and the facility’s four hot dip galvanising lines, there are only handfuls of workers around, usually watching screens, occasionally making adjustments to machinery. This is reinforced as you pass the storage yards, where rows of large black coils of steel are arranged in neat but enormous rows to cool outside after being rolled in the hot strip mill.
The hot mill is currently working at 80% capacity. The next step for Calvert is to expand the slab yard so that the hot mill can run at full capacity and to expand further down the line, for example in the continuous coating lines. The improvements are part of a planned $80 million technology expansion Arcelormittal and Nippon Steel are making to bring Calvert up to its full 5.3m tonnes capacity.

AMNS Calvert has the capacity to store tens of thousands of tons of steel coil and movement in the stores is highly automated
The steel coils move between the main buildings underground. The coil is unrolled and pickled with hydrochloric acid to remove the carbon surface, this turns the coils from black to the white colour more typically associated with steel.
The strip is then bought to the correct width, inspected with both a camera system and the human eye and then oiled. It is then stored in a large hall before it is supplied to customers. Calvert has the capacity to store 55,000 tonnes of steel.
The range of thickness for the steel is described as “huge” by Harold Van Bracht, director of the cold strip mill at AMNS Calvert, but to steel industry outsiders is tiny, between 0.3 and 3mm. “There is really soft steel and there is really strong steel and we use different technologies and heating and deformation processes to make the different products.”
The hot dip galvanising lines coat the steel with different substances to give it different properties. The main coating is zinc, which protects against rust, others are chrome and aluminium. The lines are continuously working, so the coils are unwound, welded together with a laser welding machine and then spooled before in giant vertical towers called “loopers” before and after they the baths to be dipped.
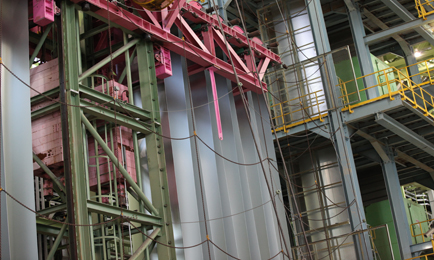
Giant tensioners called loopers help to smooth out throughput through the hot dip galvanising lines
The dip baths are kept at different temperatures according to the coating, for zinc it is 404℃. As the strip leaves the galvanising dip it at last looks like you would expect it to – it’s not such a leap of the imagination to imagine it forming the unpainted body of a car.
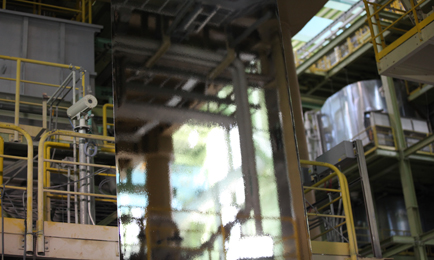
The hot dip galvanising lines coat the steel with substances to protect against rust and improve performance
Within the cold mill there is a pickling and rolling line dedicated to steels for the automotive sector. Calvert also has an ISO accredited lab on site which inspects, tests and certifies the steel for the automotive sector. The main test is for tensile strength – a sample is stretched to destruction to see how the width is affected, but samples are also tested for hardness and the roughness of the surface. The labs process 4,000 samples a week and the testing processes are as automated as possible.
Most of the steel AMNS Calvert produces is destined for car factories in the US and Mexico. The automotive sector is Arcelormittal’s number one customer globally. The company supplies 13 million tonnes of steel a year to the 183 million vehicle global automotive market. Lou Schorsch, chief executive of Arcelormittal in the US, says that the automotive market is growing rapidly around the world, and that by 2018 there will be 102 million more vehicles on the roads. Capturing that growth, most of which is which is in emerging markets like China and India, while helping automotive firms meet CO2 emissions targets, is the dual challenge his company faces, he says.
The elephant in the room though, is aluminium. Carmakers are increasingly using the lighter metal to help meet CO2 reduction targets for vehicles. The prime example is Ford’s F150 pickup truck, which has a largely aluminium body. The F150 is the quintessential American pickup. If successful, it is likely other US manufacturers will start to use more aluminium.
However, the company is bullish about the threat aluminium poses to its biggest customer base. Schorsch says: "The more turmoil and disruption there is in the market plays to the strengths of our company. We feel that with the right designs and steel's proven safety record we will be in the same place as the aluminium vehicles."
The response from steel companies has been the development of lightweight steels that offer superior strength and remain cheaper than aluminium. So-called generation three of advanced high strength steels are in development now.
Greg Ludovsky, vice president of global research and development for Arcelormittal says that Arcelormittal’s engineers work constantly to develop new steels that improve its properties. "Steel is uniquely capable of delivering functionality and cost in the automotive market. Over the last four decades the strength has been getting higher, but you would sacrifice formability. Not anymore. advanced high strength steels allow us to have cake and eat it.
"It was not long ago we introduced Usibor 1500. Now we are going to release another material that increases its strength by 30%. There is no other material in manufacturing or construction that shows that level of innovation."
Press hardened steels such as Ductibor and Usibor are offering car manufacturers the options they need to meet increasingly stringent CO2 reduction targets by reducing the weight of their designs. Steel has been the main material in cars throughout the 20th century. Whether that remains the case for decades to come is a challenge engineers and plants like AMNS Calvert are fully aware of and working to achieve.