Articles
A British aerospace technology company has announced what it claims is the biggest breakthrough in propulsion since the jet engine.
Reaction Engines is developing a synergetic air-breathing rocket engine (Sabre) that could allow an aircraft to travel directly into Earth orbit. The technological breakthrough has come with the development and testing of the engine’s pre-cooler, which is designed to cool continuously the incoming airstream from more than 1,000ºC to –150ºC in less than 1/100th second.
Richard Varvill, technical director and one of the founders of Reaction Engines, said Sabre would lead to the development of the Skylon single-stage-to-orbit reusable launcher, bringing cheaper and more reliable access to space. “Existing rockets used to get into space are expensive, unreliable, and cumbersome,” he said.
“Our Skylon single-stage-to-orbit reusable launcher will have all the operational advantages of an aeroplane – it will have wings and an undercarriage. Being reusable it’s designed for 200 flights, so you are dividing the cost of the vehicle by 200 instead of one. In the long run the cost of a mission to space could come down by a factor of 50 to 100.”
The Sabre engine will operate as a jet engine and rocket. Its air-breathing characteristics from take-off to Mach 5 mean Skylon will be able to reduce the amount of heavy liquid oxygen carried. That would cut the weight of the vehicle, dramatically lowering fuel consumption. The weight reduction would enable Skylon to be designed as a conventional, reusable aircraft.
At the heart of the breakthrough is the development of the pre-cooler, made from inconel 718, a strong and highly corrosion-resistant aerospace alloy.
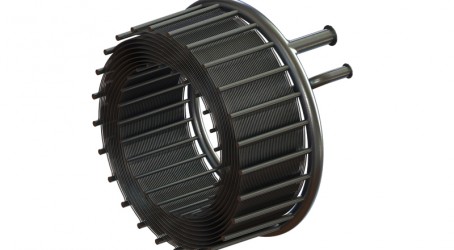
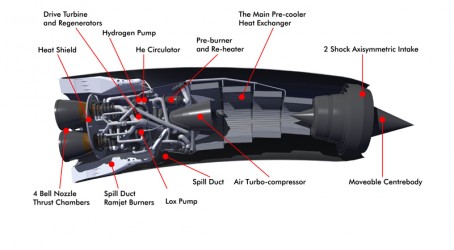
“The heat exchanger consists of a very large number of very small tubes. That, in itself, is not particularly novel,” says Varvill.
“What is unusual is how hard we have pushed it. The tubes are only 1mm diameter with a wall thickness of 40 microns. Yet they are able to withstand helium inside at 150 atmospheres pressure. We are working the materials to the very limit and we have pushed the whole design in a direction that makes it very compact and very light.”
The heat exchanger tubes are arranged in involute spirals, and formed in larger modules to make a cylindrical drum. The coolant is introduced on the inside of the drum and then spirals its way to the outside in a counter-flow thermodynamic motion.
The hot air, meanwhile, moves in the opposite direction to the cold helium in a cross-flow motion, flowing over the tubes rather than along their length. That increases the heat transfer because it causes a lot of mixing in the wakes around the tubes.
“Another advantage of this spiral concept is that these spirals are anchored on the inside, but the outsides are free to rotate. All the different modules slip over each other. It’s quite cunningly arranged so that there aren’t any thermal expansion stresses because they are all designed to move.”
Varvill said his engineers had also got on top of frost control issues. “As you cool the air subzero the water vapour tries to precipitate out as frost. If you don’t do anything about that it actually clogs the whole matrix in three seconds, stopping air flow.
“The frost system has been a difficult technology but we have managed to master it. It’s a trade secret. We don’t tell people how we actually do it but we have got on top of it because we can run steady state without frosting up,” he said.
The pre-cooler and heat exchanger have been built and tested at the Culham scientific facility in Oxfordshire. Manufacture was tricky, admits Varvill. “The heat exchanger has 40km of tubes in it. Every millimetre of those tubes has been inspected and prepared. That’s been a hell of a lot of work.”
The testing work will continue until February next year. Reaction Engines will seek to raise additional funding of £250 million over the next three years to continue detailed design of the engine. “Then we could make and test the engine. We need funding to build a ground-based demonstrator with a pre-cooler and turbo machinery, driven by helium, to prove the thermodynamics of the full engine cycle. We also want to build a small flight test vehicle to develop the intake technology.”
Varvill said that Skylon could transform space costs, bringing the opportunity of safer and cheaper space tourism, while making technologies such as large-scale solar power stations in geo-stationary orbit a possibility. “We think we could have an aircraft ready for use by 2020-2025. But it depends on funding and politics. Any support the UK government could give us would be gratefully received as the UK is ahead on this. There is the potential to create a lot of jobs and export sales if we seize the initiative.”