Just a few years ago, using more than 50% composite to make the airframe for a wide-body jet would have seemed improbable. Yet this is the proportion being used in the new Airbus A350 XWB, with the opening of the final assembly line for the aircraft in Toulouse late last month representing a seminal moment in the development of composites for aerospace applications.
Airbus claims that the high composite content will deliver huge operator benefits: the A350’s carbon fibre-reinforced plastic fuselage will result in lower fuel burn than existing similar-sized aircraft, while maintenance will prove far easier.
The success of the A350 XWB is crucial to the future fortunes of Airbus. The aircraft will go head-to-head with the Boeing 787 Dreamliner which, after launch delays related to weight and parts supply problems, is being produced at two separate plants and continues to sell well. Boeing has now delivered 30 of its 787s and will increase final assembly production at Everett in Washington and North Charleston in South Carolina to a total of five aircraft per month by the end of 2013.
The programmes act as two high-profile showcases for Boeing and Airbus’s composites capabilities. The challenge for Airbus is to move towards a drumbeat of production in a smoother manner than Boeing managed. Indeed, slowly but surely, the A350 XWB is coming to life, with the first two aircraft – the static version and the first flyable model, MSN1 – at different stages of final assembly.
The static aircraft, which will be used solely for ground tests, has nearly completed assembly, with a full fuselage, two wings and the vertical tailplane joined. The aircraft will be transferred to the static test hangar in Toulouse, where tests will start next spring.
The first flyable A350 XWB (MSN1) is also progressing well, with the fuselage already joined. The wing and vertical and horizontal tailplane for MSN1 are inside the final assembly facility and will be joined to the fuselage this month.
It’s not just Airbus that will be hoping that the A350 XWB takes off – the programme is also an important one for the UK aerospace supply chain. The wings for the aircraft are made at Airbus’s Broughton plant in North Wales, while dozens of other systems, sub-assemblies and components are designed and built by engineering firms located across the UK. So there’s a lot riding on the success of this composite newcomer.
That’s particularly the case at GKN Aerospace, the tier-one supplier that bought the Filton manufacturing facility from Airbus several years ago. GKN has invested a total of £170 million at Filton, which will be the base for the manufacture of the aircraft’s rear wing spar and assembly of the fixed trailing edge.
In the production of the wing spar, GKN has developed an automated fibre-placement process that uses a robotic head to lay down 16 tows of material at a rate of 7-10kg of material an hour. The spars could not be made using traditional hand lay-up processes for two reasons: speed and consistency of quality. Hand lay-up is achieved at a rate of only around 1kg of material per hour – just one-eighth of the speed of the automated fibre-placement process – and cannot achieve the production consistency and fine tolerances required for the structure.
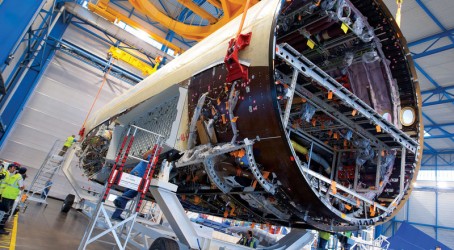
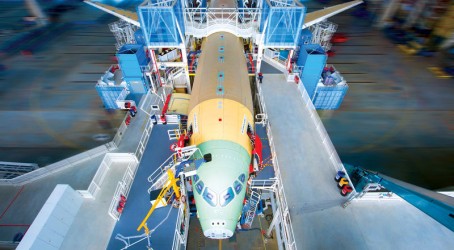
In the assembly of the fixed trailing edge, GKN has also created an innovative, fully automated “moving line” assembly process where automated guided vehicles move A350 XWB wing structures through dedicated workstations that carry out complex tasks including five-axis machining, robotic drilling and laser scanning. GKN then delivers the complete fixed trailing edge/rear spar to the Airbus facility at Broughton.
GKN is also manufacturing structures for the Trent XWB engine. The engine thrust struts are manufactured in high-temperature nickel alloy, with chemical milling used to create a lighter, stronger structure. The blisks will also be manufactured using chemical machining, to produce a component to fine tolerances and an excellent surface finish. Meanwhile, the inner core fairings incorporate proprietary all-welded titanium honeycomb technology, which gives excellent sound suppression along with a lighter, more durable and more easily repaired structure.
UK firms continue down the supply chain. PFW Aerospace, in Farnborough, is supplying fuel and bleed air tubing systems and PEEK polymer-based pipe systems for cargo drainage, while Eaton, in Hampshire, is providing the main engine fuel pump and engine build-up sub-systems for the Rolls-Royce Trent XWB engine.
So it’s all eyes on Toulouse as Airbus builds towards the first flight of the A350 XWB. Indeed, on both sides of the Channel, it’s hard to think of a more anticipated maiden journey in modern aviation history.
Countdown to final assembly
The A350 XWB final assembly line in Toulouse will employ around 1,500 people who will build up to 10 aircraft a month from 2018. It covers an area equivalent to almost 300 tennis courts. The roof is partially covered in 22,000m2 of photovoltaic solar panelling, which produces more than half the building’s energy needs.
At full production, the Toulouse plant will make three versions of the plane, each capable of flying non-stop for up to 8,500nm/15,580km. In a typical three-class configuration, the A350-800 will be equipped with 270 seats, while the A350-900 and the A350-1000 will offer 314 and 350 seats, respectively.
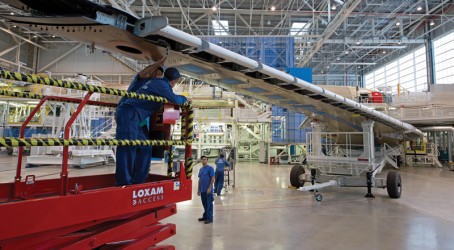
Accent on aerospace structures
Composite and metallic aerospace structures will come under the spotlight at an event in Birmingham this month.
Aero Engineering 2012 – incorporating the Composite Engineering show – will take place at the NEC on 7-8 November. The event brings together the UK’s production, design, test and inspection supply chains. It’s a chance for smaller firms to meet with global OEMs, primes and tier-one producers spanning structures, propulsion systems, components and sub-assemblies.
There’s also a strong line-up in the open forum technical sessions, where speakers will discuss topics including 3D printing of metals and nanoparticles in surface coatings.