There are several staggering aspects about the F-35 Lightning II fighter aircraft project. The first is the numbers involved. The defence programme, which will run until 2035, is the most expensive ever, anywhere. The US is projected to spend $323 billion on it. Around 3,900 of the aircraft will be built – 2,443 will go to the US, 680 to programme-partner nations and roughly another 800 to other countries around the world. This is truly the world’s next generation of fighter aircraft.
The second impressive aspect is the technology involved. The F-35 is, arguably, the most advanced aircraft in production in the world. It has a stealthy, supersonic design and is equipped with an elaborate network of sensors and an ability to share data. This fifth-generation fighter has a top speed of 1,200mph (1,931kph) and a range of 1,450 miles (2,333km). As a comparison, the Harrier, which it replaces in the Royal Navy, had a top speed of 735mph (1,180kph) and a range of 350 miles (563km).
A third surprising aspect is that bits of the aircraft are being made on the outskirts of Basingstoke by a small, family-run engineering company. RE Thompson makes the casings for the batteries on the plane. Yet RE Thompson is far from unique – it is one of 500 British firms in the F-35’s supply chain, according to lead developer Lockheed Martin.
Around 15% by value of each F-35 will be made in Britain during the next 25 years. The programme will support approximately 25,000 British jobs during that time, ranging from small companies such as RE Thompson to major aerospace firms such as BAE Systems, Rolls-Royce and GE Aviation.
The UK is the only “level one” partner in the programme and has 48 of the short take-off and vertical-landing (STOVL) variant (see box, overleaf) of the F-35 on order, at a cost of £100 million each. Total British investment in the programme is estimated to be around £1 billion. The UK is the first country outside the US to receive the aircraft, and expects the third to be delivered this summer.
However, British firms are not lesser partners in the programme. Many are supplying complex parts, such as electronics, avionics and power systems. An example of the kind of advanced engineering being supplied is shown by Rolls-Royce’s lift system for the STOVL variant.
The project depends on a high degree of international collaboration, says Philip Dunne, minister for defence equipment support and technology. “The F-35 Lightning II is one of the most complex defence programmes in the world, with many countries, governments and forces involved. International collaboration is at the heart of the project,” he says.
“Lockheed Martin would admit the foreign partners make it more difficult to manage. But the economies of scale made possible share the cost and provide a global footprint that would otherwise be unobtainable,” he adds.
The aircraft will operate until the 2050s and, says Dunne, the economic benefits will be spread over the long term. There will be a huge worldwide fleet of F-35s that require support, technological upgrades and refitting. Infrastructure for support will need to be developed and maintained, and other platforms – current and future – will have to be configured to make them interoperable with the F-35. Almost £5 billion of contracted
work has already been placed with the UK supply chain, the government estimates.
“This is the most valuable defence programme in the world at present,” says Dunne. “Its success is important to Britain. It is important to defence, because it provides our armed forces with the cutting-edge military capability that underpins our security. And it is important to our economy – creating investment, profit and jobs.”
BAE Systems is a principal partner in the programme, alongside Northrop Grumman. Chris Allam, senior vice-president responsible for F-35 at BAE, says the 3,900 aircraft that are expected to be built will be worth £1 billion a year to UK industry at the peak of the programme. The company has so far invested £150 million at its site in Samlesbury, Lancashire, to manufacture parts for the aircraft.
The work that BAE had done on previous relevant projects helped it to secure its place on the programme, says Allam. “Our leading position on the F-35 programme has come about largely thanks to our heritage and the manufacturing technology we invested in for the Typhoon programme. Our F-35 pulse production line will be producing one fuselage a day when we hit rate production.”
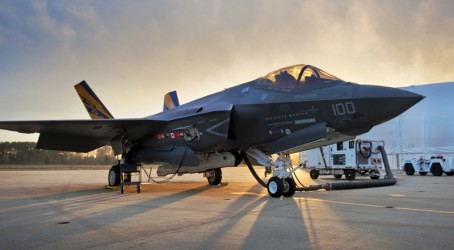
But the company is not resting on its laurels, he adds. “Our place in the programme is not a right. We have a constant focus on driving down cost and improving efficiency, and on investing in education and skills training, to ensure we have a pipeline of skilled staff.”
BAE has 50 British suppliers on the F-35 project, including GKN Aerospace. As well as supplying the aft fuselage, GKN is making the cockpit canopy and some of the engine components.
Gavin Wesson, general manager at GKN, says that participation in the F-35 programme has instigated £14 million of investment in the company, particularly in the area of composite materials. “The F-35 is extremely important to GKN,” he says. “It’s a significant growth accelerator that has prompted us to invest in new technology,
facilities and people to promote a leap in innovation.
“The electrothermal ice protection we are providing is a world-leading technology, designed and patented in the UK. We’ve invested in machining at Filton, a new composite assembly facility at Cowes, and a robotic metal spray at Luton. 150 people are directly employed in the UK for F-35, highly skilled engineering and manufacturing jobs.”
The idea that the F-35 programme has spurred innovation is echoed by Jonathon Walton, European military accounts and government relations leader at GE Aviation. The firm, which has 11 manufacturing sites throughout the UK, is supplying the electrical power system for the aircraft.
“We like to think of the electrical system as the heart of the aircraft. It has to cope with massive amounts of energy generated by the engine and distribute it throughout the aircraft. There is massive variation in loads and demands,” says Walton.
An integral part of the power system is the lithium-ion batteries contained in the enclosures supplied by RE Thompson to GE. While GE employs 5,000 people in the UK, RE Thompson employs 33. Nevertheless, Matthew Shaw, head of sales at RE Thompson, says the programme is vital to the firm and, as with BAE Systems, its participation is built on success supplying to the Typhoon programme.
“We have invested more than £1 million in machining equipment since then. Our headcount is up by 10% – in other words, three people. We’ve opened up a second site and it’s driven us into areas we have never done before, such as the coatings the casings require,” says Shaw.
Although it’s not obvious on a first look at the F-35 project, the economies of scale that are involved actually work both ways. The programme’s global footprint reduces development costs. But it also spreads the economic benefits. As well as supporting thousands of jobs at BAE Systems and Lockheed Martin, the project is incentivising innovation and supporting new jobs in hundreds of small firms.
Jet set: countries worldwide participate in fighter project
The F-35 Lightning II is available in three main variants: the conventional take-off and landing F-35A; the short take-off and vertical-landing (STOVL) F-35-B; and the carrier-based (CV) F-35C. The aircraft is a single-seat, single-engine, multi-role fighter, and can be equipped for both air-to-air combat and air-to-ground combat, as well as for reconnaissance.
The jet is intended to respond to current and future threats for air force, marine corps and navy, says Lockheed Martin, prime contractor. The UK, Canada, Italy, the Netherlands, Turkey, Australia, Denmark, and Norway have signed up, though some of those are hedging how many they will buy. Israel and Japan have ordered the F-35, and South Korea and Singapore are considering it.
The $40 billion development cost has been shared with partner nations, although the bulk comes from the US. Northrop Grumman and BAE Systems are principal partners. Final assembly takes place at Lockheed Martin Aeronautics Company in Fort Worth, Texas. Northrop Grumman in Palmdale and El Segundo, California, are manufacturing the centre fuselage, while the aft fuselage and tails are being made by BAE in Samlesbury, Lancashire. Lockheed Martin in Fort Worth is manufacturing the forward fuselage and wings.
Flight testing is being conducted at Fort Worth, at Edwards air force base in California, and at naval air station Patuxent River in Maryland. Additionally, the STOVL and CV variants will undergo sea trials onboard American, British and Italian aircraft carriers.
Lockheed expects to sell more than 3,900 F-35s. As of February, 187 jets had been ordered or delivered, with 36 deliveries planned this year. However, several partner nations are reducing orders because of the recession and a doubling of development costs.