David Keeley, engineering manager at the Irish-owned containers business Suretank, has some advice for companies thinking about investing in product lifecycle management (PLM) software: “Ignore the vendors,” he says. “Ignore the literature. Ignore the academics. Decide for yourselves what PLM is.”
Suretank, whose products include tanks for liquids and secure containers for equipment used in oil and gas industries, is one of what appears to be a growing number of mid-sized companies – and firms in non-traditional PLM-using sectors – that have come to PLM from new directions and are finding benefit outside the usual range.
“In engineering the starting point has often been on CAD management,” says Keeley. “But we wanted to look at areas that provide more value for Suretank. Forget about CAD: we’re much more interested to begin with in capturing customer requirements and loading them into a technical specification, and then managing the delivery of customer needs.”
Suretank isn’t approaching PLM from a traditional starting point. Other new users too don’t quite fit the usual image of mega-corporations using PLM to handle vast amounts of mechanical CAD data and to collaborate across huge supply chains.
Devon-based Sub10 Systems is a new small company that is making millimetre wave point-to-point wireless Ethernet bridges for customers in mobile telecoms and elsewhere. Nick Redfern, new product introduction manager, is an advocate of PLM but, like Suretank, he isn’t coming at it from a CAD perspective: “You could structure the output of your CAD to ripple through the PLM system, but that’s not necessarily appropriate for electronics manufacturing, because CAD really isn’t the centre of our universe,” he says.
Sub10 is using PLM to capture and manage product data: to give a single and simple system that handles a wide range of data – not just design information, but also decisions about changes and updates, and about conformance to external and internal standards. That sounds like much of what the long-standing PLM systems offer, but Redfern says there is a difference: “I want it simple,” he says. “We’re starting small, and cost is an issue. I wanted something that would allow me to expand at the rate I want to.”
What Suretank and Sub10 represent is a new breed of PLM user that’s a long way from the giants of the aerospace and automotive industries that were the original targets of the software vendors. What they also reflect is a change in approach on behalf of those vendors, plus some newcomers, towards the development of systems that can now be installed gradually and that don’t need vast arrays of expensive IT consultants to deploy them or expensive licence fees to operate.
PLM has had a rough ride in the dozen years or so since the term was coined. Big-name vendors, most with a background in CAD, have been criticised for over-hyping ideas and for over-emphasising the “all-singing, all-dancing” elements by adding in yet more complexity in areas such as collaboration, simulation and visualisation that could be afforded – and were perhaps needed – only by the biggest global groups.
Suretank’s technical director Dermot Short voices some of the concerns. “PLM was always mentioned in the same breath as enterprise resource planning as systems that were the reserve of large organisations with huge IT departments,” he says. “We don’t have an IT organisation.”
More recently, though, Short has been able to convince his boardroom colleagues that PLM is the way to go because of a shift in PLM focus and the arrival of new players. Suretank is deploying PLM360, the cloud-based system that marks Autodesk’s entry into the market. The bonus, Short says, is that his company can take it at its own speed. “The users will be implementing it; it’s not something that has to be managed by a team of consultants or a high-powered IT department,” he says.
Redfern at Sub10 echoes these sentiments. He is using the Aras open-source PLM system and takes some services from the Danish PLM implementation company Minerva for difficult tasks, but essentially he does the work on it himself. “And later on I can add other functions and grow it,” he says.
Leon Lauritsen, partner at Minerva, says: “The mid-market has been a problem for the big PLM vendor companies because they focus so much on the mechanical CAD side of the equation. In a mid-size company, you have to ask just how many designers there actually are. You can end up focusing all the effort on maybe 5 to 10% of the company, and if it’s just two or three guys they can usually go on managing the CAD files in the way they’ve always done.”
In small to mid-size companies, in fact, what PLM can offer is often not the all-encompassing vision of sophisticated multi-coloured and textured models zapping around the globe. Rather it brings orderliness to complex product information of all kinds, and what it frequently competes against or replaces is an ad-hoc system of spreadsheets and Word files or handwritten notes.
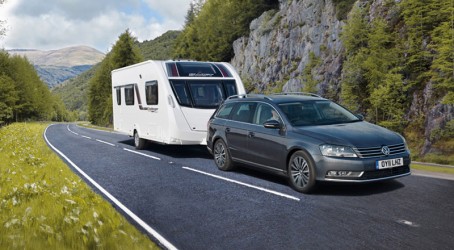
Complexity is not only an issue for big companies: Redfern says a bill of materials for one of his radio systems might have 170 lines on it, and one item on a line might have 300-400 parts with references.
PLM automates the management of product data of all sorts, and it’s particularly good at bringing order to complicated data-heavy jobs, and to operations where many functions need to access information but where, in traditional ways of working, all would have different ways of filing their data.
That may all sound a bit mundane in comparison to the grand visions enunciated at vast PLM conventions by charismatic industry luminaries, but in practice it’s the way that quite a few long-standing adopters of PLM have been using their systems anyway, and they don’t find it unexciting.
Ash Dhir, engineering manager at the Swift Group, the UK’s biggest maker of caravans, motorhomes and holiday homes, has used Windchill PLM from PTC for many years. He says: “We’ve automated a lot of the administrative functions within each role that fed information from one part of the business to another. Those manual functions are now pretty much non-existent. Our core team of designers who use the software know that it will take care of the admin functions.”
The business driver for PLM, says Dhir, is the complexity of handling a large and fast-changing product portfolio. “We do a total product range refresh on many of our 350-plus models on average every three years, but every year there’s refresh in areas right down to colours or graphics or bedding. It always means more engineering,” he says. “It means individuals can focus on the roles they were employed to do rather than dealing with consequential stuff. Our output is greater and the accuracy is improved too because the software is managing the data.”
Data management goes back to the original concept of PLM from the early years of the century, before it got overlaid with “the vision thing” and apparently inextricably linked with CAD. Lauritsen at Minerva wonders whether “it might have been better if we’d invented a new name for what we’re now doing with PLM, because few seem to have a handle on what PLM really is: they think they know, but they don’t”.
It may be that some industries outside the original targets have a better handle on PLM. Viewed as an information management tool with version control and instant accessibility as prime assets, PLM has become established some distance from its roots in engineering design in industries such as fashion and retail, which have complicated supply chains and logistics, often involving suppliers on the other side of the world.
Gabriel Garcia, PLM manager at the North American hunting, fishing and outdoors clothing and equipment retailer Cabela’s, says his group has used product data management (PDM) for a few years to assemble “tech packs” that detail new garments to be made by suppliers, most based in Asia. But that system is now being upgraded to PLM, using PTC’s FlexPLM.
What this means, says Garcia, is that selected outside contract designers have been included for the first time in design and development discussions for the spring 2014 range: “PLM gives us a full 360° view of the development process and we’re extending it next year with access for some of our partners to see the tech pack, the materials they use and the jobs they’re working on.”
But the joy of PLM, he says, is that other people with other types of product-related information can add their data into the single system. For example, the company’s Hong Kong office, which handles day-to-day supplier issues locally, can put fabric test results or prototype evaluations on in real time. That will speed up supplier selection. Compliance issues needed for items shipped into the US can be built into manufacturing routines and documented through PLM.
And the PLM system will also link into customer service, so if a Cabela’s customer phones up to say that they like a particular colour or fabric, the voice on the end of the phone can delve into the back catalogue and the upcoming items list to find things that match.
Fashion’s use of PLM is going further, though. Judy Gnaedig, PLM business leader for the fashion technology group Lectra, says the initial push into PLM in fashion came from big Western brands wanting to keep tabs on the complexities of their goods over attenuated supply chains through web-based interventions and “single versions of the truth”. She says: “The core part of PLM is the PDM that pulls all this data together, and then you add in calendar management and budget management too.”
Supply chain and logistical considerations about sending goods to the fashion houses of the West got Chinese clothing manufacturers into PLM. “It got pushed out of the starting blocks when suppliers went global,” says Gnaedig. But she sees a new trend: Chinese clothing manufacturers not particularly interested in exports but keen to tap into the huge growth in China are using PLM to achieve this. “The name of the game has changed and it’s now about being fast and managing the calendar and the critical path,” she says. “The West may be being a bit left behind here.”
Go back a dozen years, and part of the original vision of PLM was that it might integrate different kinds of product information into a single “backbone” system that would be the product equivalent of the transactional, financial information held in enterprise resource planning systems. Maybe that was too ambitious for the time for all but the biggest groups where CAD was the driving force. But with today’s PLM systems it’s becoming relevant and practicable to more people. And it needn’t cost an arm and a leg. n