Vehicle manufacturers battle with a conundrum. Consumers want ever better performance, while regulators want reduced emissions of carbon dioxide and other malefactors, which essentially means improved fuel economy. While drivers may appreciate that, no one wants a vehicle that can’t hold its own on the mean streets of London, Munich or Shanghai.
So carmakers find themselves on the horns of a dilemma, trying to balance environmental concerns on the one hand and the needs of drivers on the other. Dr Frank Schmitt, director of product development for car turbo systems at BorgWarner, says: “No driver will agree to better fuel economy at the expense of performance. We expect the level of CO2 that can be emitted by a passenger car to become lower and lower, but drivers won’t expect to change their driving behaviour.”
Enter the turbocharger. One of the ways in which an OEM can cut emissions without sacrificing performance is to downsize a car’s engine, but this means that the smaller engine must be boosted in some way to maintain performance. The answer can be to turbocharge it. A turbocharger is a forced induction machine, whose turbine forces more air into the chamber than is the case in a naturally aspirated version. The result is a more powerful engine, so that if, for example, a carmaker downsizes from a 2.0-litre engine to a 1.6-litre unit, it can restore or improve performance by turbocharging.
Turbocharging is already ubiquitous in the diesel market for commercial vehicles and cars. In the petrol market, its prevalence is lower. This could be set to change. “Turbocharging has become mainstream,” says Craig Balis, vice-president of Honeywell Turbo Technologies. “In the diesel side of the car market, it is all turbocharged, and that will continue. With few exceptions, commercial vehicles are almost entirely turbocharged as well. The gasoline part of the passenger vehicle market is rapidly becoming turbocharged. We will continue to see a lot of growth in gasoline as engines are downsized.
“There is this equation for fuel economy: you take a larger engine, downsize it, and turbocharge it. It becomes as powerful as a larger engine, but more fuel-efficient.”
The backdrop to this trend is ever more stringent standards for emissions of CO2 and pollutants. In Europe, Euro 6 – for passenger cars – and Euro VI – for commercial vehicles – standards come into force in 2014. These feature tighter limits on emissions of nitrogen oxides (NOx), total hydrocarbon, non-methane hydrocarbons, carbon monoxide and particulate matter. In addition, Europe has approved targets that commit car manufacturers to cut average CO2 emissions from new vehicles to 130g/km by 2015 and 95g/km by 2020. Further standards – proposed Euro VII and Euro 7 legislation – will make regulations for toxic emissions even tougher. With this in mind, greater fuel economy and reduced emissions of tailpipe gases are needed and engines are more likely to be downsized.
There may not be much room to manoeuvre, even with Euro VI. “We think that Euro VII will be more around CO2 emissions,” says Jonathan Wood, executive director of research and engineering at Cummins Turbo Technologies, which supplies turbochargers for commercial vehicles. “And that is basically fuel economy. There will be tougher targets around CO2 emissions, with the same strict control of nitrogen oxides and particulates, and that will mean greater efficiency.
“But we’re getting pretty close to the limits now. The numbers are very, very small. We don’t think we can get much lower with a diesel internal combustion engine. So the next phase will be ‘how do we drive greater efficiency and less CO2?’. That’s what we think Euro VII will be about once it is decided on.”
Balis agrees that the focus for car and commercial vehicle makers is on “both emissions and fuel economy”. “CO2 regulation is, in effect, fuel economy because the more fuel you burn, the more CO2 you emit. European and US standards are leading the way. There is less regulation for commercial vehicles in terms of fuel economy. But they burn a lot of fuel, and there is a direct correlation between fuel burnt and cost of ownership.”
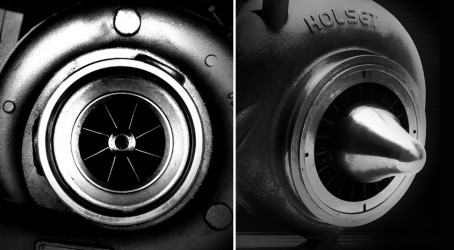
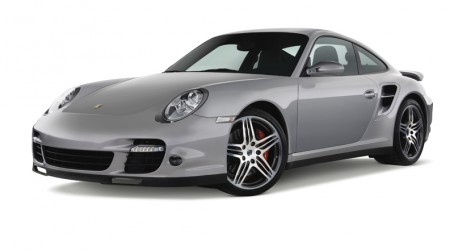
Limits on emissions of toxins, such as particulates, have tightened dramatically for commercial vehicles since the first Euro standards came in in the 1990s. Wood says: “Developments in the engine, turbo-machinery and aftertreatment have had a massive impact in terms of cleaning up the tailpipe exhaust before it enters the atmosphere. Now everything is about fuel efficiency, so for turbochargers we’re targeting greater efficiency.”
For the car market, BorgWarner produces around seven million turbochargers a year. Efficiency improvements come from using new turbine and compressor designs. Schmitt says: “There are some areas in compressor maps and turbine maps you have to focus on. On the other side, we work on the weight – we try to have smaller and lighter turbochargers.”
Because turbochargers work at high temperatures, turbine housings need to be robust and often employ expensive nickel materials, so another challenge is reducing cost. One key development has been a variable geometry turbine (VGT) turbocharger that BorgWarner developed for Porsche. Schmitt expects there to be a bigger market for VGT turbochargers for the petrol engine passenger car, where turbocharger penetration stands at 30%. But this is likely to be for niche, high-end vehicles. “Some OEMs have said they will turbocharge all the engines they have for high-level cars in Europe. In the US, Ford has turbocharged almost its whole portfolio of engines. It’s mainly to improve fuel consumption: it replaces larger engines with smaller ones.”
Cummins is pursuing an “aggressive” target of 6% enhancements in engine fuel efficiency, through improving the turbocharger, and developing other technologies such as waste heat recovery systems, which take heat from the exhaust stream and give it back to the engine as power. Wood says: “If we can use a smaller engine to do what a larger engine used to do, that’s great for fuel economy. And in terms of engine weight, the vehicle has to carry less, which makes for a more efficient vehicle.”
Challenges in turbocharger design include developing new inverse compressor wheels and different blade shapes, and new approaches to designing the impeller. “We’ve used advanced turbine tools and computational fluid dynamics to come up with higher precision,” says Wood. “That’s enabled us to make very small modifications to blade shape and angles, and to the hub, optimising performance, weight and efficiency. It’s about developing smaller, more accurate parts.”
As with BorgWarner, Cummins is keen on VGT turbochargers, which employ advanced materials and coatings to reduce weight. The company is also looking at replacing floating oil bearings with rolling element bearings, to reduce losses.
The waste heat recovery system is a new product line. It takes waste heat from the engine and passes it through a Rankine cycle. A cooled liquid in a condenser is drawn by a pump into a boiler and heated by the waste energy. It is passed through a heat exchanger in a manner similar to a steam turbine, and drives a wheel to produce 25kW, which is returned to the crankshaft. “This translates to fuel economy,” says Wood. “That, combined with turbocharger improvements, is how we’re driving toward our 6% target for improvement in fuel economy.” By using the waste heat recovery system, an operator might make 5% savings in fuel on a heavy-duty truck over a year, he claims.
Several developments in turbocharger design are taking place at Honeywell. Balis says: “There are four main areas. Aerodynamics is basically how the turbocharger compresses air into the engine, and also how it extracts energy out of the exhaust stream. There is the bearing system, because turbochargers are extremely high rpm machines, spinning at anywhere from 200,000 to 300,000rpm in a typical car. Then there’s kinematic technology, which is the moving parts of the turbocharger. The last area is materials: gasoline turbochargers can operate at up to 1,050°C, so high-temperature materials are a key element.
“Those are the key dimensions over which the technology will advance in the next 10 years.” Honeywell is benefiting from the transfer of turbomachinery technology from its aerospace division into automotive, says Balis.
Cummins says it expects to see greater hybridisation of smaller commercial vehicles.
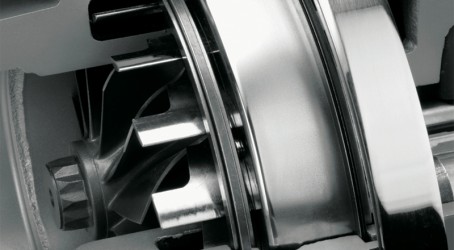