The modern foot soldier is better kitted out today than at any time in military history. But while new electronic equipment such as scopes, night-vision gear, GPS, laser designators, map displays and other items brings welcome capability, it also adds weight and becomes a cumbersome burden to lug around.
Indeed, according to the Ministry of Defence, increased electronics means the average soldier now carries 4kg of batteries for a 48-hour rural mission, rising to over 10kg for some other roles. There is also little battery standardisation at present, with a mixture of different sizes and shapes, and primary and secondary (rechargeable) cells, and an assortment of connector types.
For critical systems, soldiers don’t want to risk losing power, so they often replace the batteries before they have run down. Patrols often return with a lot of partially spent batteries, which are often discarded without thought.
Little wonder, then, that engineers are thinking about how this situation might be improved. One concept under consideration is a wearable power system that would involve webbing or other gear made from textiles with electrical channels made of conductive yarn woven into them. These channels could transport data as well as power, and could form part of an advanced personal area network connecting numerous devices.
The wearable system could feature a main power unit which all the different devices would connect to, improving standardisation and reducing waste. The system could assign a priority to each device, so the most important kit would be the last to fail. It would also save the
40 minutes a day that the MoD estimates soldiers spend just changing batteries.
“Dismounted soldiers in current conflicts are massively overloaded in terms of the amount of weight they are having to carry,” says James Fisher – business development manager at Roke Manor Research, the Hampshire-based engineering consultancy that is leading work into lighter power systems. “That increased weight burden is accounted for by new equipment such as body armour, weapons and ammunition, but also to a huge extent by communication systems and force protection equipment such as jamming devices. Consequently there is an increasing requirement to carry batteries to power these systems. And it is likely to get worse in the future with a proliferation of devices that draw power.”
The Roke research effort is looking at the problem from two angles: reducing the power needs of the equipment soldiers carry, while also looking to reduce the weight of power generation equipment itself through the development of improved battery chemistry and advanced technologies such as fuel cells. In terms of the former, for instance, Roke is looking at advances in display technologies that have emerged in the civilian sector.
The Amazon Kindle book reader, for example, is based on an electrophoretic screen design that delivers a very good power efficiency. If soldiers could use such display technology on PDAs to read maps or receive technical instruction from commanders, they would be using significantly less power than they do on existing military-spec display equipment.
Roke is also interested in other civilian technologies such as using cellular 3G communications systems on the battlefield. Historically, defence communications systems such as Bowman use VHF radio, a technology that is very symmetrical in the way it was designed in terms of its architecture. Such systems have a lot of functionality and capability in the device carried by the soldier, thus adding weight. But with cellular architecture, a lot of the complex functionality sits within the base station rather than the handset. Its power consumption compared to a traditional VHF radio system is therefore considerably less. And as it’s a civilian technology, an awful lot of money has already been spent in driving down the power consumption of the mobile phone devices which could benefit the defence industry.
In terms of the power generation equipment itself, the main thrust of the research is to reduce the estimated 14 different battery types that dismounted soldiers carry in theatre. Roke has been assessing methods of having one single relatively large battery that distributes power across the range of equipment that the soldier has to carry.
But there are challenges to address with such an approach: one of which is the nature of the primary power cell. Roke has looked at most of the different battery types that are currently available on the market, some of which are quite novel and are covered by military classification. It has also looked at the whole range of battery chemistry and the amount of power it is possible to get per gram of weight that the soldier has to carry.
Roke is also looking at how to distribute power across the body. Ideally soldiers want equipment located on their person where they need it, rather than where is convenient for how it can be powered. There are a number of architectures that might be used – ranging from one central power source which then distributes power to a number of secondary rechargeable devices located around the body. Roke has looked at solutions for weaving power distribution cables into clothing, for example, and that method in turn raises challenges in terms of how to distribute power across small air gaps.
“A soldier’s weapon, for example, is not directly linked to his body,” says Shaw Green, consultant engineer at Roke. “So if you are going to locate a battery on his person, you need a way to get that power across air gaps and on to the weapon. One of the more recent pieces of work we have looked at is to use an inductive coupling technique to bridge the gap. It works in a similar way to an electric toothbrush – you put the toothbrush and the charger in close proximity and there’s an electrical field that transfers energy from one device to another.
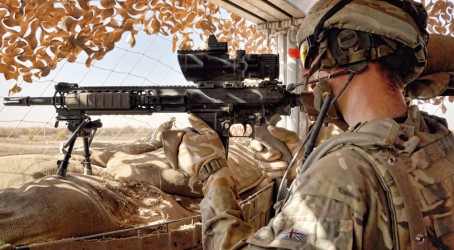
“The challenge is one of ergonomics and orientation. You need to keep the two devices in close proximity and closely aligned with each other. There are a number of options in terms of where to locate the coupling points – you can imagine you could do it by grating the weapon up against your shoulder. That would create quite a nice contact point.”
So what might a wearable power system actually look like? The first driver would be the need to have the weight of the primary power source located optimally on the soldier, probably in the backpack. Weight distribution makes an enormous difference – where it is carried can be more important than how much weight is being carried. A few extra few pounds on a soldier’s back is not as burdensome as the same weight on a helmet or on a weapon.
But connections to these peripheral areas require new thinking. For example, through the use of webbing or other gear made from textiles with electrical channels made of conductive yarn woven into them, it could be possible to have a connection in a soldier’s glove that would power a weapon for as long as it was being held. For helmets, possible solutions include magnetic connectors that would tear away easily and not impair mobility.
Companies such as Intelligent Textiles are experts in conductive fabrics and have managed to solve issues such as shielding of the wires and multiple buses to ensure redundancy of power loops. Roke has also done a fair amount of forward-looking research into advanced materials such as carbon nano fibres to bring such power distribution systems to the fore.
The personal power grid would also open up new recharging possibilities. Engineers have looked at pockets with inductive coupling to recharge devices placed in them. The same type of coupling could also charge the whole system from an external source, for example while the wearer is inside a vehicle. The wearable power system could also incorporate energy harvesting devices to recharge itself. Systems currently under investigation include backpack-mounted solar cells, piezo-electric boot heels and power-generating knee braces.
The power system could also carry high-speed data transmission. If there is a power distribution network running around the soldier – perhaps woven into the fabric – then it makes sense to consider using the same approach to distribute data around the soldier, as devices that generate or receive data also need power. Whether or not you strictly use the power system to do this is open to debate – but a parallel system using similar techniques, routing etc, seems to make sense from an integrated system point of view.
For example, a video stream from a weapon sight could be conveyed to a helmet-mounted display. From there it could be sent on to a communications unit for transmission to other squad members.
“If you are going to distribute power around a body there is a similar requirement to transmit data,” says Green. “You’ve got data coming into the soldier across the broader communication network via his radio and there would be a need to distribute that information to various devices that might be located around his person. There might be data going to the scope on his weapon or to some form of head-up display on his helmet, and you might want to build flexible displays into clothing on his arms. There’s a need to get the data to the right place. So it would appear to make sense to develop a network for power in tandem with a network for data.”
There is obviously big potential for weight-saving technologies such as wearable power systems within a military environment. But looking forward, says Roke, the major obstacles to adoption are not necessarily technological. A greater hindrance is likely to be the tendency of companies in the defence industry to work in isolation, therefore missing out on the advantages of standardised equipment and interfaces. Without collaboration, it could be a long time coming.