The farming industry is having to explore innovative solutions to increase food production in the face of climate change, a growing global population and land and water shortages – as well as an ever-worsening skills deficit. While it may appear a traditional industry, the agricultural world has been undergoing a silent, yet steady technological transformation, embracing the latest developments in automation, robotics and the internet of things to stay competitive. Engineering firms, large and small, are realising that lessons from the factory floor can be applied to farming, and are seizing the opportunity to develop productivity-boosting agricultural technology.
In 2014, German engineering giant Bosch launched a start-up called Deepfield Robotics to focus solely on developing sustainable products for agriculture. Its first offering was BoniRob – an autonomous, four-wheeled robot that can detect and remove weeds quickly and precisely, doing away with the need for harmful herbicides.
Professor Amos Albert, general manager of Deepfield Robotics, says: “We are leveraging our expertise in sensor technology, algorithms, and image recognition to make a contribution to improving quality of life.”
The first BoniRob model dates back to 2008 and was developed together with Osnabrück University and agricultural manufacturer, Amazonen Werke Dreyer. Today, BoniRob has evolved to Mark III – it’s around the size of a compact car and uses laser sensors, video and satellite navigation to autonomously navigate fields, follow plant rows and turn automatically.
To travel safely across difficult terrain, the robot has four independently steerable drive wheels and can adjust its track width. Thanks to a host of environmental sensors – including lidar, inertial sensors, wheel odometry and the option of GPS for row detection and navigation – it can pinpoint its position to the nearest centimetre.
So, how does it work? Rather than replicate the complicated and time-consuming task of pulling out weeds, BoniRob is designed to crush them into the soil using a 1cm-wide mechanical stamping rod located on its underside. Through high-speed image processing, the robot is able to distinguish between weeds and crops by leaf shape. It can then eradicate small weeds that have just sprouted by driving its stamping tool 3cm into the soil. For larger weeds, the robot is able to repeatedly crush them with a cycle time of under 100ms.
Brushing-up on botany
BoniRob’s automatic image recognition uses machine learning to remember and identify the leaf shapes of various plants, as leaves of different crops or weeds can look very similar in their early stages. To achieve this, Bosch provided the robot with a large number of image files in which researchers highlight the weeds. “Over time, based on parameters such as leaf colour, shape and size, BoniRob learns how to differentiate more accurately between the plants we want and those we don’t,” explains Albert.
The robot has proved successful in identifying and removing weeds in tests run on a real carrot crop that was spaced about 2cm apart with an average of 20 weeds per metre. BoniRob can achieve a maximum of about 1.75 weeds per second at a speed of 3.7cm/s and a weed density of 43 weeds per metre – but at lower weed densities, speeds can reach up to 9cm/s.
BoniRob also plays a valuable role in streamlining crop appraisal, normally a laborious task undertaken by scientists in the field to decide which new plant varieties are worth pursuing further. The robot is able to rapidly analyse thousands of different plants with its scanners and cameras, recording the size and colour of their leaves, as well as the size and shape of fruits, growth forms, insect infestation, and chlorophyll content. This speeds up the time-consuming stage involved in getting improved crops to market, which can take up to 10 years.
Currently BoniRob would only be allowed to operate if fenced in or observed by a human. However Dr Slawomir Sander, senior research scientist at Deepfield Robotics, is hopeful that robot accuracy and crop safety will improve as sensors become increasingly accurate and software advancements are made. In addition, valuable discoveries in autonomous car research will help to accelerate their work, says Sander, especially from a legal perspective.
The BoniRob is commercially available for universities and research institutes at an introductory price of ¤250,000. “For farmers, we plan to design unique robots for special-use cases that will cost much less than the current model,” explains Sander.
Ploughing time
Across the pond, North Dakota’s Autonomous Tractor Company (ATC) has, as the name suggests, developed an autonomous tractor system in a bid to cut production costs and tackle labour shortages. It is installed on an existing tractor and is referred to as a “truly autonomous” system that doesn’t rely on GPS. It can be “trained” to do countless repetitive field tasks on its own, such as tilling, freeing up farmers to do other jobs. However, the tractor can still be driven manually if need be.
The system works using two of ATC’s patented technologies, the AutoDrive, for autonomous navigation and perimeter safety, and eDrive – a diesel-electric drivetrain that replaces the tractor’s original transmission, differential and axles.
Kraig Schulz, chief executive at ATC, says: “This is the only diesel-electric system out there for tractors, and our autonomous system is the only one that doesn’t require a driver or rely on GPS.”
The eDrive is a modular diesel-electric drivetrain technology that’s said to be easier to maintain and repair and more fuel-efficient than traditional systems. Simplified wheel motors ranging from five to 125hp replace the transmission, differential and axles to create a system that’s easier to manage with sensors and software.
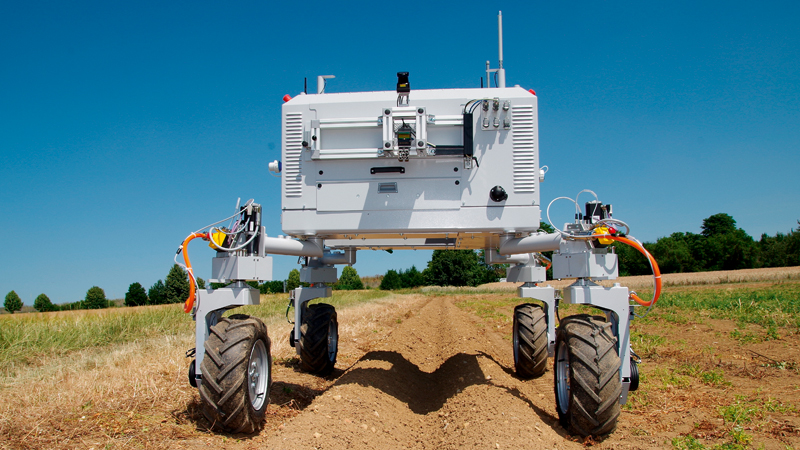
Farmers’ costs cut
There are just two components to the tractor after eDrive is installed – a diesel generator set and the wheel motors – and either one can be replaced in less than two hours with basic equipment found on any farm. This not only means that tractors are more compact, but Schulz says farmers can expect to save 50% in total ownership costs, with a payback period of three to four years.
“Fuel economy alone saves you 25% versus a traditional drive,” says Schulz. “When you can work night and day you can have smaller tractors – transporting the big boys is a pain – improving logistics and putting a lighter footprint on the soil, which is a huge cause of soil compaction and yield loss. You can expect to pay £350/hp versus closer to £700/hp for traditional tractors.”
The AutoDrive consists of two components, ATC’s proprietary Laser-Radio Navigation System (LRNS) and FieldSmart artificial intelligence software.
The LRNS supplements GPS for navigation, which, as anyone who owns a satnav will agree, can often prove unreliable. Additional data comes from a proprietary laser and radio frequency positioning system that provides independent distance, speed and direction data. For additional navigation and safety data, the LRNS also includes wheel encoders and internal measurement units. A full 360º broad-spectrum sonar system, which Schulz says isn’t dissimilar to those used in submarines, helps the vehicle avoid obstacles from 10m away. ATC has plans to add other safety features, such as infrared scanning, over time.
Both these systems work together to provide “full perimeter safety” and ensure that the tractor can operate without supervision from the farmer once trained to do a task such as plough a field – including performing turns and avoiding obstacles. Once this training is complete, the FieldSmart software imputes the path (or fills in the blanks) for the remainder of the field and confirms with the farmer that the plan is acceptable. The AutoDrive system can then take full control of the vehicle’s steering, engine and vehicle speed.
Safeguards built in
“Using our in-field LRNS system, you can drive a tractor with its implement [farming tools attached to the tractor] as you would normally, and the tractor learns everything you’re doing, where you’re doing it and replicates this exactly,” explains Schulz. “Today’s autonomous tractors all still require a driver. None that I know of actually control the implement or provide perimeter safety and remote monitoring. If something goes awry, the AutoDrive safely stops and it sends an SMS – or even a photo – to the farmer so he can work out what the problem is without even being there.”
If a tractor loses its sense of position, identifies a problem in the engine, implements or motors, or its sensors notice a power line or stray farm animal in its path, it will brake and cease operations. The brake mechanism stops at a distance of approximately 5ft at 6mph.
A small autonomous implement control (AIC) kit helps to control tractor implements and incorporates an electro-hydraulic valve that ties into existing hydraulic lines as well as a set of strain gauges that measure the position and tension of the implement behind the tractor. The LRNS system works with the AIC circuit board to send and receive control data and commands to raise and lower the implement, monitor performance, toggle spraying valves and ensure proper functioning. The eDrive technology is fully developed and began shipping to ATC’s customers late last year.
“We have a lot of work to do to get the major automatable applications worked out,” says Schulz. “We are working with implement manufacturers to speed up that process and expect to have the navigation system with auto-steer out by mid-2016, and then move to full automation towards the end of the year.”
Panasonic has also been looking to get a slice of the agricultural pie and has developed its own prototype for a tomato-picking robot. Dr Tamao Okamoto, manager of the production engineering development centre at Panasonic, explains: “The company was very interested in finding an alternative labour force as there will soon be a shortage of tomato farm workers. It saw robots as a possible answer.”
Variable shapes
The major challenge was to create a robot that can efficiently handle a product that varies in shape and size. “Besides the fruit itself, the harvest also has a range of different conditions such as sunlight and temperature,” says Okamoto. To solve this Panasonic is utilising trial and error as well as methodically collecting and analysing tomato data from farms.
To maintain the harvest performance and prevent damage to fruit, Panasonic is currently developing two technologies. One is high-accuracy 3D recognition. This is achieved using time of flight sensors that measure the distance to an object and a colour camera to collect data which is combined using an original algorithm. “The algorithm creates a high accuracy and robust recognition which is unaffected by the characteristics of the tomatoes and their environment,” explains Okamoto.
The second technology revolves around the picking mechanism of the end-effector. Designed in a ring shape, the robot harvests the tomato by hooking the stem. This mechanism prevents damage to the tomato and allows for the difference between the recognised and actual position of the fruit.
Okamoto says the robot still needs development to achieve better harvesting performance, and is aware that conventional tomato-picking robots can only currently harvest under certain conditions.
However, early signs are extremely positive, and the robot received positive feedback from researchers and developers of harvesting robots at the International Robot Exhibition 2015.
“We think our touch-free robot has an advantage against other robots which touch the fruit and can potentially cause it damage,” says Okamoto.
The next step for the development team is to match the harvest performance with cost before it’s decided whether to push forward with commercialisation.
With technology giants like Bosch and Panasonic investing time and energy into the development of agricultural robotics and automation, it seems that the time is ripe for other engineering firms to jump on the bandwagon.

Spotlight: Tomato picking
The Panasonic tomato-picking robot harvests without ever directly touching the crop to prevent damage such as scratches and bruising. Instead, it harvests the tomatoes by pulling the stem with a ring-shaped end-effector. This method adopts advanced 3D recognition and mechanical technology which has been developed for use in industrial robots and home appliances.