There’s no doubt that British manufacturing owes a debt of gratitude to Professor Lord Kumar Bhattacharyya, the passionate industrialist and educator who has been the driving force behind the hugely successful WMG facility at the University of Warwick for the past 35 years.
Back in the late 2000s, Lord Bhattacharyya used his not inconsiderable powers of influence to persuade the Indian carmaker Tata to buy Jaguar Land Rover from Ford. That inward investment represented a turning point for one of Britain’s most iconic companies, ushering in a golden period of product demand that has ultimately created thousands of jobs.
Bhattacharyya was the kingpin in the deal, and he never doubted that the coming together of the two companies would prove beneficial. “I’ve known Ratan Tata for many years. I introduced him to JLR, he’s a car enthusiast and is extremely knowledgeable,” he says.
“I haven’t been surprised by how successful it’s been. Tata’s culture is one of long-termism. It puts engineers at the forefront, and it gives them the money they need. With JLR, it realised that unless new products were done well, then they wouldn’t sell. And that required significant investment in research and development.”
That introductory moment was an encapsulation of what Lord Bhattacharyya is all about. He’s a firm believer in the potential of British industry to compete in globalised markets, while also embracing the fresh thinking and change of culture that foreign companies can bring. It’s something he’s encountered many times during his distinguished career.
“British industry had to go through a lot of pain in the 1970s, but it learnt from companies like Toyota, who went on to change the way we think about how to make good products,” he says.
Lord Bhattacharyya’s involvement in British manufacturing spans several decades. Born in India as the son of a university professor, he chose to study engineering at university because he had always considered it to be the “noblest of professions”. At the age of 21, and keen to progress, he was selected for a two-year graduate apprenticeship at Lucas, then one of the main suppliers to the British car and aerospace sectors. And so in 1960 he packed up his possessions and took a slow boat to these shores.
It was a move that was to serve him well. “I’ve never regretted becoming an engineer. And I always believed that British engineers were the bees’ knees,” he says.
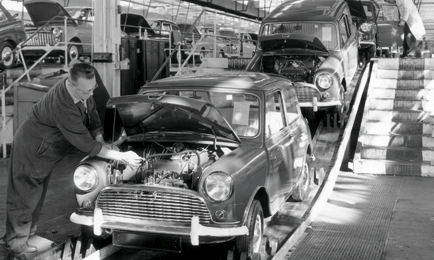
In the early 1960s, the British car industry was a good place to be, with brands like Morris, Austin and Jaguar held in high regard around the world. The iconic Mini, made by the British Motor Corporation (BMC), was rolling off production lines in huge numbers.
Lucas was a big company and major supplier. One of its subsidiaries was CAV, headquartered in London, making fuel-injection equipment for diesel engine manufacturers, and it was here that Bhattacharyya cut his teeth, working his way through the business as part of his graduate apprenticeship.
“It was a very exciting time,” he recalls. “I was visiting CAV suppliers, and also going into the factories of the OEMs that it supplied to. I was placed on a fast-track learning programme, and was also offered the chance to do an MSc in manufacturing engineering at Birmingham University, which I did while still employed. It was a good decision, as it was also the heyday of the machine tool industry.”
Lucas had formed strong links with Birmingham University and Bhattacharyya subsequently went there to do a PhD. Eventually the university offered him a lectureship, being keen to tap into his knowledge of engineering production. “I became the founder of the manufacturing systems unit at Birmingham, which became one of the fastest-growing parts of the engineering faculty,” he says.
“I understood the carmakers, having come through industry. We won a lot of funding to do projects with large car plants like Longbridge, looking at areas such as transfer line efficiencies and the development of new inspection techniques. We brought a lot of thinking into it to help carmakers analyse, model and simulate what was going on.”
The closer that Bhattacharyya got to the carmakers, the more he realised that trouble was coming down the track. Having enjoyed the ‘golden age of the automobile’ in the early 1960s, with sales kept steady by a new era of affluence, the industry had started to rest on its laurels. The problems came from the top – many of the carmakers were run by autocratic elderly men too set in their ways and resistant to change. The Mini symbolised the malaise at the heart of the sector: poor cost control and manufacturing inefficiencies meant BMC was losing £30 on every one it sold.

During this period, Bhattacharyya had visited Japan several times on business, and he was shocked by what he’d encountered. “Toyota had started exporting and I was very interested in what they were doing. In fact I was gobsmacked. I came back from Japan wondering to myself ‘my god, will we ever survive?’. Toyota’s combination of technology and efficiency was mind-boggling. I could see the writing on the wall – and I started to write up my reports based on these sorts of concerns.”
Bhattacharyya felt that those at the top of the British car industry in the late 1960s and early 1970s were dismissive of the threat posed by global competition. “They had a complete lack of understanding about what was happening internationally,” he says. “Countries like Japan and Germany were moving at very fast rates. But in the British car industry there was a lack of investment and companies were using old machine tools. As a result, I could see the start of industrial decline.”
It also came down to a lack of management expertise. “Part of the problem was that we lacked the quality of intellect to look at things in a different way,” he recalls. “There wasn’t the sort of exposure to global competitors that you would have expected senior people to have. So their answer was always the same – let’s bring in management consultants. The consultants would say ‘cut this, cut that’, the company would shrink, and eventually disappear. They were stuck in the past and the management consultant culture flourished.
“Another problem was that a lot of industry was nationalised. There was no government policy and the unions had their own agendas. There was never a united front in terms of how we should make the step change in technology and products that was required. Industry had a product deficit generally. It concentrated on the soft options.
“Japan was taking a more holistic view – they were thinking about their suppliers, about how products were designed, how they were made – they were totally integrated in all that they were doing. They were assessing international competitors and were working out how to leapfrog them.”
To this day, Bhattacharyya defends the shopfloor workers and engineers who lost their jobs in the industrial shakedown that ensued. “Fundamentally we had very good people in this country, very good engineers. But they weren’t led. It was never that our people weren’t capable, it was that global changes in manufacturing weren’t addressed. It was a lack of policy by the government and a lack of understanding of the intellectual base that was required within companies.”
Some good came out of those troublesome times. Having switched to an academic role at Warwick University, Bhattacharyya became determined to help British manufacturers fight back and secure a long-sustainable future. In 1980, he founded Warwick Manufacturing Group (WMG) at the university, with a mission to improve the competitiveness of organisations through the application of value-added innovation, new technologies, and skills development. He set about bridging the gap between industry and academia, while persuading British companies that they needed to boost investment in research and development.
“When I came to Warwick, one of my biggest concerns for British manufacturing was how we were going to go about updating our people. We needed to inject a knowledge base into our remaining companies as a matter of urgency. So when we started, that was our genesis – we worked with the research councils and big companies like BAE, Rolls-Royce, Shorts and GKN to attract the best people. Jaguar Land Rover supported four research chairs at WMG. We encouraged companies to engage with us, to allow their staff to come and study master’s degrees.”
Today, WMG is one of the world’s leading research and education groups, with more than 500 people working across six buildings on the Warwick campus, plus collaborative centres in seven countries. At the last count, WMG had an annual programme of £180 million which includes industrial and in-kind support from a wide range of companies including Airbus, Jaguar Land Rover, Bosch, Siemens, Network Rail, Tata and GlaxoSmithKline.
Perhaps the most exciting developments in 2014 have been the launch of four new R&D centres: the Energy Innovation Centre, the Automotive Composites Research Centre, the International Institute for Nanocomposites Manufacturing, and the Advanced Steel Research Centre, which complements Tata Steel’s long-term investment in their new centre at the University of Warwick. A fifth, the National Automotive Innovation Centre, is set to open in 2016.
Bhattacharyya is rightly proud of what’s been achieved at WMG. “We have received £15 million of the capital cost from the Higher Education Funding Council for England,” he says. “We’ve paid mostly for all the buildings – we don’t owe anybody anything. If you rely on government – the psychologies change, policies change, it can be hard to handle.”
There’s also an international flavour to the work at WMG. Bhattacharyya has a network of contacts in places like China, Malaysia, Thailand and South Africa, where WMG’s reputation for the strength of its research and academic learning is second to none. “We have a record international intake here now,” he says. “There is tremendous demand. I could go to China tomorrow and get 5,000 quality students.”
Bhattacharyya also advises the government on matters of industrial policy, and has played a key role on several large-scale inward investments in the UK. He is an immensely valuable advocate for science and technology within Westminster’s corridors of power, having been elevated to the House of Lords in 2004. From this position of knowledge, he makes some positive predictions about the value of manufacturing in this country.
“I’m very hopeful about the future,” he says. “There’s a much better understanding within government that, without manufacturing, we don’t get enough employment. We need manufacturing for sustainable growth. As an advanced nation, if we are not technology-based, it will be difficult for us to compete. We might as well be an offshore financial sector.”
But in truth he doesn’t really believe it will come to that. Bhattacharyya retains a sense of drive and ambition that will see him continue to work with government to ensure that manufacturing stays high up the political agenda. “We need government to stick with having a long-term policy,” he says. “Sustained long-term thinking is crucial for this nation. Government can be a driver in this area, working jointly with industry and academia.”

Warwick a hotbed of innovation Getting into the University of Warwick by car is a tortuously slow process, with traffic backing up along surrounding roads on most weekdays. This congestion, perversely, is actually a sign of success: the main campus is undergoing a flurry of construction activity. The congestion is a short-term pain for long-term gain.
The foundations are being dug for the National Automotive Innovation Centre, a £100 million partnership between Jaguar Land Rover, Tata Motors and WMG/the University of Warwick, which is due to open in late 2016. It will focus on the challenges of electric vehicles; carbon reduction; and smart and connected vehicles.
The innovation centre’s building will occupy 30,000m2 next to WMG’s facilities on the University of Warwick campus. It will be home to 1,000 academics and engineers from the partner companies to work on a range of advanced projects.
Meanwhile, there is also a planned new building concentrating on fundamental steels research and advanced propulsion research. The Advanced Propulsion Research Laboratory is being set up to develop next-generation technologies in the propulsion systems that are central to the future competitiveness of the automotive industry. The research scope will focus on internal combustion engines, hybrid and electric systems, lightweight technology and advanced control systems.
An independent Advanced Propulsion Centre, funded by the Department for Business, Innovation and Skills and the Automotive Council, is also situated on the Warwick site.
But WMG/the University of Warwick’s activities are not all centred around the automotive sector. There’s also an International Institute for Nanocomposites Manufacturing, a £4.1 million facility that is looking to exploit polymer processing techniques. The institute houses characterisation laboratories, a wet chemistry laboratory and processing hall.
And at the Institute of Digital Healthcare academics are working with engineers from global firms to work out how new technologies might change the way that health services are delivered. With sensor performance improving at a rapid pace, it is easy to visualise a future where devices such as smartphones could be used to monitor and relay health information to medical practitioners.
Also on site is a dedicated engineering and support team, based in the International Institute for Product and Service Innovation, which works with small companies on innovative design methodology.
Lord Kumar Bhattacharyya, founder of WMG, says: “In a global environment, technology and products are fundamental to developments in all industries. We have taken the knowledge and expertise we have built in the manufacturing sector and applied it successfully to other sectors.”
Bhattacharyya biography
- Professor Lord Kumar Bhattacharyya was born in Dhaka in 1940 and graduated in mechanical engineering from the Indian Institute of Technology, Kharagpur.
- Completed a two-year graduate apprenticeship at Lucas Industries in the 1960s. Then he was offered the Lucas Fellowship and entered the University
- of Birmingham where he attained an MSc in engineering production and management and a PhD in engineering production.
- Before completing his PhD at Birmingham, he was appointed as a lecturer and began the process of establishing a manufacturing education programme for industry there.
- In 1980, he was invited by Lord Jack Butterworth, then vice-chancellor of the University of Warwick, to start a premier manufacturing, teaching and research group and here he became the professor of manufacturing systems. These were the foundations for the Warwick Manufacturing Group, which today is known simply as WMG.
- WMG now boasts an annual programme of over £180 million which includes industrial and in-kind support.
- Bhattacharyya was appointed a CBE in 1997 and knighted in 2003. In 2004, he was made a life peer as Baron Bhattacharyya of Moseley in the County of the West Midlands. In 2014 he was elected to the fellowship of the Royal Society for his contribution to engineering research and education.