Articles
Braking and chassis systems specialist BWI Group has developed a range of lightweight smart passive dampers for B, C and D-segment vehicles.
The units are claimed to improve cars’ handling without affecting ride comfort and without the need for more expensive, heavier adaptive dampers.
Efforts to reduce vehicle weights and CO2 emissions are encouraging vehicle dynamics experts to find new ways to maintain the appropriate ratio between sprung and unsprung mass. Reducing the sprung mass without optimising the unsprung weight can compromise a car’s handling. The market’s shift towards smaller premium cars is also making it important to find ways of improving ride and handling more cost-effectively.
BWI said it had been able to reduce typical damper weight from 4kg to 3kg by using structural plastics instead of metal brackets and spring seats, varying the wall thickness of the damper tube, and by using hollow piston rods. A saving of 4kg is possible on a typical C-segment car equipped with front and rear McPherson strut suspension, said the firm.
The addition of smarter valve designs also allows the dampers to deal more effectively with different road conditions, such as pot-holes and speed-bumps and better protect the vehicle structure from large impacts.
Frank Robinson, BWI group’s product line director for suspensions, said: “The passive dampers are lighter than current units, providing reductions in unsprung mass that improve control, especially during bumps and wheel events. Our work on valve design has also extended the range of passive dampers’ performance, providing more of the functions associated with adaptive dampers at lower cost and weight. As a result the compromises are fewer: the driver has more control while passengers enjoy greater comfort.”
The smarter valves in BWI’s dampers produce damping curves that allow the suspension to react differently to inputs of different amplitudes and speeds. On harsh terrain, the valves also help reduce the shocks transmitted to rubber mounts and limit-stops that could otherwise be damaged.
Varying the thickness of the damper tube can save 0.25kg per corner by removing unnecessary material. Near the suspension knuckle, a damper tube’s wall thickness needs to be up to 3mm to carry bending loads. Higher up, 1.6-1.8mm is sufficient for closure, spring seat attachment and welding.
“BWI is committed to providing weight reductions and improved ride and handling without adding cost,” says BWI Group damper module engineering manager Slawomir Dzierzek. “This approach can be lighter and more cost-effective than using aluminium tubes and, when the damper forms part of a suspension strut, there is further scope for mass optimisation.”
BWI’s materials experts are targeting further reductions. The company reports that it is able to produce hollow piston rods with diameters as small 14mm. Modern high strength steels are also considered for structural components.
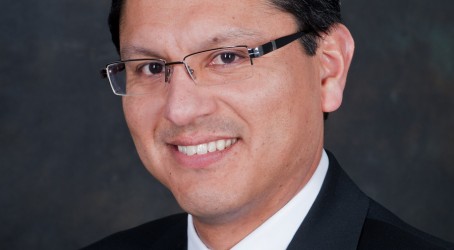