With the cost of university education soaring, many young people are considering apprenticeships as a route into engineering and manufacturing. Apprenticeship schemes at the biggest employers are often hugely popular. But many small and medium-sized businesses lack the resources to invest in apprenticeships. This is something the government wants to change.
Earlier this year the education and business secretaries commissioned entrepreneur Jason Holt to investigate what could be done to help small firms to take on more apprentices aged between 16 and 24. As a result of the review, the government has made changes to the Apprenticeship Grant for Employers. Businesses that have not taken on an apprentice for 12 months are now eligible for the grant, worth £1,500. Previously, a company was only eligible if it had not taken on a new apprentice within the past three years.
The rules on the number of apprentices that a firm can take on at once have now been relaxed. Companies can apply for the grant to support up to 10 apprentices at a time, up from three previously.
Businesses are now paid the grant in one lump sum instead of in two stages to help reduce the administrative costs. Until now, the grant has only been available for firms with fewer than 250 employees. The changes see access opened up to companies that employ up to 1,000 people.
Verity O’Keefe, skills adviser at manufacturers’ organisation the EEF, says that the changes are welcome: “It will give businesses a great opportunity that they wouldn’t have had before – £1,500 is a lot of money.” She says that often small manufacturing businesses do not access funding for apprenticeships because the process is too bureaucratic and complex, and instead dip into the company purse to cover the costs. So the changes may encourage a bit of additional take-up of the scheme.
However, a lot of non-financial issues remain, she adds. Many employers taking on apprentices in the 16-18 age group find that they lack the required literacy and numeracy skills. Raising those attainment levels through pre-apprenticeship training could be an option. Other hurdles facing businesses wanting to take on apprentices include the speed with which certain processes are completed. Companies posting an apprenticeship vacancy must wait for the advertisement to be checked and approved, and the firm vetted.
Employers must be inspected and visited by independent assessors to look into the work the apprentices would do. All this takes up valuable time.
The Holt Review recommends changes to certain processes, including that companies should be able to publish vacancies “pending approval” to speed things up.
According to O’Keefe, many companies considering taking on apprentices do not know that the funding is available. Although colleges and training providers promote the grant, more small and medium-sized businesses would access it if the scheme was better marketed by the National Apprenticeship Service (NAS).
O’Keefe says: “There has been a lot of confusion over the role of NAS in the past and I think we need to define its role. If that is going to be the organisation that promotes and markets apprenticeships, we need to make sure that it is a one-stop shop and we don’t see lots of other organisations crowding it out.”
She suggests that NAS should be organising seminars and events about apprenticeships for small businesses.
As a result of the Holt Review, NAS has pledged to “enhance” its marketing activity aimed at smaller businesses and will publish a guide outlining exactly what support is available for companies taking on apprentices.
Stephen Tetlow, chief executive of the Institution of Mechanical Engineers, says that the problems facing apprenticeships are wide-reaching. He is “really concerned” about the direction the country is taking on apprenticeships.
He says: “Only a very small proportion, 10% of apprentices, are going into engineering and by the government’s own figures it is those apprenticeships that provide real return on the investment for GDP. The rest of these very short-term apprenticeships are not going to provide the wealth creation that we really need.”
To rebalance the economy, the government needs to support the creation of high-quality, long-lasting apprenticeships. He adds: “We’ve got to be careful that the government are not just playing a numbers game.”
There are around 25,000 engineering apprenticeships each year. By contrast 200,000 engineers will leave the profession by 2020. These figures from the UK Commission for Employment and Skills are based on a projection of 0.5% economic growth, which seems unattainable given the economy’s current performance. Tetlow says: “If we have got any ambition as a country to have a properly balanced economy, with manufacturing going from say 12% to 20% of GDP, we need to be geared up in a much more coherent way.”
He suggests that the money available for apprenticeships is “spread too thinly” and more should be invested in the fields that will give the government the greatest returns at the cost of other industries. Tetlow earmarks infrastructure, manufacturing, and research and development as worthy sectors.
Engineering apprenticeships need to be given a higher profile than they hold at the moment, says Tetlow. Clearer delineation is needed to get rid of the notion that a three-month placement and a four-year high-level apprenticeship are the same thing.
He adds: “We want to see the support structure increased. We want to see it set in the context of an industrial policy that is going for growth and ties the key sectors for investment with producing the skills in colleges and companies to drive that growth.”
The Apprenticeship Grant for Employers is just one of the support mechanisms available for businesses looking to take on apprentices. Tetlow says that the current support mechanisms are “too complex”.
Many small and medium-sized businesses do not have training departments that can spend time getting to grips with the funding system and setting up relationships with colleges.
Better careers advice in schools would also help, adds Tetlow. A one-stop shop should be created that companies can use to get apprenticeship funding, education and training in one package.
But he concedes: “We are a long way from that.”
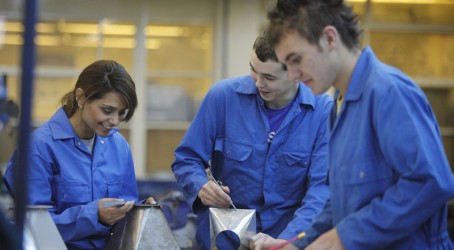
How much does an apprenticeship cost?
The Apprenticeship Grant for Employers offers £1,500 to contribute to the wage costs of taking on an apprentice. But how much does an apprenticeship in engineering cost to run?
According to a report from the Department for Business, Innovation and Skills, the cost of training a level-two and -three apprentice in engineering is £40,000. Verity O’Keefe, skills adviser at manufacturers’ organisation the EEF, says that its members spend £50,000 training each apprentice in manufacturing. By contrast, an apprenticeship in retail including an NVQ qualification costs £3,000 to run.
These training costs are met by the government if companies take on an apprentice aged between 16 and 18 years old. The government will also cover half the training costs of apprentices aged 19-24. But above this age, there is no formal provision to meet apprenticeship training costs.
The amount an apprentice earns varies between companies and sectors. The £1,500 contribution to wages offered by the government is based on a national minimum wage of £2.65 an hour. Usually, apprentices in the engineering and manufacturing sectors earn a lot more than this.
A recent pay benchmark survey by the EEF revealed that a technician apprentice in the manufacturing industry will earn an average of £9,000 in year one, rising to £11,000 in year two, £14,000 in year three, and £16,000 in year four.