Institution news
Like any engineer stuck at home, Oliver engineered an unnecessarily complicated solution to a problem that didn’t really exist, however, for Oliver, it has been fun and rewarding.
Oliver is a calibration engineer at Ford Motor Company where he currently specialises in on-board diagnostics. Though not a stranger to electronics in cars, he has never created his own electronic car accessory, until now. The interior of the car had no phone holder and the visible wires and vent supported contraptions were not good enough. So he set out to create a phone holder which blended into the dashboard and charged his phone.
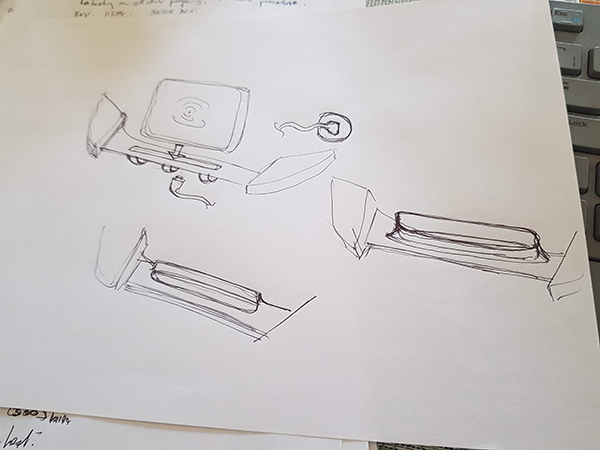
Like many DIY enthusiasts, Oliver turned to 3D printing for ease of use and low cost. After installing a free online CAD package and a few hours of online video tutorials, he was ready to go, or so he thought. It quickly became apparent that there was no datum to start from,
“Surprisingly, the most difficult part was recreating the dashboard matting surface accurately, in three dimensions”.
At work, engineers are supplied with engineering drawings or at least a datum point to start from, not in this case. Having dissected the interface shape into circles and triangles, using a set square, a protractor and a profile gauge the CAD could begin. With the datum points identified, the first prototype was designed and printed. Oliver’s brother Ben, an electrical engineer at Brunel University, gave him plenty of guidance on printing tolerances, the limits of printable profiles and expected shrinkage. By the second print the part fitted like a glove; now just the electronics to go. As with most projects, a quick browse led to some irresistibly low-priced parts from China, and three weeks later it was done.
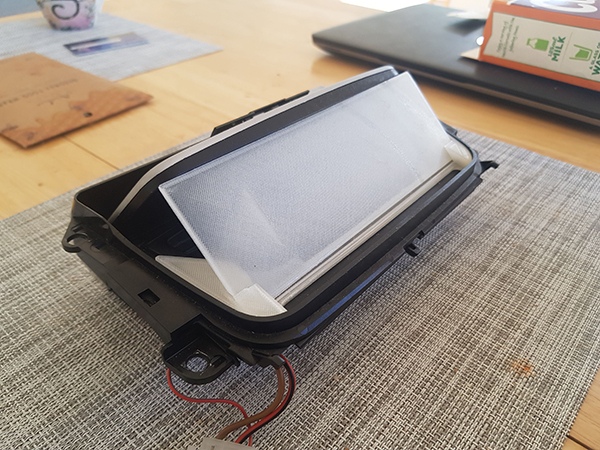
When the time came to print the second prototype, the cartridge happened to be a clear material, the final piece will colour match the dashboard, however, the clear plastic does have the added benefit of showing off the wireless charging coils for this review, a fortunate coincidence.
The product has now been tested in-vehicle and worked perfectly. Unfortunately, the part did not survive ‘hot testing’. It turns out 3D printing materials have a low softening point, “who’d have thought”?! With a few more support struts, Oliver is confident the next print will be just right.
The next step involves analysing the electronics to see if he can repackage them into a compatible shape, blending seamlessly into the back of the unit. “The project has been a welcome distraction from being stuck at home, it was short enough to be satisfying and long enough to be rewarding”.
Oliver’s other ‘current’ projects include motorbikes and cars. Oliver is looking into converting his classic mini into a electric car, but there’s a lot of research to be done, probably more research than the lock down period will allow for.