Articles
The workshops and production halls of Tata Motor’s plant on the outskirts of Pune, Maharashtra, sprawl over its 29,000 acre site like an Indian city. The plant is typically Indian – it has lots of people, 20,000, and lot of space.
However, once through the factory’s main gate, differences with the world outside soon become apparent. Unlike the chaotic streets of most urban India, the Tata Motors’ plant is a well-organised oasis of calm. There are dozens of large workshops, production buildings and offices situated on a grid system of roads. There are street cleaners sweeping, everything is tidy – a stark contrast to seemingly every other city street in India.
The Pune plant is Tata Motors’ second largest factory in India. It was the Tata Group’s, the parent conglomerate of the Motors business, first car manufacturing site. It remains the company’s foremost car development and production facility.
During its first year of operation in 1977 the plant produced 430 light commercial vehicles. During 2012, it produced 256,000 - from cars and trucks to diggers and army vehicles. The factory operates up to three shifts, 24 hours a day. It has its own school which trains people for 4 years before the main factory accepts them as apprentices. It has India's only crash test facility certified to international standards. Around 90% of time in the crash testing facility is spent on engineering development, the other 10% on certification. Other engineering facilities include an environmental testing facility, which can heat cars to temperatures up to 55 degrees C and down to -40 degrees C, and an anechoic chamber.
Inside, the shop floors and engineering facilities are just as tidy, clean and well-organised as the access roads outside. Although the site is large, it is the diverse range of vehicles produced there that impresses the most. By European standards the plant is very self-sufficient. A high percentage of a typical Pune-manufactured vehicle is produced on site from scratch. Indeed, a large amount of the plant itself is produced on site, by a production engineering shop that makes the jigs and toolsets for the manufacturing lines. Only some of the vehicle electronics, mainly the dashboard components, are externally supplied.

Engineering implications arise as a consequence of sourcing less parts and components from external suppliers. Dr Tim Leverton, head of advanced and product engineering for Tata Motors, says: “The full suite of suppliers that you would expect are here, but if you look over the last twenty years, even today, the amount of engineering responsibility we have to take is much more than compared to Europe.”
One of the tasks in recent times has been to improve the competency and standards of local suppliers, so that internal engineering resources can be deployed in a more effective way, says Leverton. The aim is to build expertise, so the company’s engineers can focus more on developing future technology instead of designing windscreen wipers and locks.
Alongside such changes in R&D, management has been pushing to improve manufacturing and quality standards. The plant at Pune produces a wide range of vehicles – from mine resistant troop carriers for the Indian army to dump trucks, buses and the Nano, Tata Motor’s diminutive and famous “cheapest car in the world”. With such a diverse range of vehicles and large volumes, ensuring quality and improving efficiency is a challenge. Recent management initiatives and the introduction of new equipment, particularly automation technology in safety and quality, have resulted in improvements, says Girish Wagh, vice president of programme planning and project management at Tata Motors.
Wagh says: “It’s a difficult task to ensure quality. We have founded the Tata Motors Production System across all the plants and products. The knowledge about good practices and benchmarks and metrics has gone into the system and is applied to all vehicles.
“We now plan to bring in more flexible manufacturing systems. Our current production capacity is not full. So the focus is to develop that over the next few years.”

Manufacturing and engineering improvements are being driven by a desire to transform Tata Motors into a global player in the automotive market. According to the company it is the largest manufacturer in the Indian automotive industry and the fourth largest bus and truck manufacturer in the world. But the reliance on the Indian market leaves the company vulnerable to its ups and downs. Although large, the Indian automotive market is as prone to ups and downs as markets everywhere. Indeed, the sector has been going through a downturn recently. According to international trade body the Organisation of Motor Vehicle Manufacturers, some 3.5 million passenger and commercial vehicles were sold in India during 2012. That figure dropped by more than 10% in the first half of 2013, from 1.9 million to 1.7 million.
The drop in demand has been felt particularly keenly by Tata Motors because its core domestic market of large commercial vehicles saw the sharpest reduction. Karl Slym, managing director of Tata Motors says that the company cannot expect to retain its 65% market share in the Indian market in coming years and that this is driving globalisation plans. “We can expect to be a major shareholder, but we can also expect pressures and further economic downturns. The overall industry is flat,” he says.
The company plans to expand first in emerging markets outside of India such as Southeast Asia, Eastern Europe and South Africa during the next six years, territories where the company already has a strong presence. The plans to launch vehicles in Europe are longer term, "when we have developed some newer platforms", Slym says.
There are no plans to launch in the US. "While we have been an exporter for almost 16 years, volume-wise it’s led by domestic demand. Most of our experience is in the Indian market,” Slym says. “To be a global player we recognise we need to meet the expectations of global customers as well as our Indian customers in terms of the quality of our product.”
Strangely, the yardstick for Tata Motors’ international success comes from within. The Tata Group bought Jaguar Land Rover (JLR) in 2008 and since then then the company has enjoyed stellar and somewhat unexpected global success. JLR produced 358,000 cars in 2012. Some 85% of its revenues that year were generated from exports, primarily to China.
Slym stresses that its sister company JLR is treated as a completely separate business unit within the Group, in India and globally. However, this hasn’t stopped engineering crossover between JLR and Tata Motors’ vehicle development.
Dr Leverton from Tata Motors says: "There are systems and components technologies where we share R&D focus and engineering standards. We’ve benefited from that since the relationship with JLR started.
"We’ve had a lot of exchange in the development process, procedures and testing, engineering standards and design rules. Over the last few years our product development process has evolved to be very close to the sort of process that is followed in JLR, which is a prerequisite to working together in the future.”
Leverton says that the European market and automotive technology is around five years ahead of what is required in the Indian market in terms of CO2 emission reduction, mainly because of poor fuel quality and costs. There is also considerable difference in pricing between JLR’s premium vehicles and Tata Motors’ mainstream vehicles, which sell at under £2000 to around £12,000. This means that although similar overlapping technology areas, such as in engines, are seeing a lot of collaboration, there are big differences in how these technologies will manifest in the vehicle.
“For the two litre engine level and below, our 1.2 litre engine and above requirements are starting to come into overlapping areas,” says Leverton. “Many of the technologies and solutions needed for those are similar. What’s different is the positioning of those products in terms of power density demand versus economy or versus vehicle application. But in 15, 20 years there won’t be much difference at all. In manufacturing terms, for cost competitiveness everything has to be localised.
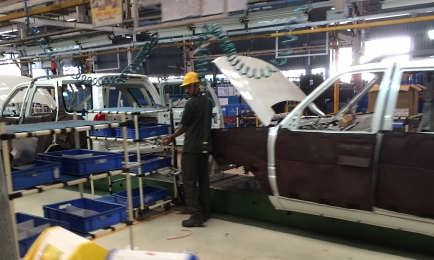
A global automotive company needs global R&D facilities and Tata Motors has been expanding its R&D presence in Europe and outside of India in Asia. The company has a European Technical Centre at Warwick University in the UK and a design studio in Turin. Nick Fell, head of Tata Motors’ European Technical Centre, says: "The R&D portfolio is overseen in the UK, some of which is executed in India. It tends to be early stage work rather than industrialisation for final product. We very much act as an integrated part of the development capacity.
Fell says there is a “common imperative” of CO2 reduction and fuel efficiency improvements across both Tata Motors and JLR products and that this has led to a pooling of capabilities in areas such as alternative fuels, base engine improvements and lightweighting. Tata Motors is building expertise particularly in in high voltage electrics, energy storage technologies, control systems, traction motors to open up a range of hybridisation options between pure battery and stop-start.
Fell says: “It’s clear we are going to move from the single solution of the internal combustion engine to multiple solutions. We can align our plan to protect for the way in which the mix of fuel solutions might change in the future.”
“We have to ensure we proceed on a multi-strand basis where we can improve the fuel efficiency and CO2 emissions of our conventional vehicles but also ensure we have alternative fuels as well. To lock yourself into a single solution is very risky. You have to be very agile and adjust to what that mix becomes. Then we can compete in our domestic market with its aggressive cost base and have products that can be competitive for when we build up in Europe.”
A JLR plant in the UK such as Halewood and a Tata Motors plant such as Pune in India are a world apart. But the freshly shared parentage of the two companies means that the manufacturing and engineering expertise that Tata Motors requires to secure its position on the world automotive stage is readily accessible. After all, there always seems that there is room to expand in India.