Articles
Improving the UK’s training and skills base in metal technology has never been more pertinent. Rising costs for extraction of metals, processing, manufacturing, disposal and pollution control are bringing the subject into sharper focus. The sobering fact that metal is a finite resource makes that focus crystal clear. We need to learn – fast – how to get the most out of what we have: the holy grail of full metal circulation.
It is a search that the Engineering and Physical Sciences Research Council (EPSCR) is taking seriously. With part of a £70m government investment in growth sectors in high-tech manufacturing, the EPSCR has set up the Centre for Innovative Manufacturing in Liquid Metal Engineering (Lime) at Brunel University in west London. The centre has pulled together engineers, scientists, technicians and researchers from universities and manufacturers. There is a sense of excitement on site that the work in its four labs will make a difference to the UK’s metal industry and help the environment.
Opened in February, Lime was set up in collaboration with Oxford and Birmingham universities. It is sponsored by the EPSRC and a number of industrial partners including Jaguar Land Rover and Rolls-Royce to develop manufacturing technologies that significantly cut carbon emissions, reduce energy use and save millions of tonnes of natural resources every year.
Zhongyun Fan, professor of metallurgy at Brunel University, is Lime’s director. He says one of Lime’s main aims is to achieve full metal circulation – reusing, remanufacturing and recycling metals already in use by using innovative technologies. Full metal circulation would lead to substantial conservation of natural resources and a reduction in energy consumption and CO2 emissions – major box-tickers on Lime’s to-do list.
“We will try to save metal resources and reduce energy usage,” says Fan. “Liquid metal engineering will be an important part of metal circulation, delivering key technology to achieve this, using materials, including secondary, recyclable metals, rather than going to brand new materials.”
Researchers in the liquid metal engineering laboratory closely control the structure of metals to better understand their capabilities. One device breaks up the oxides in molten metal, allowing the material’s microstructure to be refined. A DC simulator allows researchers to recreate the microstructure of multi-tonne castings on a laboratory scale; the reduce pressure test machine reveals the hydrogen content of an alloy when a liquid metal is poured into the device.
“We try different techniques to treat liquid metal to deliver a scientific understanding,” says Fan. “Once the science has been developed we can directly transfer the understanding into technology.”
The high-pressure die-casting laboratory develops automotive components. The pride of the room is a furnace that can melt 3kg of aluminium in 180 seconds, allowing high-quality metal castings to be made very quickly with the flexibility of changing alloy composition on demand.
“The fast melting is a new technique to increase efficiency,” says Fan. “The process can help with increasing fatigue strength. Components will last longer.”
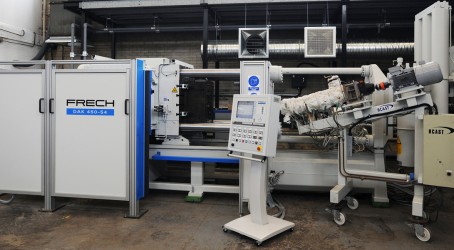
The third lab is the sand casting laboratory where large components of around 100kg of aluminium can be quickly cast. In the casting technology laboratory the team works on scaling up Lime’s technology.
It is working closely with the aerospace and automotive industries because they would benefit most from the R&D in weight-saving technologies, says Fan. “It will benefit the sectors, particularly automotive, in using lightweight materials to reduce the weight of vehicles. It will mean better efficiency and less CO2 emissions,” he explains.
One development is in lightweight car body parts from super-ductile aluminium alloys (which can be used for direct casting) for JLR. The focus of Lime’s work for Rolls-Royce is on enhanced efficiency of engine materials including surface coatings.
Liquid metal engineering is not a major industry, says Fan: other people “here and there” are engaged in it on a small scale. But he sees a significant role for Lime in the metals industry. “I want to see in 20 or 30 years time that we are playing a major part in the whole metrological area,” he says. “Metals and metallurgy are so crucial to a country’s economy.”