The detritus of our economy could have a value beyond that currently ascribed to it. And the environment could benefit, too. This is the message from those promoting waste-to-energy technology as part of the solution of dealing with the UK’s mountains of refuse.
Britain generates around 300 million tonnes of waste each year – much of which is either incinerated or goes into landfill. This, argues the IMechE, is unacceptable. And the Department for the Environment, Food and Rural Affairs concedes that the institution has a point, saying the situation is “unsustainable”. Waste contributes to climate change
and increases emissions of carbon dioxide, whether it goes into landfill or
is incinerated.
The government says it has several initiatives to reduce waste under way, including working with businesses on measures to “prevent waste occurring wherever possible” and looking at waste prevention and recycling in certain sectors such as construction. But once waste is created, is there something more useful we could be doing with it?
Generating electricity is one such option. The IMechE argues that waste-to-energy plants are attractive on two fronts: dealing with large volumes of refuse and providing an alternative means of producing power as carbon-intensive power stations are decommissioned.
There may be something of an image problem to overcome: older incinerators were seen as dirty and they did not use waste as a fuel for providing electricity. Nonetheless, both the incinerator and the modern waste-to-energy plant are sometimes tarred with the same brush, says the institution. There were also concerns about the older plant emitting harmful dioxins into the atmosphere.
But today’s waste-to-energy plant must comply with the “very stringent” Waste Incineration Directive (WID). The result is that its emissions must be 10 times lower than an equivalent coal-fired power station. Dioxin emissions under WID are limited to one-billionth of a gram per cubic metre. Bearing in mind these factors, the IMechE says it is time that waste-to-energy played a greater role in the government’s energy policy.
Lisa Jordan, business manager for bio-energy, Europe, at Air Products, has been involved in a scheme to build what is claimed to be the world’s largest waste-to-energy plant of its type on Teesside. With a capacity of 50MW, the plant is expected to power up to 50,000 homes in the region. “We have to comply with the WID, and our emissions would be consistent with what we’re required to achieve under WID for our environmental permit,” she says.
The first construction work has started at the site in the north-east, and the plant is scheduled to come online in mid-2014. Air Products describes the energy that will be created as “renewable”. Jordan says: “It’s going to be on an area that has been designated for industrial development in renewable energy. It’s reclaimed industrial land. When we looked around the country, one of the things that attracted us to Teesside was that it had industrial brownfield land available.”
She says there were no planning objections to the new plant. “Teesside is keen on the inward investment,” she adds, “because that will bring around 700 construction jobs, and then about 50 jobs when we’re up and running. The region needs investment and the creation of jobs to help regenerate the area.”
The plant is known as an “advanced gasification” type, and it is said it will divert 350,000 tonnes of non-recyclable waste from landfill each year. Gasification, which is widely used on industrial sites using fossil fuels to generate electricity, heats waste to high temperatures – without combustion taking place – with oxygen or steam to produce a “syngas”. The gas can then be used in a gas turbine to generate electricity. “We have taken a series of proven technologies for each of these individual steps and bolted them together,” says Jordan.
“One of the things we like about the technology today is its flexibility. We’re talking about producing electricity and supplying it to the grid, but the key is really getting the syngas, which gives you a future-proof energy platform. In future, you could look at using the syngas to produce hydrogen or biofuels, or you could methanate the gas and put it into the grid. You could also use it as a chemical feedstock.” Hydrogen from the plant could one day be used to power vehicles or stationary fuel cells.
Gasification vies with several other techniques for producing energy from waste, including thermal combustion, in which the waste is used to heat water to drive a steam turbine, pyrolysis and anaerobic digestion. All of these methods have different advantages, but the IMechE says that whatever technique is used, heat from processes should also be captured to heat homes and businesses. Combustion-based power plants inherently produce both heat and electricity, in the ratio of about 3:1. This heat should be captured and used for district or community schemes.
The Teesside plant will feature gasification technology from Westinghouse, which is said to offer a cleaner, more efficient conversion of waste-to-power than some traditional technologies. “The plant will be sourced from all over the world and the gasifier is obviously part of that,” says Jordan. “But there will be input from local engineering and construction firms.”
What is the attraction of building the plant for Air Products, a company known as a manufacturer of industrial gases? “We have a history in terms of energy from waste,” says Jordan. “It is part of the business’s strategy to be involved in power generation. Cleaning up syngas and putting it into a gas turbine is something we’re already familiar with. What’s unique here is that it’s the first time all these components have been put together on this scale. The plant will be the largest of its type globally.”
Jordan suggests that projects such as the Teesside plant could become commonplace. “It is the need to divert waste from landfill and the need to generate renewable power. This type of project helps the UK to fulfil both of those aims. We have publicly talked about plans to invest in other projects, and can see a future for a number of these across the UK. This is just the start.”
One British company working on its own waste-to-energy technology is Swindon’s Advanced Plasma Power (APP), which has developed a gasification type of plant that relies on a technology called Gasplasma. Said to be low in emissions, the process is compatible with recycling, and produces a hydrogen-rich syngas and a solid vitrified product known as Plasmarok, which can be used as a construction material or as road aggregate. Heat from the process can
be captured.
The plant can deal with up to 150,000 tonnes a year of municipal solid waste. Rolf Stein, chief executive officer of APP, says: “What we’ve done is to combine conventional gasification – in our case a fluidised bed gasifier – with conventional plasma treatment. We put the conventional gasifier at the front end to do the donkey work of actually creating a gas, which gasifiers do exceptionally efficiently, while the plasma technology does two things: thermally cracks the syngas into constituent hydrogen and carbon monoxide, and vitrifies the gasifier residues into a rock-like substance,
which is a safe, environmentally inert building material.”
The Japanese have been doing something similar with incinerator bottom and fly ash for decades to make road aggregate, says Stein. The APP process uses a combination of oxygen and steam, or “oxysteam”, in the gasification stage, meaning the resulting syngas isn’t diluted with nitrogen. “The gas flows are kept to a minimum, and we achieve quite an energy-dense syngas, of about 12 megajoules per normal metre cubed. That is about a third of the energy level of natural gas.” The energy-intense syngas can be fed directly into a gas engine or gas turbine to produce electricity. “That’s significantly more efficient from an electrical energy conversion perspective than a steam cycle,” he says.
Stein says the stage before the waste even enters the plant – the separating out of the recyclables – is critical. “We see no merit in putting recyclable materials, especially inert or inorganic recyclable materials, into a thermal process. It makes no sense – there’s no energy value to them, and you end up losing them.
“So we prefer to take the recyclates out at the front end. Our plant has a materials recycling facility, or a ‘fuel preparation plant’, as it might be called. We have the standard kind of equipment you see for removing recyclates from household waste, such as eddy current separators. We dry the refuse to be used as fuel with heat from the plant – you want to get the moisture content down, because then you create a more
energy-intensive gas.”
The typical ash content of a “refuse-derived fuel” is about 15%. So handling 100,000 tonnes of fuel a year would produce around 15,000 tonnes of the Plasmarok construction material. Stein says APP is working on several projects. A demonstrator plant in Swindon will be followed by a full-scale commercial operation, although it is not certain this will be in this country.
“The first commercial plant will probably be in the UK, but it may be that an international enquiry will lead to it being established overseas. We are experiencing a high number of enquiries from all over the world.”
He adds: “The ‘hot button’ item at the moment is mass burn incineration, which is typically not acceptable to the public in many cities. No one wants an incinerator. You need a solution that embraces resource management rather than just waste management, to use the resource effectively and also to recover material.”
Much like Jordan, Stein is aware of the potential of the syngas to be used for other means. APP is engaged in a project to develop a fuel comparable with natural gas, with the aim of introducing it to the grid. This project involves converting the syngas to methane. “The syngas is clean and can be used for power generation on site, or it can be turned into biofuels or water gas, shifting all the way through to pure hydrogen,” he says.
“All over the world, syngas is being converted into liquid fuels at petrochemical plants. There are hundreds of installations using gasification, coal, crude oil and biomass to create syngases for feedstocks into plastics plants and chemicals plants.
“It’s a tried and tested methodology – we just do it with waste, which requires a slightly different approach. We are one of a small number of emerging technology companies that are doing this globally. We’re proud to be doing it here. This technology has massive potential.”
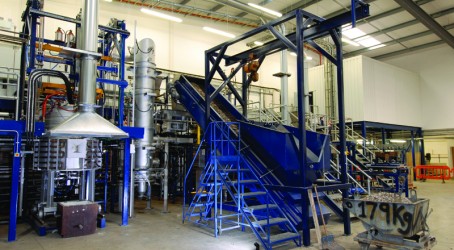