As a teenager in the 1960s, Peter Dearman wondered what the world would do without oil, and he had the idea of using cold as a store of energy. He read up about liquid nitrogen in the Encyclopedia Britannica, and worked out a way to harvest energy from the stuff.
About 30 years later, while watching the last Tomorrow’s World BBC television programme, Dearman saw Jon Snow travel to Washington State University and talk to researchers who had built a mail delivery van powered by the vaporisation of liquid nitrogen. His interest was piqued, and he tracked down the scientific papers. The academics reported that the process could be viable only if there was a way to maintain the temperature of the liquid nitrogen as it expanded into a gas – a phenomenon called isothermic expansion. Dearman knew how to do this, and built a car to test his theory.
The Dearman engine, as it has come to be known, is a simple two-stroke machine that could soon become a player in the low-emission vehicle race. Its secret lies in the dense heat-exchange fluid, which has a high specific heat capacity, used in the engine cylinder. This type of fluid, when mixed with a very cold substance, takes in a lot of heat before its own temperature changes significantly.
The heat-exchange fluid, a water-glycol antifreeze solution, is pumped into the dead space at the top of the engine’s cylinder during the return stroke, at an ambient temperature. When the piston reaches the top dead centre of the cylinder, liquid nitrogen at -196°C from an insulated tank is injected into the cylinder. On contact with the heat-exchange fluid, the liquid nitrogen rapidly vaporises and expands in volume by more than 700 times to create a high-pressure gas. The expansion of this gas drives the piston down.
During heat exchange, the liquid nitrogen will warm up by more than 200°C, whereas the heat-transfer liquid will cool by only around 10°C. The properties of the heat-exchange fluid mean that the gaseous nitrogen stays at a near constant temperature once warmed up, which boosts the efficiency of the process because the gas cannot cool down and contract.
This process is significantly different from previous cryogenic engines, which have had poor heat transfer during expansion, says Dr Henry Clarke, lead engineer of core technology at the Dearman Engine Company. “We have got isothermal expansion.”
Once the piston reaches the bottom of the stroke, the heat-transfer liquid and the gaseous nitrogen leave the cylinder, the gas is exhausted into the atmosphere, and the heat-exchange fluid is recycled and pumped through a heat exchanger for reuse.
Ricardo has been working on a Dearman engine demonstrator for 14 months. Understanding of the liquid air engine has developed “extremely quickly”, says Dr Andrew Atkins, chief engineer at Ricardo. He puts this down to the company’s existing detailed knowledge of what happens inside the cylinders of engines, and its understanding of cryogenics. The work of academic partners – at the universities of Brighton and Loughborough, and the Rutherford Appleton Laboratory in Oxfordshire – has contributed, too. These partners have helped with selecting relevant materials, and with imaging what is happening.
“If you look at the 100 years of development of the internal combustion engine, we’ve probably done 20 years very quickly by paring a lot of the knowledge from that into this,” says Atkins. “I’m not saying we have done it all,” he adds.
So far, the peak pressure achieved inside the Dearman engine test cylinder is 103bar. But the system is constrained by a pressure relief valve. Typically, the peak pressure inside a petrol engine cylinder is around 100bar, while that in a heavy-duty diesel engine is 200-300bar. The rate of pressurisation within the Dearman engine is similar to that of a petrol engine.
The jury is still out as to whether the Dearman engine can compete with other low-emission vehicle technologies. As with batteries or hydrogen fuel cells, the energy density of liquid air is not comparable to that of diesel or petrol. The amount of energy contained in liquid air is 20-30 times less than that of diesel, and broadly similar to that of a lithium-ion battery. So any vehicle that uses the technology is likely to have a restricted range. But unlike batteries, which can take hours to recharge, liquid air can be pumped at a rate of 100 litres a minute, enabling fast refuelling.
For Atkins, the benefit of a liquid air-powered vehicle over a battery-electric one is that it does not rely on the development of new and complex electrochemistry. “This is mechanical engineering, it’s known technologies, which means that it can develop quite quickly once applications have been identified,” he says.
As well as common processes, Nick Owen, principal consultant at sustainable energy consultancy E4Tech, mentions the advantage of common materials being used to make liquid air engines. This makes them relatively cheap to manufacture compared with the other zero-emission transport technologies. “The lack of exotic materials means that there are no sensitivities in terms of material prices or nasty surprises lurking in the lifecycle analysis,” he adds.
The technology could be used in tandem with the internal combustion engine. With the trend to downsize engines and ramp up power, liquid nitrogen could be used for cooling, or to boost power density, says Colin Garner, professor of applied thermodynamics at Loughborough University.
An engine that incorporates liquid nitrogen technology may have reduced thermal loading, for example, opening up options for the use of different materials and the design of the engine. “As soon as you’ve got that cooled fluid, you can use it,” says Garner. The fluid could be used to cool superconductors, or to supplement the air-conditioning unit to improve fuel consumption in hot weather, he suggests.
The cold fluid can also be used to turn waste heat into work, and it is this area that Garner is most excited about. In a conventional engine, the difference in temperature between the engine and the ambient temperature is relatively small, so any technology that captures this heat for work will have relatively low yields. But with cryogens such as liquid nitrogen, the temperature gradient is far greater, providing the opportunity to harness the energy. “That will lead to radical new engine architectures,” he says.
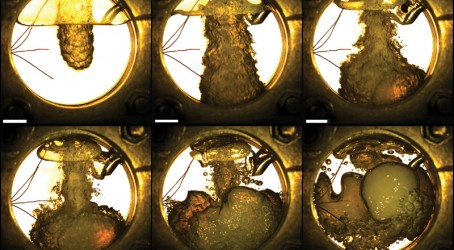
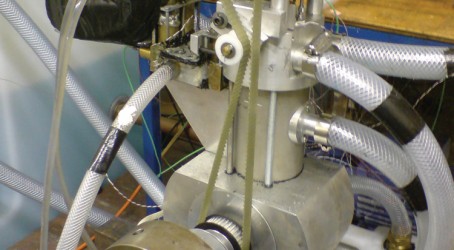
Meanwhile, Dearman is working on hybrid technology. By pairing the liquid air engine with an internal combustion engine, it hopes to convert waste heat from the radiator into power. About 30% of the energy in every litre of diesel used in a standard engine is lost through radiator heat. This waste heat could be captured in a small heat-exchange unit and used to warm the recycled heat-exchange fluid ready for injection into the Dearman engine, says Clarke. Another area for potential hybridisation is the antifreeze cooling loop.
The fluid that cools an internal combustion engine is similar to the solution that is used as the heat- exchange fluid in the Dearman engine. “In theory, you could join those circuits and add the antifreeze that is coming straight out of the internal combustion engine into the Dearman engine,” says Clarke.
He adds: “Because of the high specific-heat capacity of antifreeze, you get some thermal inertia out of it. If you couple them, you don’t necessarily have to have them working at the same power output – you can have them working dynamically.” With the correct algorithms, this set-up would enable the Dearman engine to be used as a booster for the internal combustion engine, or in stop-start technology.
Dearman is now building its first engine, which it hopes to complete by the end of the year.
In the meantime, Ricardo is developing its own split-cycle liquid nitrogen engine. The set-up includes a novel internal combustion engine that incorporates liquid nitrogen, to capture heat from the exhaust and boost fuel efficiency. It is a development of a 3MW engine for static applications that Ricardo built in 2002-03, which had almost 60% efficiency. This compares with 40% efficiency for modern diesel engines.
There is still much work to do before liquid air technology can be a viable alternative to the electric and hydrogen-powered vehicles that are on the roads today. But in contrast to these other technologies, at least infrastructure is not going to pose a barrier, says E4Tech’s Owen.
“You don’t have to install battery charging stations, or hydrogen refuelling stations, that nobody is going to use for the first couple of years. We have an infrastructure that is fit for purpose and expandable.”
In addition, the main components of liquid air – liquid nitrogen and liquid oxygen – have been produced for more than a century by the industrial gases industry. Thousands of tonnes of liquid oxygen and nitrogen are distributed across the country, for everyday use in the steel-making, food processing, medicine and superconducting industries.
There are already nine industrial gas production facilities dotted around the UK. These are in Motherwell in Scotland; the northern England locations of Teesside, Hull, Manchester and Sheffield; Margam in Wales; Fawley in Hampshire; and Thame and Didcot in Oxfordshire. The existing infrastructure also includes import terminals and storage facilities at various sites.
And nitrogen, particularly, is readily available. The commercial demand for liquid nitrogen is less than that for liquid oxygen, says a recent report about the potential of liquid air in transport by the Centre for Low Carbon Futures – a network of five UK universities. As nitrogen is four times more abundant than oxygen in air, 8,500 tonnes of waste gaseous nitrogen is vented back into the atmosphere every day during industrial production. If this nitrogen was liquefied for use as fuel, it could power the equivalent of 6.5 million car-km every day.
With the infrastructure ready to go, Owen says the challenges now lie in developing the technology and materials.
Liquid air lowdown
What is liquid air?
If you cool air to -196°C, it turns to liquid. Around 700 litres of ambient air liquefies down to one litre of liquid air, which would need to be stored in an insulated tank. It does not need to be kept under pressure.
How is it produced?
Liquid air is not produced commercially today, as there is no demand for it. But liquefied nitrogen and oxygen are used in industry. Producing liquid air would be easier and cheaper than producing liquid nitrogen and oxygen. Less equipment would be needed.
How much would it cost to produce?
The Centre for Low Carbon Futures calculates that the cost of producing liquid air would be 2.5-3.6p/litre, based on current market prices for electricity. The delivered cost after distribution by road tanker would be double this.
From mines to refrigeration
Liquid air technology could be used in several applications. A Dearman engine could be used in small, off-highway, zero-emission vehicles, such as those used in airports, inland waterways or down a mine, where the cold exhausted air could be used for cooling the environment.
Liquid air technology could power the air conditioning and lighting on a bus while it is stationary, instead of deploying the diesel engine. A London bus fitted with a 100-litre tank of liquid nitrogen, filled several times a day for this purpose, could save 25% on fuel consumption. Toby Peters, founder and chief executive of Dearman Engine Company, says that, compared with a hybrid electric bus, a liquid air hybrid would be marginally smaller and weigh half as much, even when the liquid air tank is full. “Costwise, we would be at about £5,000 at commercial scale, compared with £95,000. It’s a massive saving.”
Putting a liquid air engine in a refrigerated lorry could help to keep the produce cold. Currently, these vehicles use diesel to power a refrigeration element. Using liquid air technology in place of this could shave 15-20% off fuel requirements.