The technology of process control is escaping from the confines of factories and business sites and finding new uses in outdoor, distributed applications where continuous performance monitoring, diagnosis and control have all been difficult until now. And in very small-scale applications that simply couldn’t have been
done before.
Behind this expansion of applications is a fundamental change: where measurement and control systems have traditionally been based on hardware and hard-wired instrumentation, the new systems are driven by software, have elements of in-built intelligence and communicate through wireless means.
It’s enabling techniques long used in the process industries to be applied far more widely. But it’s also changing those techniques radically, to the point where process control as it’s traditionally been done becomes virtually unrecognisable.
Software is key to this. Dr James Truchard, president, chief executive officer and co-founder of National Instruments, says software “is at the centre of how instrumentation is being built for the future”. He adds: “Everywhere around us we see where software has taken over mobile devices and smart phones and tablets and the like. It’s really at centre stage.”
Truchard’s company, NI, is the pioneer in software-based instrumentation through the development of FPGAs, field-programmable gate arrays, customisable chips that can be configured and reconfigured in sensors. “We try to do as much as we possibly can in software, and then whatever’s left we’ll have to do in hardware,” Truchard says.
But the step-change that NI is now seeing isn’t just coming from software-based sensing and measuring devices: it’s aligning these to wireless data acquisition and transmission networks.
What this opens up, says Nick Butler, NI’s product marketing manager for wireless sensor networks, is a whole range of remote monitoring and control applications to enable factory-style supervision of events happening in difficult or faraway places, often in lots of places at the same time. “Our targets are things that are often monitored today manually or unofficially,” he says. “That includes things like the continuous monitoring of your assets or your environment.”
An example in NI’s home state of Texas is a pilot scheme in which department of transport bridges have been fitted with wireless sensors that monitor stress and strain and look for any cracks that might be growing. “It means you can prioritise the inspection, which is helpful because these agencies have limited resources and manpower these days and can’t be sending out their inspectors to every bridge when there’s no need,” Butler says.
Big applications come in hard-to-reach places as well. Across the world, wind turbines have been a spectacular growth product, but system reliability has not always matched up to the design spec: a rotating mass with a lot of variable forces acting on it is highly complex to model. It’s difficult to monitor too “and lends itself to wireless very well,” Butler says. As with the bridges, you don’t want to be sending out inspection and maintenance people unnecessarily, but you do want a continuous feed of information.
Along similar lines, and very much in the process control area, an early NI application for wireless sensors was in a US project growing algae in challenging desert conditions, where process monitoring was difficult and unpleasant. Environmental projects, says Butler, are “a huge application area, right the way through from climate research to greenhouses into agriculture. In vineyards, they want to monitor soil pH, moisture, dissolved oxygen, and CO2 levels: it’s outdoors and you want to cover long distances, so this is an obvious use.”
But it’s not just big outdoor projects. An application for wireless devices is the whole idea of smart energy usage in smart buildings. “People throw these terms around, but smartness requires data and you need data around the building to create a smart infrastructure. Wireless sensor network devices are an enabling technology for this,” Butler says.
These large-scale uses are pretty much where the technology has been up to now, and there are big areas of application where wireless systems are only just starting to take off: the technology of smart grids, for example, relies on wireless sensors not just for data collection at point of use, but also for monitoring loads and outages on the system and for switching networks so they can accept power from a lot of diverse sources.
Many of these applications are still to come, but they are foreseeably on the horizon. It is, though, only a start, and some experts in the field of wireless sensors feel that it’s not so far been a particularly good start. “About 10 or 15 years ago, when wireless was just emerging as a technology, the projections we had then just went haywire,” says Jan Rabaey, professor of electrical engineering and computer science at the University of California, Berkeley, and scientific director of the Wireless Research Center there.
He says: “If you ask me now what we’ve achieved, I’d say we’re about a tenth of what was predicted. We’re still firefighting. We’re still reinventing. The opportunities are still there, but you have to turn the wireless sensor into a platform: distributed, dynamic, adjustable, heterogeneous…”
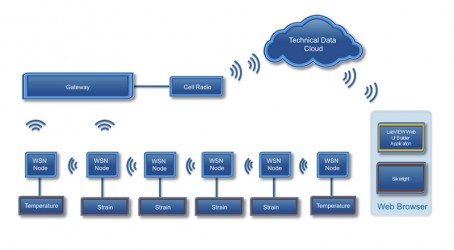
What Rabaey and other researchers in this field are excited about is a further step-change rather more radical than the one that has seen NI and others apply wireless technology to the current applications. They see the potential for radio chips to add sensing and communication capabilities to anything and everything.
At the further fringes of this vision – further, but not necessarily that distant in terms of timing – are concepts such as swarms of communicating devices acting in concert and, by talking to each other, taking what are, to a degree, “intelligent” decisions based on the information they share. That may sound far-fetched, but essentially an intelligent building that modifies its behaviour through data acquired from a multitude of sensors – turning the lights off or the heating up – is doing something similar, and a process control system that shuts a production line down when a batch of underfilled beer bottles is detected is not much different either.
Where the difference comes is in scale: both going down in size to the micro and nano scale in terms of device size and going up in the numbers and the ubiquity of such devices. Nick Butler at National Instruments says there are technical issues that have to be addressed.
“First of all, you have to have the sensing technology, and everything really still needs to get smaller,” he says.
“Then there are the wireless protocols. We at NI are part of a coalition called IPSO which is trying to come up with a standardised internet protocol for smart objects to help this world of interconnected devices, the so-called ‘internet of things’. How can you have interconnection if one device is talking Zigbee, another’s ISA100, this one’s wi-fi and that one’s Bluetooth?”
But the work on wireless sensors also leads into new areas. Butler says: “If you want to have interconnected devices and you want them to be online all the time then you can’t expect them only to be where there’s external power. So you go to batteries, but how are we going to recharge or replace those batteries when they wear out? Particularly if you’re going out to far parts of the earth or far parts of your building.”
In some cases, such as wind turbines, there’s usable energy nearby. “Wind is of course a big thing and so is solar,” Butler says. “But in this area of energy harvesting there are people looking at taking energy from thermal gradients inside and outside, at taking power from indoor lighting as well as outdoors, from vibration.
“I’ve seen work on energy harvesting from a light switch, where the flipping of the switch generates energy, or from walkways where the impact of each footstep puts energy into a capacitor that you can draw on later.”
The scale here is very small. “The beauty of it is that these sensing devices are so small they need only nanojoules of energy to operate. We’re trending towards ultra-low power sensing capabilities, ultra-low power radios that only take milliamps to transmit, though there’s a trade-off in terms of the distance they can transmit. If we can get down to nanojoules of total power then we could even be powered by things like the voice that comes out of your mouth,”
says Butler.
National Instruments’ beat in this area is in the sensors, and it’s going in two directions: wireless systems on the large scale for tough jobs like solar farms and steel plants, and the ultra-low power wireless sensor network platform, where users can pick the software-based sensors they want to connect in.
NI isn’t getting into the energy harvesting technology itself, but it has linked with a Texan company on a solar-powered enclosure for sensors and with the Southampton University spin-off company Perpetuum which has developed a device to convert vibrations from machinery into usable energy to power sensors.
There’s a neatness in this that encapsulates why this whole area of technology is interesting a lot of big companies and researchers. A potentially huge application for wireless sensors is in condition monitoring: measuring the vibrations of a machine to assess when it needs maintenance. Using vibrations to power the measurement of vibrations is smart: getting something for nothing.
And is it way off into the future? “We have the wireless sensing capabilities, with six nodes and three new ones this year,” says Butler.
“We’re adding a new gateway that integrates our CompactRIO control and monitoring system, and we’ve got programmable nodes which is a step towards more intelligent sensing, and then we’ve got energy harvesting. All of that is available today.”
Harvesting energy to power sensor networks
Energy harvesting to power wireless sensors is the subject of a lot of work at top engineering universities and research sites worldwide. At the Massachusetts Institute of Technology, researchers have developed a vibration collecting device that could work on bridges and pipelines, picking up the small movements caused by the rumble of traffic or the flow through a pipe and producing perhaps 100µW: enough to power a network of wireless sensors “that can talk forever with each other,” MIT says.
Southampton University spin-off company Perpetuum is already in this market with its Free Standing Harvester, which uses vibration to produce a steady current of 4mA at 5V for transfer to a capacitor and onward transmission to wireless sensors. Perpetuum has also developed devices for rail bearing monitoring, where wireless is the only way continuous monitoring of performance can be done.