A new era of high-speed rail will be ushered in later this year when testing of the fastest production train in Europe finally gets under way. The Bombardier Zefiro V300, with its striking long nose and sleek aerodynamic construction, will set pulses racing as it hurtles along the tracks at a phenomenally rapid 360km/h.
Italian state-owned railway operator Trenitalia will be forgiven for revelling in the glory of unleashing such a state-of-the-art train. But, away from the spotlight, in an office in Derby, a small group of British engineers will also enjoy a sense of satisfaction for the hugely important role that they have played on the ground-breaking project.
These engineers, 35 or so in number, make up Bombardier’s UK bogies division. And it is these men and women who have developed the active suspension-enabled bogies that will allow the V300 to reach its top speed, while handling the enormous loads involved.
Nathan Cartwright, head of design at Bombardier’s bogies division, is rightly proud of the team’s achievements. He uses a comparison with motorsport to highlight the challenges: “To put it into context,” he says, “a Formula One racing car weighs about 650kg and achieves maximum speeds of around 300km/h. It carries one person and the engine is designed to last only for a few races.
“Each Zefiro bogie will travel for long periods at 360km/h with a load of up to 32,000kg upon it and have its first major overhaul after five years, during which it will have travelled 2.5 million km. While the demands upon the two products are obviously different, the engineering accomplishment is surely equal.”
Chief engineer Justin Keeley puts it another way. “This is mechanical engineering at its limit – in terms of fatigue, analysis and structural design. And the great thing is that it’s British.”
The story of how this world-class cluster of bogie expertise came to be can be explained by the fractured nature of railway history. Some of the division’s engineers started their careers at British Rail, before privatisation and a series of takeovers – involving companies such as ABB and Adtranz – led eventually to the bogies team being housed at Bombardier’s Litchurch Lane train-manufacturing site in Derby. The facility now boasts a rare mix of people and skills, and can produce complete bogie designs, including vehicle suspension, wheel-sets, drivetrain and brakes.
Historically, most of the bogie division’s work has supported Bombardier’s mainline train-building programmes, such as the current contract to make 130 class 377 vehicles for Southern at the Derby plant. Typically, the work will include a full package of services – from initial understanding of client requirements through to concept and detailed bogie design, as well integration with traction and gearbox suppliers.
Cartwright says: “The detailed design phase often requires the use of finite element analysis to define the structural performance of all the components, making sure all the relevant standards are worked to, all the equipment has enough space around it, and all the tolerances are correct.
“Throughout the whole process, we work with the train manufacturing team to ensure it can all be produced in the most cost-effective way. It’s a typical convergent process – it starts wide and tapers down quickly.”
While the bogies division has a central role in all UK train-building programmes at the Derby site, the quality of its work means it is also winning a strong reputation internationally. Bombardier has sold tens of thousands of bogies to China as the emerging economic superpower rapidly expands its railway network. Much of the design and development work on those contracts has taken place at Derby.
Indeed, it was a Bombardier bogie designed for the Chinese market that acted as the basis for the Trenitalia contract. Keeley says: “The initial product was designed in Europe and manufactured in our Chinese factory.”
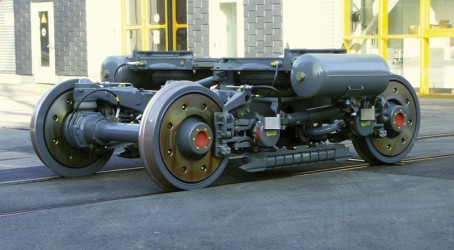
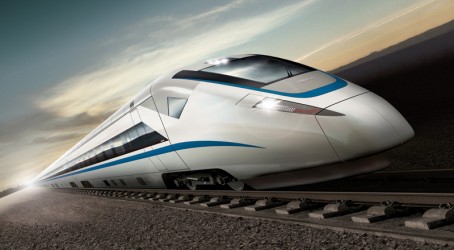
But the team had to do things differently for Italy, he adds. “We realised the requirements for the Italian market were different from those for China. There were differences in the kinds of welding accepted, the supply base, and the requirements of the safety analysis. There’s a different homologation process. The standards are different. We had to use an Italian wheel-set designer, and it might want to manufacture in a different way – maybe shrink-fitting rather than push-fitting the wheels on.”
The end solution offered for Trenitalia was an active lateral suspension design – a bogie technology that provides a way of manipulating the suspension, principally to achieve a better ride for passengers. The design features a hydraulic actuator that sits between the bogie frame and the carbody, making it possible to influence lateral movement.
On straight track, the carbody “floats” on secondary suspension air springs which have a low lateral stiffness. When the train goes through a curve, the bogie follows the curve first, bringing the carbody with it. What controls this movement are the lateral bumpstops between the bogie and carbody centre pin. The low lateral stiffness of the secondary suspension allows the carbody to move laterally during curving until there is bumpstop contact, which then ensures the car follows the bogie.
The problem with bumpstops is that they have to be stiff to limit the movement of the heavy vehicle during curving. This rise in stiffness affects the lateral ride quality of the vehicle, which makes things less comfortable for the passengers. At high speeds, the force transferred to the carbody during curving becomes much higher, and the passenger ride comfort deteriorates significantly.
At 360km/h, the bogie frame undergoes violent forces and accelerations, which are transferred to the rubber bumpstops. So the carbody goes from a position of low lateral stiffness to a rapidly increasing bumpstop stiffness, resulting in greater force transmission to the carbody that the passengers can feel.
The Bombadier engineers have tackled this problem. “With active lateral suspension,” says Cartwright, “the actuator software analyses a series of input signals from accelerometers on the bogie and carbody. It then applies force inputs to the carbody to condition the ride and prevent bumpstop contact during curving. It is this reduction in bumpstop contact that improves the ride performance.
“The Chinese bogie didn’t have that. We designed it in. It wasn’t just a case of exchanging the lateral damper for a hydraulic actuator – we had to redesign the central section of the frame to take it. And because it’s a hydraulic actuator, it needed an oil-cooling mechanism which had to go in the middle of the frame. That had implications for frame stiffness. There were challenges from a structural mechanics point of view.”
The design and development of the active lateral suspension bogie wasn’t the end of the work in Derby. The team’s engineers were required to ensure it was fit for manufacture, and they got fully involved with production of the first prototypes. These were manufactured at Bombardier’s Siegen facility in Germany, with full technical support from the Derby operation.
The first Zefiro V300 train for Trenitalia has now been built by Bombardier in conjunction with its partner, the rail transport engineering giant Ansaldo Breda, and will soon undergo slow-speed testing in Italy. Keeley says: “When the first bogie was welded up in Poland, this complicated frame of 100-plus plates worked perfectly. It was a successful jigsaw that had an elegance and simplicity of form. There were some modifications in the wiring, but we were delighted with the mechanical side of things.”
Later this year, a super-lightweight trailer bogie based on an existing Bombardier design used for the UK Voyager and Meridian trains will be manufactured for the 250km/h ICx regional trains to be made by Siemens for the German railway operator Deutsche Bahn. The concept for the ICx bogies was also piloted out of the Derby office, with Deutsche Bahn being specifically keen to tap into the team’s expertise in inboard bearing bogie technology.
This unconventional bogie layout offers a low-weight frame and wheel-set solution, and reduced unsprung mass. The result is a compact, lightweight but robust design with significant operational benefits, such as reduced energy consumption and noise emission and less track damage.
The inboard bearing concept harks back to BR’s days, says Keeley. “Much of the work was done in the 1980s, and the guys who developed it brought it with them to Bombardier. It developed within Bombardier from a concept to something that works.
“For 20 years, the only people using it were in the UK, driven by track access costs. Then we sold one to Norwegian railways. And now everyone is starting to realise that this inboard bearing bogie design matches the needs of the world in that it is light, doesn’t destroy the track, and reduces overall costs.”
However, although the Deutsche Bahn ICx will use a technology honed on British railways, the operational characteristics of the German rail network will mean design changes for the Bombardier bogie being supplied.
“For instance,” says Cartwright, “we had to upgrade the frame to handle increased axle loads. The bogie concept remained the same, but it had to be ‘Europeanised’. We had to have a track brake, and added an extra disc brake in the middle of the axle. We uprated the primary and secondary suspension. The focus many years ago was on large castings, but now it is on smaller castings. So we redesigned the frame to suit that.”
The Deutsche Bahn project is now at a critical stage. All the parts for the first prototypes have been procured and fabrication will take place over the summer. Bombardier’s engineers have worked closely with their Siemens counterparts on the project, dispelling any suggestions of adversarial rivalries. Siemens is responsible for the main contract, with Bombardier providing the trailer cars and the bogies.
“Deutsche Bahn likes buying German, but we had the bogie design that it wanted,” says Keeley.
Looking forward, there are other contracts on the horizon that the Derby bogie division is keen on winning. Its Flexx Eco bogie, with inboard bearing technology, is being considered for railways in countries such as Russia and Singapore. “We also have a launch customer in Sweden, so there is a lot going on,” says Cartwright.
A Flexx Eco variant will also be offered as part of Bombardier’s bid for the train-building contract for the Crossrail project. That bogie will require space for the shoe-gear, which will mean reworking of the design. “We are in the final stages of bidding for Crossrail, and it’s fingers crossed,” says Keeley.
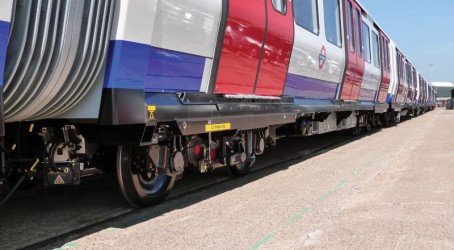
Flexible frame bogies tackle Tube track twist
Innovative flexible frame bogies that can cope with challenging track conditions have been designed by Bombardier’s Derby division for London Underground’s deep-level Victoria and Northern lines, and for its sub-surface Metropolitan, District, Circle, and Hammersmith and City lines.
Justin Keeley, Bombardier’s chief engineer in the bogies division, says: “With a normal bogie, you have four wheels with a rigid H-frame. But London Underground wanted something that could deal with track irregularities while still being steady. It didn’t want lots of movement and sway.”
The solution was a bogie that has two halves, bolted together with rubber joints to accommodate track twist. “That design was developed specifically for London Underground,” says Keeley.
The Litchurch Lane train factory in Derby has produced deep-line versions and is now building the S stock for the sub-surface lines. This model is bigger than the deep-line variants, and that has implications for the bogie design. “The S stock for sub-surface is a lot bigger – the axle load is higher, and it runs a bit faster – but essentially it has the same design,” he says.
The London Underground work will sustain train-making at the Derby plant until at least 2015, after which Bombardier hopes to win a 600-carriage contract to build the Crossrail trains. But it faces competition from German rival Siemens.
An early day motion put forward by Chris Williamson, Labour MP for north Derby, has called on the government to make sure the Crossrail trains are built here. Williamson says the work would guarantee 10,000 jobs in the East Midlands and in the supply chain. Without the work, the Bombardier plant will close, ending British train manufacturing, he says.
Bombardier to be joined by Hitachi with Co Durham train plant
Bombardier’s Litchurch Lane site in Derby is the only train manufacturing plant in the UK. But that is set to change soon, with Japanese giant Hitachi building an £82 million facility at Newton Aycliffe in County Durham where it will make the Super Express trains for the Great Western main line and the East Coast main line.
The Newton Aycliffe factory will build 596 cars over the course of two-and-a-half years, with production commencing in 2016. The greenfield-site facility is being overseen by Darren Cumner, Hitachi’s manufacturing and plant manager, who is responsible for construction and fit-out. “It’s an exciting time,” he says. “I have been responsible for new train plants before. But this is in the UK, so that makes it high-profile.”
Cumner already has a good idea of what the factory will look like. Each train carriage will flow through a maximum of 51 stations, with value added along the way. The aluminium body shells will gradually be filled out in a defined sequence, starting with equipment such as insulation and wiring, then floors and ceilings, with larger components such as the heating and ventilation added towards the end.
To meet output requirements, the plant will use a takt time manufacturing approach, says Cumner. “Takt times will drive production of one carriage per day. Every cycle time on each station has to be completed in less than eight hours.”
The plant will be based on Hitachi’s main production facility in Japan, so stringent quality levels can be replicated. Cumner has been back and forth to the Japanese plant, learning from engineering, manufacturing and logistics teams there. “Hitachi has been making trains for many years,” he says. “So we have been going through things station-by-station, picking up where the quality control points are.
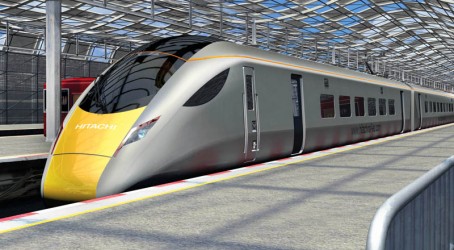
“At the moment that is the key focus for me. Even though we might position each station in a different sequence, we want to be sure that our facility produces the sorts of high-quality trains that we make in Japan. So the facilities might look different, the materials movements might be different, but the quality gauge will be the same.”
The Newton Aycliffe plant is also being “future-proofed,” says Cumner, in anticipation of other orders. While it will initially build the Super Express trains, Hitachi is also bidding to win the Crossrail rolling stock order and contracts in mainland Europe.
“We are not designing the factory just for Super Express, we are designing it to make trains forever,” he says. “We’ve got to future-proof it. We know what the UK rolling requirement looks like, but we are also taking into consideration European gauging and height of trains, for instance.”
New manufacturing techniques will be introduced over time. On Super Express, all the train bodies will be friction stir welded in Japan. But Hitachi is looking to transfer that technology to Newton Aycliffe.
“There is large-scale technology transfer already,” says Cumner, “but friction stir welding here might have been a risk on this product. We are risk-averse – that is key to delivering on time. But we have a friction stir welding resource in the UK and we know what investment will be necessary.”
Construction of the Newton Aycliffe plant is expected to start at the end of this year. It will employ 730 people. Fewer than 2% of the workforce will come from Japan.
Recruitment of engineers will start soon, adds Cumner. “We want to put some engineers in Japan in advance of the start of production so they become experts. In the next three months we will scope that out and we will be looking for those people, particularly in the areas of quality and manufacturing engineering. There will also be a long-term mentoring programme with Japan.”