Decommissioning of the Brent oilfield will be a job of equal stature to finding it and getting it to produce oil in the first place, experts say. The field, which was discovered off the north-east coast of Scotland in 1971, was up and running relatively quickly: within five years.
And then it was prolific. Since 1976, Brent has produced a total of about four billion barrels of oil equivalent – almost 10% of the oil and gas so far produced from the North Sea. Production peaked at 504,000 barrels of oil a day in 1982, according to operator Shell. But the field, located in the East Shetland Basin, 186km north-east of Lerwick, has now reached the stage where production is no longer economically viable.
Decommissioning of the Brent field will be conducted over the coming decade. For Shell this means two things: figuring out how to decommission four oil platforms, 140 wells and 28 pipelines in an environmentally, economically and socially responsible manner, and then convincing the government its plans stack up.
Shell started to look at decommissioning the field in 2007. The oil company has had to engage in a stakeholder engagement programme to understand what the concerns of interested parties are, and must satisfy regulators, and the European Oslo-Paris Convention (Ospar), that its plans are sound. Ospar is the legal instrument guiding international cooperation on the protection of the marine environment of the north-east Atlantic. A final decommissioning scheme must also gain ministerial sign-off.
Duncan Manning, who is leading the decommissioning of the Brent field for Shell, says: “The whole process takes time. We need to understand what we are doing – and why we are doing it. We have weighed up the dilemmas of the project and made sure we are doing the right thing. We have been engaging stakeholders in the UK but also in Europe more widely.”
He claims: “There is a deep understanding of what we plan to do and why we plan to do it, and the science which underpins the recommendations we are making.”
The four Shell platforms on Brent are known as Brent, Alpha, Charlie and Delta. Brent Alpha is a standard field jacket design but, unusually, the others are gravity-based structures and have concrete bases. There is more experience of decommissioning the field jacket design of Alpha, although there has been some experience of decommissioning gravity-based structures in the Norwegian sector of the North Sea, says Manning.

Dismantling the platforms has to take place just as the many wells are plugged and made safe, to isolate the reservoir from the surface. Pipelines and subsea locations also need to be encapsulated in one overall decommissioning scheme. “We have to think long and hard about decommissioning to make sure we do it both safely and responsibly and meet the requirements of the regulator,” says Manning.
Since 2007 stakeholders in more than 180 organisations have been engaged. The science underpinning Shell's decommissioning proposals for Brent is also being reviewed by an independent body of nine scientists.
Central to the issue of decommissioning is the cost – and the question of who is responsible for the asset. According to the Ospar convention, ultimate responsibility remains with the owner. A report by the Royal Academy of Engineering, released last year, says: “The persons who own an installation or pipeline at the time of its decommissioning will normally remain the owners of any residues: that is, any remaining abandoned facilities, fluids or pollutants. Any residual liability remains the owner’s in perpetuity.”
The academy points out that ownership of assets may transfer during the life of a field. Transfer of ownership is a strategic decision that typically occurs between 10 and 20 years, when income from production is reducing and the risk profile begins to increase. When an installation is sold, the liability may or may not transfer to the new owner, depending on the commercial arrangement.
Although in most cases liability does transfer to the new owner, there are limited cases of it remaining with the seller. Should a new owner default, liability then transfers back to the original licence holder. A dictum of ‘if you put it there, you take it away’ then comes into force.
The academy notes that: “Exact decommissioning costs are notoriously difficult to calculate, as there are many unknowns and fluctuations such as estimated risks, material change in condition, market volatility, industry experience, loss of key personnel, supply-chain inflation, technical data and information management systems.”
Nonetheless, it is expected that a burgeoning North Sea oil and gas decommissioning industry will provide a lot of work for engineering firms. Manning says the industry is only “10-15% down the road of decommissioning”: there are 470 offshore installations still to be taken down, more than 5,000 wells still to be plugged and made safe, and 10,000km of pipeline to be decommissioned. He says this new industry is worth £35 billion.
“Parts of the UK are slightly ahead of the rest of the world in conducting decommissioning and sit under a very robust regulatory regime, and therefore the skills and experience that we are developing in the North Sea provide a real export opportunity,” he says.
“We can use the North Sea as a springboard to export worldwide.”
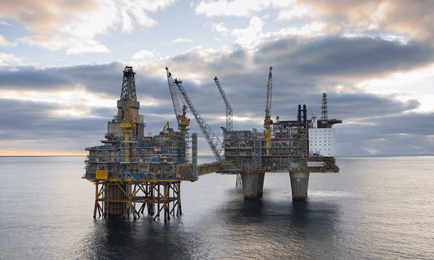
Manning says 80% of the contracts for decommissioning of Brent have been placed with British companies by Shell. This includes a contract with Able UK, which specialises in recycling end-of-life vessels and marine structures. The work to recycle material from Brent will take place at Able's Teesside Environmental Reclamation and Recycling Centre in Hartlepool, which has the distinction of being the only facility outside the US certified by the US Department of Transportation Maritime Administration for the decommissioning of redundant assets.
The Hartlepool centre has been the location of all Able's previous oil and gas platform decommissioning work, which has seen the dismantling of 15 offshore platforms. According to Able, the total percentage of reuse and recycling from these platforms is approximately 98%.
The challenges involved in decommissioning the North Sea's relics of the oil and gas boom are considerable. There's the size and scale of some of the rigs themselves, comparable in height to the Eiffel Tower, and hulking over the sea in some inhospitable territory. Manning says: “It is not a case of starting with a blank piece of paper and designing your programme: you're starting with a platform that has been in operation for more than 35 years and has some very prolific wells, that produced some tremendous amounts of oil and gas over their lifetime.
“So that requires some forward-thinking engineering, and coming up with bespoke technology to overcome the challenge. And it's a long project. We still have at least 10 years to go. Part of the challenge has been the location, which is a hostile environment for a certain number of months in the year.”
The Brent Charlie platform is still producing oil and will continue to do so for as long as possible. “We don't want to decommission early,” Manning explains. “Platforms will produce for as long as possible.”
From an engineering perspective, a single lift of the Brent Delta platform, at more than 23,000 tonnes, will be a challenge. The new single-lift vessel designed to do this is likely to capture the imagination of the public when it is launched, he adds. This would be a welcome development. Manning concedes that “decommissioning isn't necessarily a topic that people automatically gravitate to. But if you explain the dilemmas of what we're doing, and the engineering challenges of what we overcome, then people become increasingly interested in the project – and more invigorated by it.” It will be crucial that engineering skills are available in the supply chain to serve the new decommissioning industry and these should not just be in existing oil and gas contractors.
“It's important that any gaps in engineering support aren't just seen through the optic of oil and gas but the whole of the supply chain,” says Manning.

Diversity matters: The offshore industry needs to attract more female staff to plug the skills gaps
On the flipside of the industry, BP continues to explore for fresh oil and gas resources and begin production, with five major new finds exploited for the first time this year. But, just as for the nascent decommissioning sector, skills gaps are a problem, even for majors engaged in the sexier area of exploration and development of oil and gas resources, as a visit to the company's plush new training complex at its Sunbury-on-Thames HQ makes clear.
BP is working hard to prepare its staff for the demands of life in upstream oil and gas by investing more than $500 million in learning and development each year, which includes the newly built Upstream Learning Centre at Sunbury, intended to provide “flagship training” for employees around the world, using the latest technology, including lifesize oil and gas simulators, 3D visualisation of deeply buried geological layers, and HD video-conferencing suites for interaction with far-flung employees. Globally, BP has 20,000 upstream employees, of whom 12,000 are petrochemical professionals, scattered at many different sites and production facilities.
“What we are doing in resourcing is to try and understand where the key capability gaps are, and understand the critical need for key skills,” says Ann Perrins, vice-president of upstream human resources. “For example, diversity is incredibly important to us and we are always looking at it from that perspective. We need to build up talent.”
BP drills many deepwater wells. So the drilling simulator is useful for preparing upstream operatives for live drilling in the field. This includes how to deal with emergencies, explains Professor Phil Hassard, drilling simulator manager at BP's Global Wells Institute in Aberdeen. “We bring our teams in to face six of the most harrowing scenarios they might see in their careers – although we hope they never face them.” These teams include drillers from leading contractors such as Transocean and Maersk.
Operatives are recorded so they can see how they have dealt with whatever the simulator throws at them. “We can unleash Armageddon,” grins Hassard. These scenarios range from multiple failures of equipment to deterioration of conditions on the surface, down to nozzles coming off or bits getting stuck in the drill pipe. “In the worst-case scenario we may disconnect the blowout preventer and let it float away with the rig. It is an emergency disconnect – and very expensive.”
According to Perrins, the “whole industry is looking at how you can use technology to accelerate capability”. She adds: “Globally, there is a shortage of Stem students. We need to make sure we do our bit to develop them. This facility is one part of our philosophy of what we are going to do to build talent.
“Simulation has been used in aviation for a long time, and can now be used to simulate drilling for oil.”