Extreme products call for extreme testing. The products being designed and built by the defence industry, which have to endure some of the harshest environments imaginable, certainly fit that bill.
From fighter planes to body armour, many of these products are intended for use where there is a very real risk of damage by bullets, shrapnel or explosive blasts. To make sure the range of materials used in these products is suitably robust, a great deal of computer modelling is carried out. But the ultimate test, given that lives could be at stake in these scenarios, is to simulate these very high-speed impacts.
At BAE Systems’ Filton site near Bristol, as part of the Advanced Technology Centre, is the High Strain Rate Test Facility. Inside this specially designed building is the machinery that, under very controlled conditions, creates the experience of being shot at by using gas guns.
The facility started out 20 years ago with one relatively small gas gun, but has grown to host five guns of varying size and power. “As we developed the facility, we built a range of gas guns,” says David Townsend, executive scientist at the facility. “The biggest fires projectiles at 4km a second. At the other end of the range, where we’re using heavier and slower projectiles, that one can fire 20 to 30kg at 100m per second.” As the five guns share some common parts, only two can be used at any one time.
Gas guns work on the principle of pumping gas, usually helium, into a chamber until very high pressure levels are reached. The pressure is released directly onto a sabot – effectively an open carrier for the projectiles – which is propelled through the gun’s barrel until it hits a stop close to the barrel’s opening. At this point the sabot is halted and the projectiles continue forward, into the material sample. The trigger mechanism consists of a diaphragm made of oxygen-free copper, which is pushed to its specified breaking point during the build-up to each firing. Having burst to allow the gas to shoot towards the sabot, a new one is installed for each shot.
The largest gun, which has been in use for 15 years, is a two-stage design. “Essentially it is two guns back-toback,” says Townsend. “The first generates movement through a build-up of high pressure gas, and that feeds into a piston.” This further amplifies the speed with which the sabot is sent forward.
The gas used is helium, which is stored at 7,000bar before release. This provides enough energy for speeds of up to 4km a second, which equates to just less than 9,000mph. This is sufficient for most of the centre’s testing needs, says Townsend, adding that 1,500 shots are fired per year, on about 100 different test subjects.
However, faster speeds are possible for certain experiments. “To get higher speeds we would use hydrogen, if we wanted to look at collisions caused by space debris,” says Townsend.
Indeed, research on potential collisions during the Apollo space programme of the 1960s necessitated the initial development of the two-stage gas gun, in the US. When the Apollo missions ended, interest in similar tests died down until being revived with the launch of the so-called Star Wars space weapons programme in the 1980s.
When gas guns were first used at Filton, they were housed in a converted air-raid shelter. However, in 2007 the equipment was moved into a building specially converted for this purpose and which includes a novel safety feature in the roof. “Because we’re using a lot of high-pressure gas, part of the roof, about 1m by 2m, is designed to burst open if the pressure gets too much,” says Townsend. Owing to the extreme safety risk of such equipment, it is enclosed within internal, windowless walls inside the building and is operated from a separate control area.
When the gas guns were built, the aim was to study missile-to-missile interactions. “Most recently, most of our work has been related to vehicle armour,” says Townsend. This sees projectiles, usually steel cubes and rods, of around 100g thrown onto samples at 2km a second. “It’s trying to simulate explosive-generated particles. Not exactly IEDs, but we’re looking at the same sort of energy flux on the surface,” says Townsend, referring to the improvised explosive devices, or home-made bombs, seen in Iraq.
The size of these simulated shell fragments is limited by the diameter of the barrels of the gas guns, which are totally enclosed for safety reasons and range, on the biggest gun, between 12.7mm and 35mm across. The use of uniform shapes, such as cubes and rods, is to make comparisons between tests easier and to ensure the mass of the projectile is accurately calculated. It also makes programming data for computer modelling more straightforward, particularly compared to using a more realistic object, such as a stone, which is infinitely more complex in terms of its dimensions.
Work for the army in developing protective bodywear requires the mimicking of bullets. For this, rods made of steel or the much harder tungsten carbide are the preferred choice. Other work, which requires the firing of much larger objects, has seen a focus on rubber, which can cause huge damage to aircraft, as seen in the fatal Concorde accident of 2000.
“One thinks rubber is fairly flexible but it’s very tough and, if it’s moving fast and your aircraft or vehicle has got a thin skin, it can be catastrophic,” says Townsend.
The impact of these experiments is measured in a variety of ways. “Because we are in a lab and it’s a very good, secure environment, we can bring in lots of diagnostic equipment.
The first thing is a high-speed camera that records footage at 500,000 frames a second,” says Townsend. This rate of capture dwarfs the standard used in movie making, of 24 frames per second. “When firing the gun at top speed, it’s travelling 4mm every microsecond. If you want to capture that event, you need those sorts of speeds,” he says.
X-ray imaging is also used due to side effects of the collision itself. “The problem is that at those speeds the impact creates a lot of debris and light which clouds the view. So we also have a two-part, short-timescale, flash X-ray imaging camera,” he says.
This provides information when visual inspection is no longer possible. Depending on the type of test, strain gauges can also be put on the target. Townsend says that these are standard, off-the-shelf strain gauges. Pressure throughout the system is also measured through transducers.
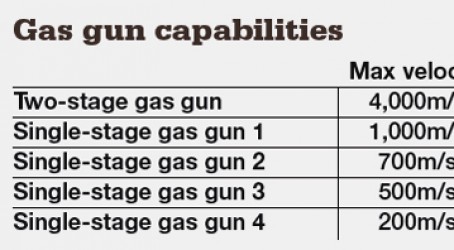
A growing source of work for the facility in recent years has been helping out in the development of new materials and for verifying predictions made in computer modelling. Stewart Penney, head of business development for design and materials technologies, says this work is carried out for BAE itself as well as for other defence companies, some of which are in the private sector – all unnamed owing to commercial sensitivities. Penney says: “These days, people don’t want to build a complete model and destroy it so we’re talking about finding the elastic limit and strain rates for their materials.” This work is mainly focused on aircraft and other types of vehicles. “But we do some work on fixed infrastructure, such as concrete. That information is useful for blast loading,” adds Penney.
Like any testing of products designed on computers, the information from strain gaugesgoes towards verifying computer predictions of the effect of an impact. “If you’ve got that right it gives much more confidence in the modelling,” says Townsend.
‘Liquid’ armour offers improved protection
A recent subject for gas gun testing has been a new type of ultra-lightweight, flexible “liquid” armour, developed by BAE Systems. When integrated into standard Kevlar body armour, the liquid component offers easier movement for the wearer, while reducing its thickness by up to 45%.
The design uses the properties of shear-thickening fluids which, when subjected to an impact, become stiff and absorb energy, so preventing the missile from penetrating the armour.
Tests done at Filton on prototypes last summer found that the liquid armour can be thinner than the current standard while offering the same protection. These images show a gas gun trial of 31 layers of untreated Kevlar subjected to an impact (top), repeated on another sample containing 10 layers of the liquid armour, in durable casing, (bottom).
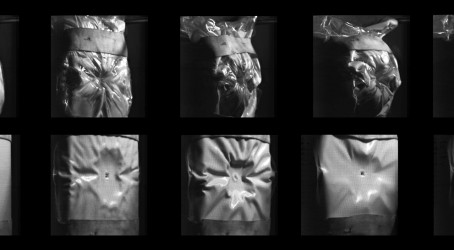
- Big bang (top): Gas gun trial of 31 layers of untreated Kevlar subjected to impact
- Big bang II (bottom): Test repeated on sample with layers of liquid armour