The UK’s first F-35 Lightning II fighter took to the skies recently for a series of tests. The programme to produce the fighter jet is the world’s largest single defence contract and it has not been without controversy. UK officials are still dithering over which of the aircraft’s three variants they want, and this political chatter has dominated coverage of the project.
But behind the scenes, significant developments have been made in the manufacture of the F-35. Manufacturing processes have had a total overhaul, taking influence from the automotive sector. Advanced production techniques are being honed, and components look set to roll off the line with unprecedented levels of accuracy and speed.
Several companies in the UK are involved in the manufacture of components for the fighter. Rolls-Royce is producing the LiftFan engine that powers a short-take-off-and-vertical-landing variant, and BAE Systems is making the aft fuselage and the vertical and horizontal tails. So far, 70 sets of these have been shipped from BAE Systems to Lockheed Martin in Fort Worth, Texas, for assembly.
Last month, BAE Systems opened an extension at its Samlesbury site in Lancashire. The building is the second part of a three-phase plan to ramp up production from the current level of a set of parts for one aircraft a week to one a day by 2016.
Since 2001, the company has spent £150 million on buildings, infrastructure and specialised plant and machinery at Samlesbury. Chris Allam, senior vice-president of the F-35 programme, says: “We’re using state-of-the-art machines and manufacturing techniques to ensure that we can meet the rates of production that the F-35 programme demands.”
On the factory floor, the temperature is tightly controlled at 21°C to stop materials swelling or shrinking. Future plans for the factory will change it to a set-up more like an automotive production line than an aircraft plant. Usually, aircraft production revolves around a static station where the plane is gradually pieced together. But the manufacture of the F-35 will involve a moving product, just as in an automotive plant.
Vijay Panchal, assembly transition manager, has the job of getting the factory ready to meet the one-a-day production rate. He says: “We looked at how higher-volume manufacturers produce products, and one of the things that we learned quickly is that products are handled significantly differently.”
The new extension will accommodate two production support systems, designed by BAE and US firm Novotech, that will run the length of the building. A third system will be added during the third phase of expansion to come.
“It will be the heartbeat of what we do. Products, parts, suppliers, tools, support staff will all be geared up around this production system,” says Panchal.

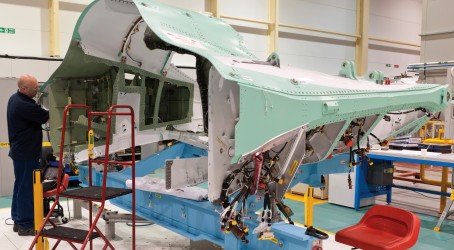
A monorail will transfer the product between 21 stations. At each, workers will have 15 minutes to complete their tasks before the system moves the part to the next station. It will take four minutes to move the parts between stations – a process that today can take hours.
Panchal adds: “We are hoping to employ 250-300 people on this, working a two-shift system of days and nights, four days a week.”
The benefit of moving the product is that fewer tools are required, and the line-up is faster, says production director Tim Boness. “In static production, you need five or six places, so you have to duplicate the tools. From day one, the decision was not to spend money on tooling.”
Instead, the F-35 team decided to use what is known as the digital thread. In this process, the three-dimensional digital design data makes its way onto the factory floor to computers that control the alignment of parts using a 3D interactive application.
Engineering manager Dr Paul Needham says: “Gone are the days where we have lots of drawings and we manufacture back to micrometres. What happens today is a huge step forward.”
Once produced, the left and right booms of the aft fuselage get married up using a laser tracking technique. A hard tool replicates the forward wing of the aircraft at Fort Worth. During assembly of the two aft fuselage parts, lasers project blue marks that indicate how far the product is from the digital model. The whole process is controlled to within the thickness of a human hair.
The assembled aft fuselage is then sent to Fort Worth, more than 4,000 miles away, along with the digital data, which is loaded into an electronic mating system. “The aircraft gets wheeled in and moved into the position of the points that we have here. It marries up to the wing section in a matter of hours,” says Needham.
Laser tracking was used in the production of the Typhoon aircraft, but with F-35 the technology has been developed further and used more exhaustively. Boness says: “Using digital technology instead of lots of tools guarantees the repeatability in the products.”
As a result, less time is needed for inspection so the build is faster. Levels of accuracy are achieved that until now were impossible to measure. This accuracy is important because the tight tolerances of the outside of the aircraft give the jet its stealth qualities.
Fitting the airframe and the skin together is a complicated process that involves drilling a pattern of 800 holes in both to align perfectly. Ian Bradshaw, head of F-35 assembly operations at BAE, says that the positional accuracy of these holes is less than 1/1,000th of an inch. Gone are the days of calibrated crowbars and oversize power drills fitting fasteners in the holes, he adds. “When you see the size of these products, it’s impressive that the overall accuracy is within the thickness of a human hair.”
The nozzle bay doors, which open at the back of the aircraft to allow the engine nozzle to swivel down through 90deg, are developed using one of the most complex production techniques in the military aircraft industry. Manufacture involves a fusion bonding and super-plastics forming process.
The door starts life as four sheets of titanium that are heated to 900°C and put under 1,000 tonnes of pressure. Under these conditions, the sheets bond to each other. “It’s not a weld – it’s a true molecular bond across those four sheets of titanium,” says Bradshaw.
With this cutting-edge manufacturing, the F-35 programme employs 2,000 people at BAE’s Samlesbury site. The programme safeguards these jobs. Allam says: “F-35 is a critical part of the military aerospace industry in the UK and critical to the future of the site.”
MoD vacillates over which variant to buy
The F-35 comes in three variants – conventional take-off-and-landing, short-take-off-and-vertical-landing, and aircraft-carrier-landing. The UK has yet to decide which type it will buy.
Originally, the Ministry of Defence sought to replace the Harrier jump jets with the short-take-off-and-vertical landing F-35B version. But in September 2010, the strategic defence review ruled otherwise, saying that the multi-mission capabilities of the F-35 meant it could replace the Tornado GR4’s reconnaissance role as well as the Harrier, and that the aircraft-carrier-landing F-35C variant might be best.
Replacing the Tornado with the new fighter would leave the UK with two types of fast jet, Typhoon and F-35. Now officials are debating whether to stick with the original plan and procure the B variant. A final decision is expected soon.
Aside from the landing mechanism, there are differences between the B and C variants. The C type carries more than 2,000kg more fuel than the B version, which powers it for a further 533km. The F-35C has larger wings so it handles better at lower speeds. But if the UK were to go for this variant, the Queen Elizabeth-class aircraft carriers would need an upgrade to accommodate the jets.
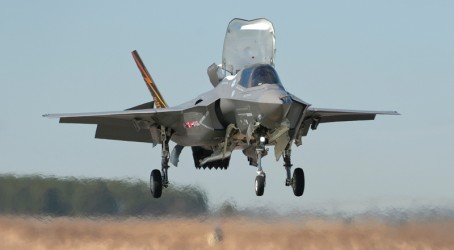
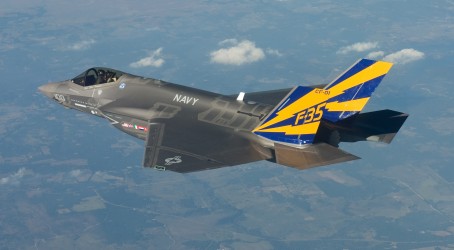
The C version is fired off an aircraft carrier by a catapult, and as it lands onboard a hook catches an arrestor cable. Fitting these ‘cats and traps’ to the new aircraft carriers is likely to be expensive.
The MoD is considering using an electromagnetic launch system, which is still being tested, rather than the conventional steam-driven catapult system that the US Navy has been using for years.
Paul Livingston, UK aeronautics director for Lockheed Martin, says: “I believe the cost and technological risk of putting those cats and traps onto the carrier is probably what is driving the UK to look at what is the right decision.”
Going for the B variant would give the MoD more flexibility than with the C type, as the short-take-off-and-vertical-landing capability means it can land much closer to a specified site or on a smaller ship than the Queen Elizabeth-class carriers. But the B version costs 10% more than the C variant, and has less space for weapons.
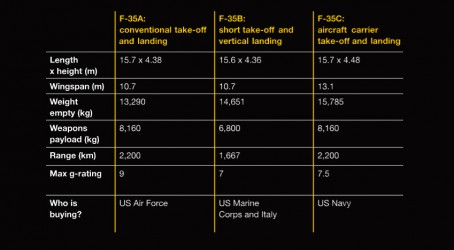