The catchphrase “to boldly go where no man has gone before” needs to change for the 21st century into “to boldly go where no robot has gone before”. The continuing success of Nasa’s Curiosity rover, currently on Mars, has highlighted the role that robots can play in the exploration of space. And Nasa is not alone – globally, the trend is for robots over manned space exploration.
This year, the European Space Agency (ESA) and the Russian space agency, Roscosmos, signed a deal to send the next robotic explorer to Mars in 2018 to look for signs of water and life. The Indian Space Research Organisation and the China National Space Administration are sending rovers to the Moon this decade. And the Google Lunar X prize finishes at the end of 2015. This competition will send an independently developed rover to the Moon and get it to send back images and data. If you want to get ahead in the 21st-century space race, it seems the key is to let a robot run the race for you.
Greg Sadlier is a space economist at consultancy London Economics, whose space group produces reports that help governments and industry to judge the economic value of activity in space. He says the main reason that space agencies are using robots for space exploration is their lower cost. “Environments such as Mars pose challenges that push the limits of our technical capability – low weight, low power, autonomy. A rover reduces the engineering and costs required.”
But there is a downside, he adds. “You lose the ability to be reactive and proactive in some situations – to act as autonomously as humans do.”
When emerging countries such as China and India start up space programmes, they are primarily announcing their arrival as serious players on the world stage, says Sadlier. “Having a space programme shows your economic and technological might off. Much space technology, such as satellites for positioning and monitoring, is vital for 21st-century warfare.”
The objectives of Nasa’s Curiosity are scientific, not militaristic. However, Sadlier says rovers economically justify their development and operation through a “ripple” effect whereby their innovations are applied in other areas. “A huge range of technologies improve from meeting the needs of space missions.”
The importance of space programmes’ role in developing politically important technical capability is echoed by Ralph Cordey, key account manager of science and exploration for EADS Astrium. At the back of the EADS Astrium site in Stevenage, Cordey presides over a large sandpit filled with rocks and ramps – a simulation of the surface of Mars. The ESA’s ExoMars rover, which will be landed in 2018, is being developed by EADS Astrium, and the sandpit is where its chassis and its guidance, navigation and control system are being tested.
As with all modern rovers, ExoMars’ navigation is conducted by a computerised system of cameras according to waypoints selected and communicated on a daily basis from Earth. The cameras take images of the local environment, which are fed into software that can analyse them. The on-board computer then decides the route on the ground for the rover that best avoids obstacles, and controls its movement.
The system is autonomous enough to go from point A to point B, avoiding the main obstacles, over a certain amount of terrain and obstacles up to 25cm in height.
Rover development is regional, but much of the resulting knowledge is eventually shared globally. “All the technological challenges of the ExoMars’ development have been met within Europe to give us a European capability in this area. The same engineering challenges would be faced by Nasa, by the Chinese, Russians and Indians. The knowledge of how to solve these problems filters around the world, and in some areas – such as how to clean equipment such as rovers in space – is openly discussed at conferences,” says Cordey.
However, despite the similar nature of the design challenges and engineering solutions, a common standardised platform for rovers is not likely to happen soon, he says. “The parts and robot we have in ExoMars are the design solutions to specific circumstances and requirements on Mars. There will be commonalities between rovers sent to Mars and rovers sent to the Moon, but there are also differences. So we will keep on seeing specialised rovers designed for specific missions in the future. They aren’t like satellites, which have a recurrent mission and environment.”
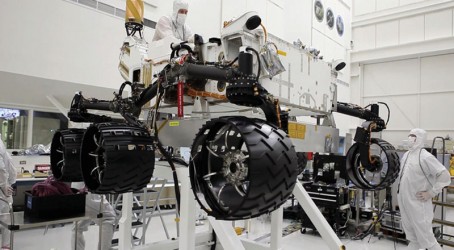
The ExoMars rover will be considerably smaller and lighter than its American predecessor Curiosity, which is much larger and heavier than most rovers. On first look, the European rover, the next to explore Mars, has more in common with Nasa’s previous generation of rover that landed in 2005, the Mars explorers Spirit and Opportunity.
The main reasons for ExoMars’ comparative smallness are its power source and landing system, says Pietro Baglioni, ExoMars rover manager, who is based at the European Space Agency’s research and development centre in Holland and has overall responsibility for the engineering of the rover.
“Curiosity looks different because it has the radioisotope thermoelectric generator (RTG), and it was delivered used Nasa’s sky crane system, which is capable of landing a big rover. All other rovers need to get power from the Sun, so they look similar. The requirement for solar arrays drives the configuration. The device has to be able to operate in low gravity and extreme temperatures. It has to be light, and able to operate with low sources of energy.”
Curiosity is the first rover to use radioactive materials to generate power as well as heat – ExoMars and other rovers use plutonium in heating units to maintain temperatures within operating parameters. The development of RTGs is ongoing, but until they become significantly smaller and easier to handle, they won’t become used widely in rovers. “In the future, we may get compact RTGs that can produce enough electrical energy to enable changes in the configuration of the rover,” says Baglioni.
The low amounts of power and volume available are large factors in the design of ExoMars and most rovers. European engineers have striven to reduce the need to divert power to heating systems and create space in the core. They decided early on to place a lot of the electronics on the outside. This design creates volume within the central core for equipment and instrumentation. It also makes it easier to maintain the core’s temperature, because it avoids the need to drive a harness from the electronics to the motors through the insulated packaging. US rovers, including Curiosity, have the electronics inside and the motors outside on the wheels.
However, moving the electronics to the exterior means that new materials have to be developed for electronics and packaging, to withstand the extreme thermocycling of the Martian environment. The result will be a ceramic material, combined with new technology for the soldering and joining, that can withstand temperatures of -120 degrees and operate at the temperatures of -60 degrees that are reached during the Martian day.
ExoMars’ other unique feature is its drill, which will be used to seek signs of life up to two metres under Mars’ surface, in contrast to Curiosity’s, which can penetrate only a few centimetres. Scientists believe that the surface has been sterilised by cosmic radiation, so if there are signs of life, they will be between one and two metres underground.
Designing a 2m drill posed another challenge for ESA engineers, particularly fitting it in the box and producing sufficient torque. The solution is an 80cm assembly, consisting of a magazine with four rods, which are engaged one on top of the other during the drilling to extend to 2m.
The drill is a vital piece of equipment, so its development and testing have been extensive. Although the ExoMars will operate in relatively soft ground, sensors will monitor the torque of the drill and switch it off if the compressive strength of the material is too high. There is also a back-up drill, in case the main tool gets damaged and is left in the ground.
The next step for robotic exploration, says Baglioni, is mini rovers, that can fetch samples and return them to Earth. The ESA, Nasa and Roscosmos are working together on this goal. “We are studying how to collect the sample in a sealed box and deliver it back.”
As to whether human rather than robot explorers could eventually boldly go to Mars, Baglioni says: “We are limited to the Moon for manned exploration so far – the complication and cost of a manned mission to Mars are enormous. But we are preparing for that with materials and systems. So, in the future, maybe.”