You’d expect a British Sugar plant to make sugar – the clue is in its name. But how about producing tomatoes? And animal feed. Oh, and don’t forget compounds for cosmetics.
Perhaps the most surprising aspect of this multi-stranded approach is that all of these products are made at one facility – the company’s Wissington plant in Norfolk. British Sugar has adopted an integrated manufacturing system at the site, so that the output of each process becomes the input of the next.
The result is true sustainability in action: all raw materials are turned into products, so waste is virtually non-existent. That approach allows Wissington to be globally competitive, securing its long-term future.
None of this is done out of some nebulous sense of responsibility to the environment, says the company. “It’s a commercially driven approach – each investment makes good business sense,” says Mark Carr, group chief executive of parent firm AB Sugar.
“We don’t grow tomatoes just because it feels good to make effective use of our waste carbon-dioxide streams. We do it because we think we can make a return on the investment. It’s a good example of how sustainability can be used to drive a business forward.”
Wissington is a gigantic site – it can be seen from miles around across the flat Norfolk landscape. The plant’s primary role is to take three million tonnes of beet from 1,200 local growers, turning it into 420,000 tonnes of sugar which is supplied to food and drink manufacturers in the UK and across Europe. But that’s just one part of the story.
As well as enriching the production of millions of tonnes of tomatoes each year by piping CO2 into an adjacent glasshouse, Wissington produces 120,000 tonnes of a lime-based soil conditioner used in agriculture. The site also makes 140,000 tonnes of high-protein animal feed and 6,000 tonnes of a speciality nutrient that helps support stomach function and protein digestion when added to other animal feed foods.
These are all products derived from what, in the past, would have been considered waste streams. “These days Wissington is much more than a sugar factory. We see it more as a bio-refinery now,” says Carr.
The production chain starts with the arrival of the sugar beet which, during peak periods, comes in on lorries at a rate of 900 loads a day. The first stage of processing involves cleaning the beet. Soil is separated, dried, screened and blended before being sold as high-quality topsoil to landscapers and builders. In addition, rotary stone catchers remove 5,000 tonnes of stones each year, which are washed and sold as aggregate.
Clean beet is sliced into thin strips called cossettes. These are pumped to three separate diffusers, where they are mixed with hot water to extract the sugar. The juice is used to preheat the cossettes before it passes to heat-recovery systems and on to purification. The remaining fibre is mechanically pressed before being dried in gas-fired rotary dryers. This process produces the familiar plume of steam that rises from the dryer chimney in winter. The dry fibre is compressed into pellets which are sold in bulk as animal feed.
Factory manager Paul Hitchcock says: “The pulp still contains a certain amount of sugar. When it is mixed with a bit of molasses, it makes for a high-value co-product that is used as animal feed all-year-round.”
The raw juice is progressively heated through complex heat-recovery systems, which minimise the plant’s energy demand. Milk of lime (a suspension of calcium hydroxide) and CO2 are added to precipitate calcium carbonate or chalk, which removes the impurities in the raw juice. The extracted “thin juice” passes through multiple-effect evaporators, which boil off the water and produce a syrup known as “thick juice”. This is the complex heart of the factory’s energy efficiency. The water that has been removed by evaporation is used for further heating, and then stored to be used again in other processes on site.
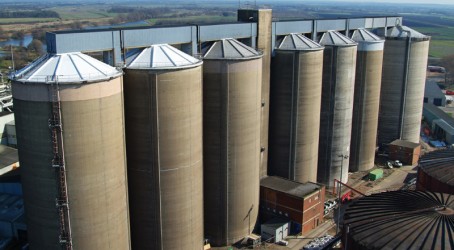
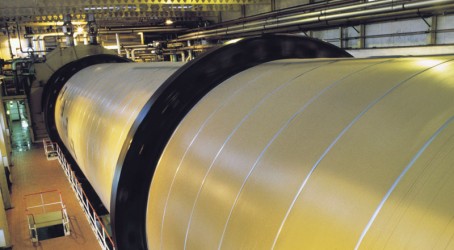
The precipitated chalk produced here is filtered, washed and pressed, producing 120,000 tonnes a year of an easily spreadable material called Limex, which is used for correcting soil acidity and general conditioning. “We have a good market for this product – it sells out every year,” says Hitchcock. “It is used to raise the pH of soil, allowing farmers to vary the type of crop they can plant.”
Up to 50% of the thick juice can be stored on-site in 10 steel tanks with a combined capacity of 365,000 tonnes. This juice is returned to the factory after beet processing to allow sugar production to continue throughout the year.
The rest of the thick juice goes for crystallisation in pans, where the juice is boiled at relatively low temperatures under vacuum. The thick juice is “seeded” with tiny sugar crystals to provide the nuclei for larger crystals to form and grow. When the crystals reach the desired size, the mixture of crystal sugar and syrup – known as massecuite – is spun in centrifuges to separate the sugar from the mother liquor. After the crystals are washed, dried and cooled, they are conveyed to seven concrete silos with a capacity of 100,000 tonnes.
After crystallisation, the residual syrup is spun away and collected before being passed through a resin separation process. Three additional products are made here: a sugar stream called extract; an amino-nitrogen stream, which is mainly betaine; and a further stream, comprising mainly mineral salts, which is called raffinate.
The betaine liquid is sold as an animal feed supplement that increases feed absorption
efficiency in an animal’s digestive system. Betaine can also be used as a moisturiser in healthcare and cosmetic products. Wissington is the second largest producer of natural betaine in the world.
The raffinate, meanwhile, is also used with beet fibre in animal feed production. The sugar extract may be used to crystallise sugar, or may be passed to an on-site bioethanol plant, where it can be used in the fermentation substrate.
“Betaine exists naturally in sugar beet, and is a useful to balance water in live cells,” says Hitchcock. “When mixed with animal feed, it can keep the stomach lining of the animal moist. When you feed an animal, its stomach starts to dry and it lowers digestion efficiency. If you keep the stomach lining moist, you can feed the animal with lower volumes of food of a different quality.”
Another facility enabled by the production of sugar syrup is an on-site fermentation/distillation plant producing up to 55,000 tonnes of bioethanol per year. This is used as a renewable fuel to blend with petrol.
Sugar syrups, including the extract from the resin separation plant, are mixed with yeast and fermented. The resulting 8% alcohol mash is then passed forward to distillation. The alcohol is boiled off from the water to produce a concentrated ethanol, which is 95% ethanol with 5% water. The remaining water is removed to produce a virtually 100% pure ethanol product, which is taken away by tanker.
A CO2 recovery and liquefaction plant, recovering up to 40,000 tonnes of what Hitchcock describes as “very clean” CO2 from bioethanol fermentation, has also been established. “It’s another example of where we used to have an arrow coming from the business labelled as ‘waste’ which is now turned into a value product used by the drinks and fire prevention industries.”
The final piece in the jigsaw is the power-generation system at Wissington. At the heart of the factory’s operations is the combined-heat-and-power plant, producing steam and electricity. “We are in the energy market – we buy gas and we sell electricity,” says Hitchcock. “The job of the gas turbine is to generate torque, so it has an electrical alternator strapped on the front that is capable of generating 50MW, which goes straight to the national grid.”
Looking into the future, AB Sugar plans additional investments at the Wissington plant to allow it to continue to improve its performance. “We are still challenging ourselves to get better,” says Hitchcock. “Whether it’s soil or stones, bioethanol or liquid CO2, everything we produce has a value to someone, somewhere. We will continue looking to find that value and to create a marketplace, so that we produce no waste, only co-products.”
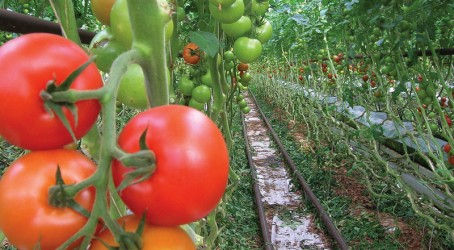
Waste gas and heat nurture tomato nursery
A good example of sustainability at the British Sugar plant is the creation of a horticulture business on adjacent land. Combustion gases and low-grade heat from Wissington’s combined-heat-and-power (CHP) plant are diverted to the site to enrich the environment inside an 18-hectare glasshouse to encourage tomatoes to grow twice as fast as normal.
The hot water from the CHP plant is pumped through pipes around the glasshouse to maintain the balmy temperatures that suit tomato plants. This hot water would otherwise be destined for cooling towers. Carbon dioxide from the CHP boiler is pumped into the glasshouse, to be absorbed by the plants via photosynthesis rather than vented into the atmosphere as waste emissions.
“We realised we had a lot of the ingredients to start a business growing a vegetable or fruit,” says Paul Hitchcock, Wissington’s factory manager. “We had the land, the road infrastructure, the low-grade heat and the carbon dioxide – so we decided to grow tomatoes. Our business now grows 140 million tomatoes per year – 20% of all homegrown production.”
More than 8,500 bumblebees, living in 170 hives, pollinate the crop and are part of the nursery’s integrated approach to crop management, using natural agents and predators in preference to agrochemicals. The glasshouse even recycles rainwater from the roof, along with other water, to irrigate the crop.