Standing overlooking the production area at Control Techniques’ factory in mid-Wales, you see a very 21st-century manufacturing operation. The high degree of automation – with distinctive reels of electronic components feeding capacitors, chips and resistors on to high-speed precision machinery where they are fitted, soldered and quality-checked on printed circuit boards – of the factory in Newtown, Powys, seems fitting given that the end product for which these circuit boards are being made, the drive, is also destined to find use as a high-tech addition to demanding automation applications.
Drives are an essential element of modern manufacturing. The range of parameters that AC drives can be used to improve or control in industrial applications includes acceleration, flow, monitoring, pressure, speed, temperature, tension and torque.
They can also be used to control several specialised industrial processes. Drives can be either AC-AC, or AC-DC, and can prevent motors from being subjected to high starting torque and surges of current. AC drives are designed to gradually ramp the motor up to operating speed to lessen mechanical and electrical stress. This can reduce maintenance and repair costs, and extend the life of the motor and the driven equipment.
Variable speed drives – also known as variable frequency drives – can also run a motor in specialised patterns to further minimise the levels of mechanical and electrical stress.
Software development is critical to the development of the drive, says Mike Lomax, an engineer with Bosch Rexroth, part of the Bosch Group, which markets and maintains the devices in the UK.
He says: “Traditionally the drive, or the inverter, was a fairly dumb device. But eventually people started to put microprocessors in them, so now it’s limited only by your imagination: if you can write the software to do it, then you can do it with that drive.
“So, for instance, all our newest range of drives contain a complete IEC 61131 programmable logic controller (PLC). They contain a complete motion controller, and a complete set of technology functions for solving different automation applications.
“You need to recognise that in that little box you’re probably getting up to 50 or 60 technology functions that are solved by the drive.
“You want to make the automation process that you solve as easy as buying the drive and connecting it.”
The microprocessor used within a drive is “vastly more capable” than the ones found inside a typical desktop computer, says Lomax. As CPUs have grown more powerful, they have taken on more functionality in the consumer marketplace, and the same is true in industry.
“We’re taking motors and doing things with them that wouldn’t normally be possible – increasing their efficiency, increasing their smoothness of operation – with algorithms inside the microprocessor,” he says. “We’re implementing algorithms at the moment that decrease heating within the motor.”
Energy efficiency is a key technological driver, with the heat sink at the back of the drive becoming increasingly sophisticated as a result. Another important trend is interconnectivity and the increasing use of ethernet to remotely control drives.
Some of the algorithms used to make motors perform better are “mindblowing”, says Lomax. No motor turns perfectly, so ripples are created in the electric current. These can be smoothed out by the drive. Drives have to be very responsive to perform this task, continuously making realtime calculations within the processor.
Although Bosch Rexroth does manufacture drives for “quick and dirty” jobs, it specialises in providing high-end drives for very precise manufacturing operations. “The thing that differentiates our PLC from that of any other manufacturer is the libraries of knowledge that go along with the product,” says Paul Streatfield, industry sector manager at Bosch Rexroth.
“It doesn’t matter what the PLC is really; it’s that library of functionality we’ve developed over the years that makes the difference.”
Future generations of PLC will entail the development of further functionality in terms of software that can be used to solve different problems in automation.
Bosch supplies most of its drives with motors, so motor design is an important focus in terms of improving performance and efficiency. At Bosch Rexroth’s headquarters in Cirencester, Gloucestershire, a team of engineers at PhD level is responsible for finite element analysis of motor design. This includes not only the mechanics of the motors but also the magnetic fields they generate.
Lomax says: “In an effort to make the motor more efficient and lower-cost to make, we analyse the magnetic fields. Engineering is not just the best absolute possible: it’s the best absolute possible at an affordable price. And there are other constraints: you can’t use beryllium in certain components any more, because it’s carcinogenic.”
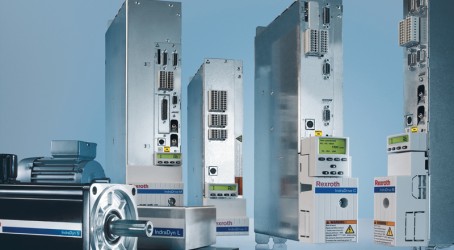
The market in the UK for drives is relatively good at the moment, says Streatfield. “It’s pretty healthy: you go home after work and listen to the news and it’s all doom and gloom, but we’re not seeing that. In 2011 and 2012 we had two of our best years ever. Our customers have full order books and are giving us loads of enquiries. We see it as a buoyant market. As we are a German company, they are more cautious than we are because of the eurozone, but in the UK we are optimistic for this year.
Government backing is helping, he says. “It’s an exciting time for engineering and manufacturing. If you thought about manufacturing five years ago you probably wouldn’t be recommending it at as a career: today, you probably would. The government has encouraged manufacturing in a number of ways. The creation of the Catapult centres is an example of that.”
Enrique Minarro Viseras, president of Control Techniques, says Wales remains an attractive location for the company to manufacture drives. The company is part of the US-owned Emerson Industrial Automation Group, but Control Techniques has three decades of history on the Newtown site. It now exports most of its drives.
“Most of the technical competencies started here; the whole business started here, helped by the government,” he says.
“The type of technology that we were doing with drives was new to the market – this way of manipulating power, to do more with motors and factory automation, didn’t really exist.”
Viseras makes an analogy between inventors such as Bill Gates starting up in a garage and the origins of Control Techniques. “They started from nowhere, and that has stayed since that time in the culture of the company.” Engineers tend to stay with Control Techniques for long periods, passing on their knowledge to subsequent generations.
Could the kind of manufacturing that Control Techniques does in Powys be done in the Far East? “I think there are certain areas that can be done in the Far East, and indeed we have two sites there that we already use,” says Viseras. “But there are a couple of areas that make manufacturing here relevant, and that will make it relevant for the foreseeable future.
“The first is that it makes financial sense to have manufacturing in the UK, and manufacturing in Wales in this case, because we can supply to the whole of the European and Middle Eastern markets from here in a much more cost-effective way. The other area is the customer value side, in terms of the flexibility required today, in terms of quick changes to plant to be able to deliver at the pace and time the market respects.”
So it is Powys’s proximity to the European market that is valuable? “I think most industrial technology companies have realised in the last few years that if you do not have a strong policy of regionalisation, you are dead,” says Viseras.
He adds that core competencies are required for high-tech manufacture of products such as drives. To do this to the requisite quality, and with a continuous evolution of manufacturing processes, requires the skills built up over the decades at Newtown, he says. “For these reasons we are very comfortable manufacturing in the UK and manufacturing in Wales. We are investing for the long term here.”
The UK is competitive in terms of cost with the other western European manufacturing nations, says Viseras. “You have to remember that, regardless of where we are in the world, in China salaries and wages for shopfloor people in the next five years are expected to grow at more than 20% a year. So it’s not only what you have today, but what might be expected to happen in the future in terms of cost.”
Using the Far East for the whole manufacturing process could also stifle innovation, he adds. “The more you are thinking that it is appropriate to build a product for the whole world in the Far East, the more your product is likely to become commoditised, rather than relying on innovation and adding value.”
Control Techniques has many customers in Germany, Italy and France. Asked if Britain should even be entertaining the notion of leaving the European Union, Viseras says this would cause problems in terms of both markets and employee skill levels. “We do probably 50% of our sales in Europe, so obviously we don’t want that to be damaged. If any changes in terms of the UK’s relationship with Europe are to take place, we don’t want to see barriers that would make it difficult to make those sales.
“We also use some highly skilled labour from the European pool: it would be a pity if we could no longer access that.”
Being part of the wider Emerson group brings advantages for the company in financial understanding, marketing expertise and focus on customers, says Viseras.
“The financial backing that we have is important,” he says, “Emerson traditionally doesn’t rely on external debt but makes investments through cash flow.” When funds are required for new product development or changes to plant or manufacturing processes, the group has the financial muscle to back Control Techniques’ plans, he says.
There are also advantages in being able to tap the expertise of sister companies in moving into new markets, for example.
Where would he like to see new markets opening up? Is there anywhere that’s strategically or territorially important? “Europe continues to be by far the largest manufacturing and automation market globally. When we look at the emerging regions, any global company these days wants to tap into the growth of China as it moves into more automated equipment. We need to be on that train,” he says.
“Outside that, we see a lot of potential in sub-Saharan Africa, particularly South Africa. And the Middle East and Latin America are important, although Latin America remains a complex market. And the US is doing well at the moment.”