If at first you don’t succeed, try, try again. That is the motto of Bladon Jets, the Coventry-based micro gas turbine specialist bidding to plough a new furrow for fast-revving turbines in vehicles and power-generation applications worldwide.
Told in the 1980s by none other than Rolls-Royce that micro axial-flow gas turbines “could not be done,” Chris and Paul Bladon – twins well-known for their racing motorcycle engineering skills – set about proving the elite aeroengine maker wrong.
Paul Bladon, before his sad death in 2008, pioneered the machining of minute axial-flow compressor blade discs – blisks – from solid material using electro-discharge machines (EDMs). He took two months to produce his first blisk; now, with the latest machine, parts come at several an hour.
Bladon Jets has come far since its formation in 2007. Now the worldwide application of micro gas turbine technology looks to be within its grasp, both as automotive range extenders and for electrical power-generation sets (gensets) of up to 100kW – and possibly even larger.
It was in the 1960s that gas turbines first powered cars and trucks. The Achilles heel was poor heat exchangers and adverse fuel economy. Now, in range-extender mode, a micro gas turbine need run for only a short time at constant speed to keep an electric vehicle’s battery charged.
Paul Barrett, Bladon’s chairman, admits that serendipity played a part in the company’s evolution. He says: “Rolls-Royce challenged the Bladon brothers, who were very stubborn. Rolls-Royce said they would not be able to do it. The brothers went out and did it – using EDM to create the complex aerofoil blade shapes. We filed patents on the process in 2002.
“When we set out to commercialise the technology, our primary interest was aeroengines. But we moved our focus to the automotive area, where we perceived more immediate opportunities. We were approached by Jaguar Land Rover (JLR) which was interested in the weight-saving potential of a gas turbine range extender for electric vehicles.
“JLR tracked us down through our principal engineer Phill Heward, who had joined us a few months earlier. Phill is the world’s most prolific micro gas turbine designer,” says Barrett.
A collaborative project with JLR, part-funded by the Technology Strategy Board (TSB), led to the two 70kW micro gas turbine engines that featured in Jaguar’s C-X75 concept electric sports car. Using Bladon Jets’ ultra-lightweight range-extender technology, C-X75 has a top speed over 200mph and a range of 540 miles on a 60-litre tank of fuel.
Bladon’s technology muscle was further enhanced with the arrival of three senior advisers. Professor Philip Ruffles CBE, former technical director of Rolls-Royce, and Professor John Denton, former director of Cambridge University’s Whittle labs, have recently been joined by Professor Geoff Kirk, former chief design engineer at Rolls-Royce. Additional expertise is provided by partner PCA Engineering of Lincoln, specialist in aerodynamic design and CFD work. Barrett says: “PCA creates the complex aerodynamic shapes that we reproduce using our patented EDM process. Additionally, we have Leuven Air Bearings of Belgium. It develops advanced air bearings, crucial for high-speed rotating machines such as our micro turbines, which run at up to 250,000rpm.”
But it is the support provided by India’s Tata Group that may prove crucial in enabling Bladon to succeed where many others have failed. Chairman Ratan Tata is a firm believer in gas turbines. He not only sees where the automotive market is heading, but believes that micro gas turbines will play a big part in addressing the power-generation needs of emerging economies.
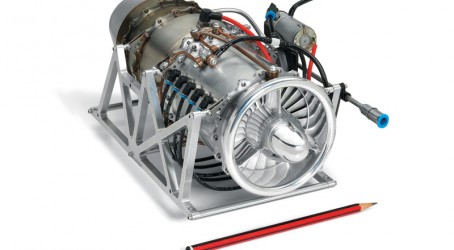
“Tata is a fantastic investor,” enthuses Barrett. “Besides financial support, it gives us access to a wealth of expertise. Tata shares our vision of building the world’s leading micro gas turbine business. The field is wide open.”
Bladon Jets’ design is for a simple reverse-flow gas turbine of tiny proportions – 90mm is the inlet diameter for Jaguar’s 70kW machine with an entry hub/tip ratio of 0.5. Overall thermal efficiency is 25% – achieved through high pressure ratios instead of the heavy (and expensive) recuperators found on most micro gas turbines. A multi-stage axial-flow compressor is followed by a single-stage radial compressor feeding air into the reverse-flow combustion chamber. The compressors share the same 90,000rpm shaft as a two-stage axial-flow turbine. A third axial-flow, “free” turbine drives the generator at 60,000rpm.
“Shaft length is critical for rotor dynamics,” explains Barrett, “especially as we use air bearings, which have little inherent damping. Hence our choice of reverse flow; it allows us to move the combustion chamber out in order not to take up space on the shaft.”
The absence of a recuperator has kept the overall design compact and light: the target weight for the 70kW unit, including the generator, is less than 30kg. Turbine inlet temperature is close to 1,000°C. Turbines and combustors are made from high-temperature nickel alloys, but there could be a move to ceramics – and higher temperatures – in future.
The vision is for even smaller engines, down to 6kW or less for some applications. Here the miniaturisation will be pushed further using rotor dynamics, aerodynamics and thermodynamics. The gensets will require recuperators to enhance fuel economy; the constant-speed range-extender turbines are unrecuperated for simplicity, reliability and low weight.
“The high power density of the gas turbine means we could fit a 6kW genset into a biscuit tin,”
says Barrett.
“And, with air bearings, air cooling and clean combustion, it would not require the bulky oil, water and exhaust treatment systems of conventional internal combustion engines. Gas turbines are multi-fuel – liquid or gas. And, with just one or two rotating parts, they are quieter and more reliable than their reciprocating counterparts. They are the ultimate combustion engine.”
Bladon plans to build a complete range of engines. “We will have 6, 12, 20, 35 and 100kW machines in time,” says Barrett.
“We already have two customers for our first engine. However, I am not convinced that 50kW is the right size for the high-volume automotive market. The sweet spot for Jaguar and other high-end manufacturers might be in that range, but for a small electric vehicle the range extender may need to be only 5-10kW. So we are working on a smaller engine.”
Had it not been for the Bladon brothers’ pioneering EDM work, Bladon Jets would not have existed. Now, thanks to the latest, £160,000, fully-automated Sodick AQ325L EDM machine, it can produce micro turbine compressor and turbine blisks in less than an hour.
“EDM is viable for volumes of 100,000 a year,” says Barrett. “We have developed the process for aluminium, titanium and nickel alloys and, using the latest CNC capabilities and our proprietary tooling, we can make multiple blisks in parallel.
“The number of blisks from one machine depends on blisk size, surface finish and component complexity. We can make five, 10 or even 20 in one pass. The process depends on the amount of material removed – very little with such tiny blades.
“For smaller engines, ceramics are viable using clever design and production techniques,” he says. “They can be used for both static and rotating parts in the hot end.”
Bladon has secured funding for a second TSB programme with Warwick Manufacturing Group (WMG), which has strong links with Tata and Jaguar. This is to develop gas turbine range-extender validation programmes. Bladon has to prove its designs are robust enough for automotive use.
“WMG was keen to work with us,” says Barrett. “No one has developed validation standards for automotive gas turbines – or for range extenders.”
Barrett says: “The biggest challenge for us is people’s expectation. Our profile is ahead of our capability at present. Six months ago we were in a cowshed in Shropshire. Now we have a custom facility in Coventry, but we are still two years away from production.
“Technology is the second challenge,” he adds. “Gas turbines may be simple in concept, but there is much to learn to make them perform reliably. The knowledge is out there in respect of larger gas turbines and we have to apply that to micro engines. The third challenge is growing the business. We have 17 people but we require more engineers. It is difficult to find anyone with micro gas turbine experience.
“We are serious about making this succeed,” concludes Barrett. “We have an incredible opportunity. We are extremely fortunate to have two major partners in Tata and Jaguar. And we have guidance from our Rolls-Royce advisers.
“Our aim is to produce tens of thousands of micro gas turbines for the Indian power-generation market and so reduce the unit cost to compete with conventional engines in automotive applications.
“Our small genset is being designed for mass-production,” declares Barrett. “It is not rocket science, but we are applying automotive production techniques where previous product runs have typically been measured in the hundreds.”