The departure of Trident submarine HMS Vigilant from Devonport dockyard last month after a substantial refit marked the culmination of a programme of work that included use of leading-edge ultrasonic techniques to perform structural survey analysis.
The use of advanced non-destructive testing (NDT) methods, including phased array and time-of-flight diffraction, for the maintenance of the nuclear sub brought notable benefits in cost reduction and the minimisation of radiation hazard. And now engineers at Devonport in Plymouth are planning similar survey work to validate the hull of HMS Vengeance.
The work on HMS Vigilant saw all main components that fulfil a key design and safety function inspected for internal defects. “This is of prime importance during the process of examining re-welded cuts made in the pressure hull when refuelling submarines,” explains Barry Richards, welding design and NDT manager at Babcock, the company responsible for the maintenance work on Britain’s nuclear submarines.
“There was also a need to look at ways of minimising the radiation hazard from the more traditional weld radiograph techniques that have been used to date. We have therefore been seeking viable alternatives to intrusive and hazardous radiography onboard submarines and surface ships for a number of years, leading to the introduction of advanced ultrasonic techniques for weld examinations.”
Submarines are complex and highly integrated platforms. Traditional weld radiographic techniques often require the whole of the platform or large sections of it to be isolated from other personnel owing to radiation hazards from the large isotopes used in the process. Additionally, the arrival of new classes of platform has resulted in thicknesses of section requiring examination outside of the range of traditional radiography.
New solutions were therefore sought. This led to the use of phased array and time-of-flight diffraction (TOFD) techniques after approval was given by the Ministry of Defence. TOFD is ultrasonic inspection involving the use of twin probes, which are positioned next to each other. One probe transmits ultrasound into the material and the other receives the reflected and diffracted signals.
One of the main advantages of this method is that it can detect defects in various orientations, whereas radiography cannot spot defects at certain depths and angles. In addition, unlike conventional ultrasonic techniques, TOFD uses an acceptance standard that is not dependent on the size of the return signal.
“In radiography, if a defect’s orientation is more than 8° in relation to the beam axis the defect is unlikely to be detected,” says Richards. “In TOFD the wavelets that emanate from flaw tips radiate 360° from the source, therefore diffracted waves can be detected from virtually any angle.”
But there are limitations. TOFD is not so effective for detecting defects near to edges, so Babcock engineers looked at using phased array ultrasonic techniques as a complementary inspection method. Phased array uses a probe with 64 elements which can be electronically excited and pulsed in varying sequences to steer or focus the ultrasonic beam to the specific area such as an edge.
So the TOFD system was used to examine the main body of the weld, while phased array was employed to look at more detailed areas where it was known that it would produce stronger results.
Richards says: “With TOFD, near-surface defects can be missed because of the lateral wave dead zone due to the pulse duration of the probes which give poor time resolution. Far-surface defects can be missed because of the back-wall blind zone where off-centre defects are obscured by the back-wall image. This is due to the ellipse of equal time – signals generated from points at any position along the elliptical arc occur at exactly the same timing. So phased array is used to correct this anomaly.”
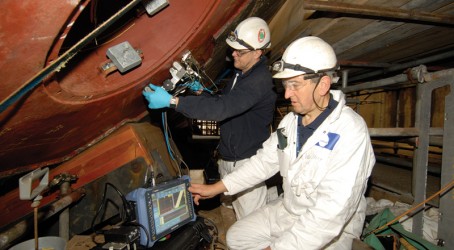
With phased array testing it is possible to configure the probes to send out beams in various individual angles (linear) or swept angles (sectorial). And with components of complex geometry, focal laws can be calculated to “steer” the beams to do a meaningful examination. Richards says this is a big advantage over manual ultrasonics where probe angles are fixed.
Phased array, like TOFD, also gives a permanent digital record which is useful for future defect monitoring. Unlike TOFD, phased array has the benefit of only having to scan from one surface. Phased array can also be used for corrosion mapping and surveys, and can be configured to produce readings every millimetre.
In addition, more conventional ultrasonic techniques (using single probes to send and receive signals to detect defects) have also been used to examine welds in plates of 8mm or more thickness, on surface ships and submarines, where radiography would traditionally have been used. This has enabled the radiation hazard to be minimised. Approval and certification bodies such as Lloyd’s Register have also now accepted this as a viable technique on thin structures, with further radiation reduction benefits.
Following investment by Babcock in these systems, staff at Devonport are now qualified to do weld examinations on components with complex and non-complex geometry. Richards says this has resulted in savings in the order of £50,000 for each major maintenance period, as specialist subcontractors are no longer required to examine complex geometries.
The reduction in the use of radiography on submarines – notably for inspection of complex and non-complex pressure hull welds – and surface ships has lessened radiation hazards. This is delivering further annual savings of £70,000 by enabling work to continue in the examination areas, so reducing downtime, he says.
An additional benefit lies in the ability to use phased array for a more complete area examination, and this has proven particularly useful on hull survey work packages with restricted access. Again, because there is no requirement to restrict general access because radiography is no longer used, these ultrasonic techniques can be deployed at any time without interference to other work on the vessel. This helps to avoid delays and keep programmes on schedule.
Babcock is now looking to explore further opportunities to benefit from these techniques in other areas. One idea is to gain approval to develop inspection mapping of pipework systems, to further reduce the use of radiography on submarines. The system would be used initially on main steam and feed piping systems, and could then be developed for bends, fittings and other materials with a diameter of below 100mm.
A further advance could be to gain approval for TOFD acceptance criteria on plate of less than 16mm thickness in surface ships and submarines. And a feasibility trial using phased array on composite materials and structures to examine flaws and thickness could lead to wider applications.