The world's fastest 'office': The first look inside Bloodhound SSC's cockpit, designed just for driver Andy Green
When the Bloodhound project to create the world’s fastest car was launched in 2008, sceptics doubted whether the ambitious initiative would ever progress. Now it has grown from a five-man outfit into a multi-million pound, multinational enterprise, with a 70-strong team and more than 250 companies involved.
This year has seen Bloodhound achieve some significant milestones that are critical to delivering a complete car in time for trial runs in 2015 in South Africa. But it has been no easy journey for the team to reach this stage, and there remain plenty of challenges to overcome before the vehicle is ready for its ultimate 1,000mph land-speed test in the Hakskeen Pan in 2016.
Conor La Grue, Bloodhound’s engineering and commercial leader, says that building the car has been no mean feat. “Every part is unique, every part is difficult – there is no easy bit of Bloodhound,” he says.
This isn’t surprising when you consider the car’s specifications. It is jet- and rocket-powered, weighs more than 7 tonnes and its engines produce over 135,000hp. It is part car, part aircraft. The front half is a carbon-fibre monocoque, like a racing car, and the back half has a metallic framework and panels like an aircraft. Such an unusual mix of technologies, for what is in effect a prototype vehicle, has required the use of modern and traditional techniques and materials. Chief engineer Mark Chapman says: “On one end of the spectrum we are pushing the cutting edge of technology, using things like additive manufacturing and very large topologically optimised components, and on the other end of the spectrum you’ve got a guy with a hammer and a sandbag putting some shape into a panel.” A case in point is the car’s first aluminium wheel, which arrived with the team in April.
A product of a three-year design study by Bloodhound engineers, Innoval Technology and Lockheed Martin, the wheel marked a vital stage in the project’s development. The 900mm wheels have to be seriously strong to endure extreme forces during Bloodhound SSC’s 1,000mph journey. The rims have to be able to withstand a radial force of 50,000g. The team opted for “old-school solid wheels made with really traditional metalwork fabrication” using a new aerospace aluminium alloy known as 7037.
The alloy wheel was made by a consortium. The aluminium was first cast into cylinders, rough machined, heat treated and cold compressed by German company Otto Fuchs and then machined in Glasgow by Castle Precision Engineering, which normally makes turbine discs for Rolls-Royce. The first wheel has been tested at Rolls-Royce, where it was spun up to full running speed on a test rig that’s normally used for turbine engine blades. The initial tests went well, says Chapman. But, with three more wheels to be made and tested before next May, there is no room for complacency.
It is not unusual for consortia to be formed to make one-off parts for Bloodhound, says Chapman. “We’re trying to do things that are unusual, new and interesting, so often you have to try and get enthusiasm in companies to do something that maybe is outside their comfort zone. Then they pull in partner companies and what you end up with is a very strong consortium that wants to achieve the best-possible outcome.”
This can be witnessed in the collaborative effort behind another significant milestone that looks set to be achieved this year – the completion of the front sub-assembly. The Bloodhound team has affectionately nicknamed this the goat’s head, for obvious aesthetic reasons. It consists of four pieces of forged and machined aluminium to which the suspension and steering components are attached. It is four huge five-axis machinings, says La Grue, made from 7075 aluminium-alloy forgings used for greatest strength and control of residual stresses.
Supply chain issues have often been a challenge for the project, but this time luck was on Bloodhound’s side: “We spent many weeks searching for these parts,” says La Grue, “and in the end Thyssen Krupp came up trumps, finding what we needed in just the right size. This was great news as a bespoke mill run for this material could easily have added six months to the project.”
Using the latest CNC machinery and aided by Delcam PowerMill CADCAM software, the University of Sheffield Advanced Manufacturing Research Centre machined the parts, and removed 94% of the metal, leaving only what was vital for the design. This reduced the start weight for the whole assembly from 924kg to just 68kg. “It took 151 man days to deliver these stunning parts,” says La Grue. But he adds that 268 parts “are still needed to complete the goat’s head, although many have already been made and the balance will soon be manufactured”.
Costs for such large amounts of material and advanced machining are steep, however. La Grue explains that the materials and machining for the goat’s head were fully sponsored by the companies involved. “This is amazing when you consider that, for the price of the materials, project management, programming and machining, you could easily fill a not insignificant garage full of your favourite supercars,” he says.
When Bloodhound finishes the desert programme the team will be looking at costs of £30-40 million. Chapman says that sourcing funding has meant depending on a large support network. “Funding comes in from many sources,” he says. “There are a host of smaller companies that work with us, and a huge amount of public support, through the supporters’ club and public talks.”
Although the car is now tangibly close to completion, the Bloodhound gang have no time to rest on their laurels. Systems are being integrated into the existing structures, further rocket testing still needs to be carried out, and the vital air brakes are being designed. They aren’t likely to be made until just before the team starts to run the car next year. The pressure is most definitely on. As Chapman says, “when we start to travel above 800mph we are truly entering into the unknown”.
Whether the car will be completed is no longer in question, but whether it achieves the 1,000mph land-speed record remains to be seen. Ultimately, though, says La Grue, Bloodhound is about inspiring the next generation of engineers, which was a key factor in the Institution of Mechanical Engineers’ decision to become a key sponsor of the project.
“Kids’ lives are full of HD fakery,” he says. “We want to give them some HD reality and show them that the real world is more exciting – this project is all about inspiration.”
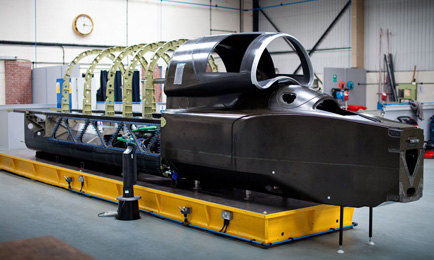
The adventure builds: Test fitting of the upper chassis, which will house the EJ200 jet engine
Armour-plated cockpit to protect driver Green
This has been a big year for Bloodhound, with the testing of the first wheel and the completion of all the car’s final structures, including the lower and upper chassis and the carbon-fibre monocoque. The cockpit, also referred to as driver Andy Green’s 1,000mph office, has been designed to his exact specifications. The structure is made from five types of carbon-fibre weave and two resins, and took more than 10,000 hours to design and manufacture.
A testament to the engineering prowess of the Bloodhound team and its partners, the carbon front section of the monocoque is designed to withstand aerodynamic loads of up to 3 tonnes/m2 at 1,000mph as well as the forces generated by the front wheels and suspension.
Sandwiched between the layers of carbon fibre are three thicknesses of aluminium honeycomb core – 8mm, 12mm and 20mm – which provide additional strength. At its thickest point the monocoque comprises 13 individual layers, but is just 25mm in cross-section. The structure weighs 200kg and bolts directly to the metallic rear chassis carrying the jet, rocket and racing car engine.
The acrylic windscreen is ready to be fitted to the cockpit. At 25mm, it is thicker than a fighter jet’s screen and sufficient to withstand an impact from a 1kg bird at 900mph. The front section of the monocoque will also carry ballistic armour to protect Green should a stone be thrown up by the wheels at high speeds. Keeping Green safe when driving, says Mark Chapman, is of the utmost importance.