In many sectors of the global economy, “recession-resistant” is a term that would be applied only with extreme caution, but the aerospace industry seems to be bucking the trend of contraction or feeble growth. It’s been forecast that 23,000 commercial jets will be built in the next 20 years, so engineers working in the supply chain can, perhaps, sleep a little more easily than their counterparts in other industries.
At Exova, a global testing group with a lab focused on aerospace, in Bridgwater, Somerset, it’s acknowledged that the commercial jet market is the main driver of growth for the company, although it also focuses on general engineering, construction, fire safety, vehicle testing, and chemistry and microbiology for food production.
“Aerospace is the fastest growing sector, certainly in Europe,” says Paul Lawrie, sales director for aerospace in Europe. “We’ve seen about 15% growth year-on-year over the past two years, despite the obvious problems in the global economy. I think aerospace has been affected, but it’s one of the industries that has proved to be a bit more recession-resistant.”
About 50% of Exova’s revenue comes from Europe, with the Americas generating about a third and the Middle East the other important region. The company works closely with Airbus, but also with Boeing, Canada’s Bombardier, GKN and BAE Systems.
Dr Roger Digby, group technical director, says: “We are recognised to be a provider of technically demanding services that involve not just a simple test but the advice that goes with it – a discussion with the client on the type of test they might require and how to solve the problem they’ve got with their product. We focus on relationships.”
The principal spur to aerospace growth is demand from emerging markets, especially China, which are growing more quickly than mature ones. But even in the US and Europe aircraft are ageing and need to be replaced.
Another driver is advances in materials – such as the adoption of ever-increasing amounts of composites and new alloys in airframes. The amount of composites in new aircraft has grown from 5% in the early 1980s to 50% on some more modern designs such as the Airbus A350.
“Every aircraft pushes the boundaries,” says Lawrie. “For the A380, for example, one of the challenges was to make it as fuel-efficient as possible by making it as light as possible.” The target was to use three litres of fuel per passenger per 100km. The aircraft actually came in slightly below that because it used carbon fibre materials and lightweight aluminium structures. “The challenge is always how to make the component both strong enough and lighter; those two don’t normally go together.”
All this growth and technological change means work for test houses such as Exova. The firm plays an important part in the design process for components for not just aircraft but also helicopters and rockets, where it typically works with suppliers to determine the suitability of materials for a certain design right through to testing smaller parts to assess their failure rates and responses to loading and stress. It is possible, for example, to test molten titanium before it is cast. The metal can be assessed in the laboratory and the composition altered before the manufacturer makes the casting.
Exova is typically involved right from the early stage of an aircraft’s design, or during the research and development programme, and is subject to the stringent certification standards that define the industry. “We’re validating that a material ‘does what it says on the tin’, effectively,” says Digby.
“We will validate every step of the process of manufacture or design to make sure the material is still performing the way it should, and that it hasn’t been altered in any way that might be detrimental to its performance.”
It is not always possible to standardise tests for materials or components, so sometimes bespoke test equipment is developed at Bridgwater and produced for a particular project. “Quite often, materials are developed specifically for the aircraft: it’s a big industry and Boeing and Airbus have close relationships with their suppliers,” says Lawrie.
“We support that by doing the testing to create the data that they need, so we work for the suppliers and the manufacturers.”
Exova, which is owned by private equity, is investing £2 million in aerospace this year and in 2013. Bridgwater, said to be the first lab in the world to achieve Nadcap (National Aerospace and Defence Contractors Accreditation Program) accreditations for both composite and metallic materials, has already seen investment in support of the A350 and A400 supply chains. Further money is expected to be used to increase static and fatigue testing capability.
Why do Airbus and Boeing need Exova’s labs around the world to carry out test work? “Both the major OEMs have these sorts of capabilities,” says Digby. “But in both cases it’s not their core competence. What they are there to do is to design the best possible aircraft, and produce it in a way that makes sense. They don’t necessarily want to be experts in routine testing.”
Exova carries out little work in the aftermarket, where components are typically replaced under maintenance regimes that determine when they are reaching end-of-life.
Were the worst to happen and an accident occur, in theory the failure of a component could affect the business, but it would have to be demonstrated that the testing process was deficient. “If we’d been negligent in our testing we would be liable for the failure,” says Digby, “but, in practice, it’s unlikely that a series of tests would lead to something falling out of the sky.” Apparently one of the biggest causes of damage is catering trucks being driven into aircraft, or “ramp rash” as it is sometimes referred to.
It is difficult to predict exactly what the materials used in the next generation of commercial jets will be. For now, there is a “huge backlog” of orders for short-range Boeing and Airbus aircraft that are primarily metal, with a small proportion of composites. “There’s a lot of work for us still to do in supporting the production of metallic airframes,” says Digby.
“The interesting question is what the next generation of aircraft will look like – will there be more composites, as with the A350 and the 787, or will the metals guys come up with more advances that make the metallic opportunity more attractive, whether that’s from a weight or a manufacturing point of view?”
Manufacturing in metals is cheaper than composites, and the cost of ownership of an aircraft is a balance between the acquisition and in-service costs. “So there’s a complex equation,” says Digby, “whether the manufacturing costs are sufficiently low to offset an increase in weight and a greater in-service cost. Those are the sort of things that are being considered.”
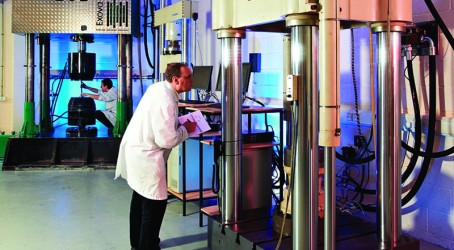