The excavations were chilly in mid-March with our six-month winter yet to end, and the news soon to come that skeletons from the Black Death were next to be uncovered by Crossrail employees only served to highlight the murky nature of plumbing London’s subterranean depths.
Rapid progress was being made at Bond Street, where work was advancing on two new ticket halls, east and west, that will serve the railway line come 2018. And engineers were able to celebrate the arrival of a gigantic tunnel boring machine known as TBM 1, or Phyllis, at the halfway point of her journey from Royal Oak to Farringdon station.
Anyone who commutes regularly in London can attest to the attractiveness of Crossrail, which will add a much-needed 10% to the capital’s rail capacity. The project, versions of which can be traced back as far as 1941, nearly didn’t make it to the approval phase but was finally granted royal assent in 2008. Billed as Europe’s largest construction project, it will not come cheap, at £14.8 billion, but will link Maidenhead and Heathrow in the west to Shenfield and Abbey Wood in the east through 21km of twin tunnels under the city.
It’s these tunnels that require the labours of TBMs like Phyllis and her colleagues Ada, Elizabeth and Victoria. Two special slurry TBMs are also being used to construct the 2.6km section of the network that goes under the Thames. A further two machines will dig the Pudding Mill Lane to Stepney tunnel.
Engineers have to contend with the fact that London is a city built on networks of tunnels. This means avoiding gas, water and electricity supplies and also the systems that make up the Underground. Steve Parker, Crossrail construction manager, says of the work at Bond Street: “You can imagine Oxford Street is littered with tunnels – that has been the case over the last 100 years. If you took a borehole down at Oxford Circus, you have the Bakerloo line, the Victoria line, the Piccadilly and Central Tube lines, and then there’s the Thames Water main, power tunnels and the old Post Office cable tunnels.”
The challenge is to bore in the attractive tunnelling medium of London clay while avoiding this criss-crossing network of older tunnels and yet not starting works too deep – because this would entail building excessively long escalators.
“Very deep tunnels are uneconomic,” says Parker. “But by looking at the history of these tunnels, we know the ground is competent – between Bond Street and Holborn we expect good clay. There should be no changes in the geology.” This means that the western TBMs should not encounter stiffer resistance than hitherto experienced as they make their way through the clay, boring the west and eastbound tunnels for one section of the line.
Parker says: “We have a lot of monitoring of TBM torque and shot pressures. If we start to notice that the TBM’s driving parameters and the torque starts to rise unexpectedly, then either we’ve got something stuck to the head or we’ve encountered something and are getting wear.
“On this drive I don’t think this is going to happen: but if things got tougher then that indicates that something’s not right and we go for a look.” Measures taken to smooth the progress of each machine include injecting foam and polymers into the head.
It is also necessary to carefully plan maintenance of the tunnelling surfaces of the machines. When Phyllis reached Bond Street, a chamber was constructed to allow her usually inaccessible cutter-head face to be inspected by technicians. The chamber was filled with light, airy foam concrete which provides a tunnelling surface for the machine, and an access path was left behind so engineers could look at the wear and tear on Phyllis’s head.
Parker explains: “We can check the tools from the back of the machine, but you have to enter the head and go through an airlock: it can be done but it’s messier and harder. The foam concrete is rather like the Thermalite blocks you get in your house. It’s light and airy but will support the machine, and we have an access way that a person can walk down. We can then look at the cutting head in a safe way, and make any necessary repairs.
“Thus far, in this clay, the wear that we’ve been getting is low. Clay is an ideal tunnelling medium and we’re driving the machine, injecting foam into the head, and it’s reducing the wear and reducing the torque.”
Tunnelling under the Thames presents more of a challenge, and a different type of TBM known as a slurry machine is used. “There is a combination of chalk and water which becomes rather like toothpaste when it is bored into, and it is removed in a slurry from the machine,” says Parker. He emphasises that the sophistication of the Crossrail TBMs, which are supplied by German firm Herrenknecht, is principally in the way in which they communicate information.
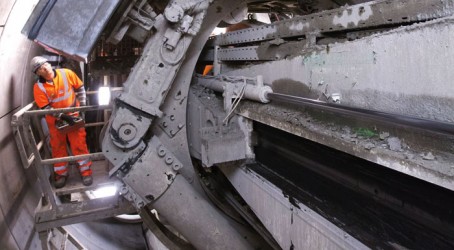
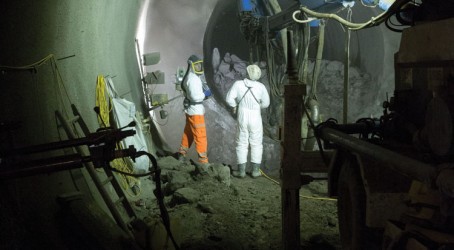
“The TBM is a big beast of a machine but, in terms of its sophistication, the mechanical bit has not changed that much in the last 20 years,” he says. “What has happened is that the telemetry on these machines nowadays is far more sophisticated so we have a lot more realtime data. We can examine that data, trends and parameters, and with web-based applications I have the ability to sit at home with my iPad and see in real time what the TBM is doing – and whether it’s being driven correctly.”
The six TBMs that are being used to dig the non-Thames sections of Crossrail’s twin-bore tunnels are known as earth pressure balance machines (EPBs). These differ from the open-face machines that Parker managed when he was involved in the construction of the Jubilee Underground line extension. “Open-face machines are simpler – you can see the ground,” he says. “We’re using EPBs on Crossrail, which give you the ability to close off the face and provide what we call positive pressure. What that helps to do is reduce settlement.
“The art of the tunneller, if you like, is to tunnel in a controlled manner and maintain and excavate the correct quantity of material per metre going forward.”
The tunnels along which the trains will run are being built with concrete segments and rings of a standard diameter, matching their height. The construction method changes to sprayed concrete lining in the new stations, where the tunnels are significantly bigger.
Parker says: “If you can imagine, there will be escalators, concourses, and cross-passages connecting into existing stations. We’re surrounded by tunnels, every passageway is unique, and if you constructed in rings you’d need so many different types and sizes of bends and rings. Sprayed concrete lining lends itself to changing shapes more easily.”
Life on board a TBM involves an eight-hour shift for a team of about 20. Facilities include a welfare area, canteen and toilet. The machines are more than 140m long. Operators control the cutting head from a cabin 20m behind the front of the machine. The cutting surfaces are controlled by computer nowadays. Individual segments of concrete used to construct the tunnels weigh 3.2 tonnes and are placed using vacuum technology.
A grouter at the rear of the TBM copes with the imprint left by the machine, which needs to be filled and extends to about 5.5m3. “Every time we shove forward we inject over 5m3 of grout and allow the ground to settle, controlling it all the time,” says Parker.
Finding the space in London to construct a “portal” in which to build the machine and send it underground was in itself a challenge. “Crossrail is such a big project,” Parker explains. “Finding a site to build a big TBM machine, with a lot of material coming out, is not easy.
“Even our site here at Westbourne Park is very constrained. North of us there is the Westway and Grand Union Canal, and to the south there is London Underground’s Hammersmith and City line. We have a long sliver of land but at parts it’s only 50-60m wide. We’re operating two TBMs, so it’s a tight area. Planning and logistics are key to a successful – and safe – operation.”
To this day, Parker enjoys seeing tourists using the Jubilee line extension in the knowledge that he helped to build it. “With Crossrail we’re in the heart of London, so from my point of view this is a mega project,” he says.
“It’s exciting, and I’ve had 25 years in tunnelling and am surrounded by professional engineers. Some of these people I’ve been working with for 25 years: we follow the work and we bring a lot of experience to it.
“I’m passionate about what I do, and I do it safely and professionally. So of course I will be immensely proud when the first passengers start using Crossrail.
“And I think it will be of great benefit to Londoners.”
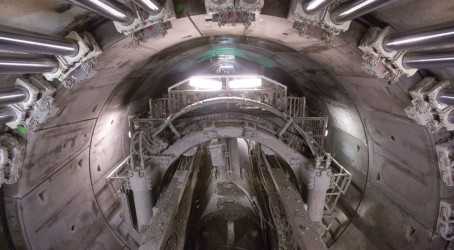
Crossrail services will start in 2018
Crossrail will bring an extra 1.5 million people within 45 minutes of London when services begin on the central section of the line in 2018. There will be 37 new Crossrail stations including new Underground stations at Bond Street, Tottenham Court Road, Farringdon, Liverpool Street, Whitechapel, Canary Wharf and Woolwich. A new surface station will also be built at Custom House.
Up to 24 trains an hour will operate in the central section between Paddington and Whitechapel during peak periods, with each train able to carry 1,500 passengers. An estimated 200 million people will travel on Crossrail each year. Passengers will be able to travel in 10-car trains from Heathrow airport to Tottenham Court Road in less than 30 minutes and from Paddington to Canary Wharf in 16 minutes. Abbey Wood passengers will see their commute into central London cut from about 50 minutes to 20 minutes.
As PE went to press, Crossrail engineers were celebrating lead tunnelling machine Phyllis passing through the new Bond Street station, having completed more than two miles of tunnel. Sister tunnelling machine Ada has also now completed more than 3km of tunnels. Both western tunnelling machines will finish their journey at Farringdon by the end of the year, said Crossrail.
Crossrail’s TBM Sophia has dug half a mile of tunnel from Plumstead, and will reach the Woolwich station box later this spring. Two huge eastern tunnelling machines, Elizabeth and Victoria, will break through into Canary Wharf station box shortly.