No longer is the idea of augmenting the abilities of humans to work harder, faster and stronger the preserve of science-fiction.
Within the last year companies have started to demonstrate and trial the first robotic exoskeletons for use in the workplace. In the US, Japan and Europe, the first applications that bring man and machine closer together than ever before are appearing, and a new generation of benefits are being realised.
The first systems have their roots in the defence sector. In the US, Lockheed Martin has revealed both powered and unpowered exoskeletons. Developed by Ekso Bionics and licensed to Lockheed, the Human Universal Load Carrier (HULC) is being tested by the US military. The battery-powered, hydraulically-actuated “lower extremity” suit enables soldiers to carry loads of up to 200 pounds for up to 20 km on a single charge. A lighter and more efficient version of the HULC, which can also assist soldiers in lifting heavy loads, was reportedly last seen three years ago at a defence trade show.
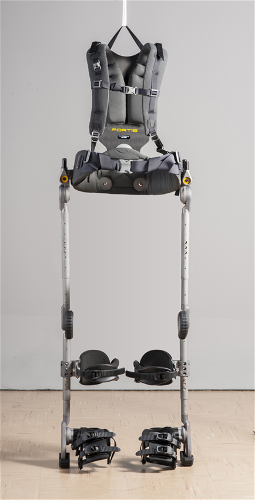

The Fortis suit is unpowered but still reduces worker fatigue
Lockheed has been keener to publicise an unpowered exoskeleton for industrial uses. The Fortis increases an operator’s strength and endurance by transferring the weight of heavy loads from the user’s body directly to the ground. Last August the US Navy purchased the first two suits to evaluate their use in shipyards. Adam Miller, director of new initiatives at Lockheed Martin Missiles and Fire Control, says: “Ship maintenance often requires use of heavy tools, such as grinders, riveters or sandblasters, which take a toll on operators due to their weight and the tight areas they are sometimes used. By wearing the Fortis, operators can hold the weight of those heavy tools for extended periods of time with reduced fatigue.”
It isn't just the US military that sees the potential of exoskeletons in industrial settings. French company RB3D has been developing exoskeletons and cobots for industrial use since 2003. The company's exoskeleton “Herculee” was developed first for defence applications and is at the prototype stage. However, the company's range of collaborative robots, which shares technology with the exoskeleton, is available to buy now.

The Hercule exoskeleton is designed for industrial applications
What makes a collaborative robot, a cobot, different from a regular industrial robot is that it works next to a person, together with them, bringing more strength and capacity to a process. The cobot does not require the equipment and guards normally used in a robotic cell. RB3D has patents in a number of key areas to ensure safety, says Olivier Baudet, business manager at RB3D: “The patents are in the architecture of the hardware to make sure there is a high level of redundancy in the control systems. They align with the latest international rules and regulations so they can be used without risk. It works by knowing the position of the human operator constantly from the position of the hands.”
Another key difference is that a cobot isn't autonomous and doesn't need to be programmed for one specific task. Instead it uses a combination of a human operation and high-level software, meaning it can be used and reused for a variety of different tasks. Baudet says: “We are more expensive now than industrial robots from the likes of Fanuc, Kuka or ABB, when considering the same number of axes. Around three times the investment compared to a €40,000 robot. But we don't need the surrounding equipment, a cobot doesn't have to be programmed and can be used for different tasks. The final cost of a robotic cell is higher.”
However, Baudet says that cobots should in no way be seen as suprior to robotic cells. They are, he says, complementary. “Where there is a fixed process there is a clear return on investment for reducing the number of workers. In these cases a robotic cell is the best solution,” he says.
The company has so far installed 15 machines in “various” applications. The typical case for the use of cobots so far is the grinding of metal parts in foundries and finishing workshops, says Baudet. This sector is where the company is seeking to build sales when it starts exporting the cobots for the first time later this year. “We are focussing on the most strenuous tasks first,” he says.
“The most challenging task is reducing their cost and proving the value of cobots through the increase in production rates and capacity they enable. They improve health and safety and empower people, with a cobot weight and power is no longer an issue, risk is actually reduced.”
Sales of the cobot range will help RB3D further develop its Hercule exoskeleton for industrial uses. A key difference with industrial exoskeletons to medical exoskeletons intended for rehabilitation is the element of control. Medical exoskeletons available today are programmed to work like a programmable robot for people who can't move their legs, says Baudet. Hercule is designed to follow follow a person's movement in order to augment it, like the cobots, not follow a pre-programmed routine.
“We see two key markets for the first industrial exoskeletons like Hercule,” Baudet says. “Strenuous tasks with manual tools that require a lot of torque and the movement of heavy loads for logistics. In these situations we've shown that the use of an exoskeleton makes the work a lot less demanding.
“The industrial and logistics market is the biggest opportunity. But the first market is medical. Military applications will take time because the specification is so tough.”
The immediate challenge is power. Hercule is able to operate for four hours from lithium-ion batteries in normal conditions, thanks, says Baudet, to the high power-to-weight ratio of its mechatronics. Longer usage times will be made possible with improvements to its exoskeleton and increases in the power density of batteries. However, the power problem can be minimised by making the batteries easy to swap and charge.
Another basic design challenge has been to make the suit fit a variety of different body shapes and to design so it can be worn and removed quickly. Hercule achieves this in a minute, says Baudet: “An exoskeleton should be like putting on a jacket and should be adjustable. Hercule is designed to fit 90% of people.”
Meanwhile in Japan, the ageing profile of the population has encouraged research into industrial exoskeletons, as researchers and the government look into ways of keeping people working for longer. It was reported last month that Activelink, a subsidiary of Panasonic, has leased out the first test models of its Power Loader device to agricultural and logistics companies. According to the report in Japanese media, the company plans to have 1,000 of the devices leased out by the Autumn.


The Activelink Power Loader and Cyberdyne's Hal suit have been
developed in Japan
Baudet says that Europe is not trailing Japan in the field of exoskeletons. “Japan has started early with medical applications, but we're not following them with industrial applications,” he says. “As far as I know, Cyberdyne's exoskeleton takes a long time to get in and out of and isn't ready yet for everyday use. Panasonic's is still at trial stage.”
The ominously named Cyberdyne, a spin-off from the University of Tsukuba, is also making progress in Japan and looking to develop international markets. The company's Hal (Hybrid Assistive Limb) became the first device in the world to be ISO certified as a wearable robot for workers and caregivers last November. The lower limb version of Hal wraps around the user's lower back, hips and thighs and is powered by a lithium-ion battery. A myoelectric sensor detects spinal activity to operate its actuators on the hips to provide additional support. Demonstrations have shown the unit assisting a person in lifting two 20kg weights. The device has also be tested by Japanese construction company Obayashi.
Whichever is first to market, and where ever it is, exoskeletons, cobots and similar devices look set to change the way many of us work in the coming years.