On an unprepossessing site in a leafy part of Bedfordshire, a team of engineers are working hard on a project that will deliver vital improvements to a piece of equipment that is widely recognised as the workhorse of the British Army.
The Lockheed Martin facility on the outskirts of Ampthill is where the Warrior armoured fighting vehicle is being upgraded, giving it more firepower and better protection, as well as providing a more comfortable environment for the soldiers who are transported in it.
Warrior has been in service since the 1980s and has seen action in Bosnia, Kosovo, Iraq and Afghanistan. And, bearing in mind that the new £642 million package of work will extend the vehicle’s life until 2040, the army is relying on Lockheed Martin’s engineers to make it the very best it can be.
“Warrior is core capability. It has been pretty much everywhere the British Army has been for the past 30 years,” says Bob Armstrong, product team leader for the Warrior capability sustainment programme within Lockheed Martin UK. “Our challenge, therefore, is about improving the capability of an existing legacy platform. And that means using technology to deliver significant fightability, lethality and survivability improvements.”
What that military jargon translates to is an upgrade to major systems in the turret and hull, including a 40mm cannon with fire-on-the-move stabilisation, an advanced, modular armour system, blast-resistant crew seating, and an environmental control system that means infantry troops won’t have to suffer the extreme temperatures of up to 70°C that have been encountered in the rear compartment of Warriors in service in Afghanistan.
“The improvements to firepower and electronics will put Warrior at the heart of the British Army’s combat capability for at least another 25 years,” says Armstrong. “The upgrade comprises a package of work – including mechanical, electrical, software and materials engineering – that will come together to transform the capability of the vehicle.”
About 700 Warriors were built in the 1980s by GKN Defence. With a driver seated in the front hull and a gunner and commander seated in the turret, the vehicle’s primary role has been to transport up to seven infantry soldiers under protection to the frontline.
Since the vehicle’s introduction, the turret has been armed with a non-stabilised, 30mm cannon. A crucial part of the current upgrade is the replacement of this cannon with a more powerful 40mm weapon, which will be fitted with a new digital fire control system to improve accuracy. A series of sensors and gyros provides auto-stabilisation for the turret, so the cannon can be fired while the Warrior is travelling on bumpy ground. Armstrong says this is a huge advance.
“The 30mm cannon has limited capability,” he says. “Historically, it has been used to spray lead around to keep people’s heads down rather than to engage with targets and do any significant damage.
“The new stabilisation sighting system will give the Warrior fire-on-the-move capability. While driving over cross-country terrain, it will be possible to hold the gun on the target and fire, irrespective of the movement of the vehicle. It turns the Warrior from being an infantry fighting vehicle into something more like a medium-sized tank.”
The cannon will also have an improved type of ammunition. The projectile will be encased in a single cylinder, with the propellant packed around it, rather than being separated as two distinct compartments. This arrangement cuts the length of the round by 50%, says Armstrong, effectively compensating for the increased space requirements that are required for the more powerful gun.
The cannon will be fed by a new auto loader system developed by Meggitt Defence Systems. This auto loader can be fed with scores of rounds, with the ammunition handling contained behind armour and physically separated from the crew. This, says Armstrong, is a far safer and more efficient approach than that currently installed.
Increasing the protection given to the soldiers is another important aspect of the Warrior upgrade. The conflicts in Iraq and Afghanistan have been characterised by troops coming under attack from improvised explosive devices. Lockheed Martin’s engineers have attempted to provide additional protection against such threats by developing a modular appliqué armour system for the turret and a modular armour mounting system for the hull.
The system permits the modular fitting of a variety of armour options to address specific missions. It consists of lightweight hull fixings and standardised mounting plates for modular armour solutions, including passive armour, explosive reactive armour and bar armour. They can be rapidly fitted, replaced or entirely removed by the vehicle crew using simple tools. Consequently, the armour can be tailored for each mission.
“The strap-on armour that Warrior originally took into deserts was designed in three months as an urgent operational requirement but ended up being continuously fielded in various operations ever since,” says Dave Brundle, hull systems integrated project team leader at Lockheed Martin. “The system had fundamental limits due to the time it took to design.
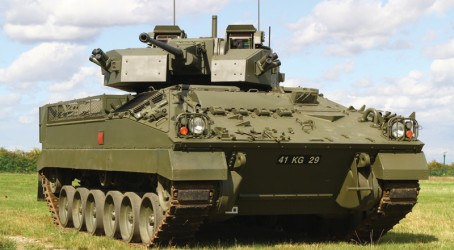
“The basic concept was the creation of a rail along the top of the vehicle to which armour panels could be attached to give protection – the idea being that if you wanted to swap the armour, you just unhooked it and put different types on. But it was very much a scientists’ concept. It needed some engineering realism behind it.
“What we’ve come up with is a more robust system of mounting armour on the vehicle which is easy for the crew to service. The fit of the armour can be managed by the use of the basic tools on the vehicle. Everything is designed to use the same spanner and equipment.”
Brundle says that much work has also gone into the development of a novel ceramic armour with an aluminium backing, that will be used as a spall lining on the upgraded vehicles. “You are never going to have an armour platform which is going to survive against all threats.At present, there isn’t a spall liner in the Warrior turret, so when a hole is created some fragments can manage to get through. The role of the new material is to catch these.”
The new ceramic/aluminium spall liner has been field-tested with very large high-energy projectiles used to punch massive holes through steel armour, says Brundle. “It has real potential to catch fragments and protect the crew.”
Other areas of survivability are also being addressed. A mine blast-resistant seat subsystem has been integrated. The turret seating will be mounted on an elevated mast, with the operator secured in a new five-point harness. The seat can be elevated for head-out observation and it has been fitted with a collapse mechanism for instant retraction.
“In the elevation mechanism, there is shock attenuation for energy absorption,” says Brundle. “The mount absorbs the energy rather than transmitting it to the
operator’s spine.”
Efforts have also been made to improve situational awareness for troops seated inside Warrior. New electronic architecture allows information sharing around the whole vehicle, with cameras relaying multiple views of the outside world.
Bob Armstrong says: “These guys get bounced across the battlefield for a couple of hours and then they get thrown out at the end and they are expected to engage with the enemy. Now we can provide them with situational awareness. There’s a screen in the rear section providing views of what the commander can see and where the cannon is pointing. Before dismounting, soldiers have some form of briefing on what’s outside the green box they have been sitting in for a couple of hours.”
Crew space has also been updated, with the operating environment decluttered through the removal of legacy equipment. “As Warrior is a platform that has been in service some time, it has gradually had items added to it,” says Armstrong. “We’ve cleaned a lot of it out and started again – it’s a more elegant design solution. It’s less cluttered, with more space, and easier operation of the man-machine interface for the control systems.”
Crew comfort has also been considered. At present, the Warrior hull doesn’t have any air cooling. With up to seven troops sitting in the rear compartment in close proximity for several hours, temperatures of up to 70°C have been recorded in Afghanistan. An urgent operational requirement has delivered an environmental control system that can be strapped on the back of the vehicle, but this has limited capabilities. Armstrong says that a more integrated cooling solution that is under development will perform far better.
Testing of the various sub-systems and technologies on the Warrior is now under way. Mine-blast trials have been conducted on the seats, ballistic testing has been carried out on the armour panels and the 40mm cannon has undergone live firing. While there have been no major technical problems, the trials are expected to feed into the construction of the prototype vehicle next year.
On the cannon system, for instance, Armstrong says, “We have needed to look at the gyro stabilisation of the sight-head. That was an issue we’ve sorted as part of the development process. We didn’t hit any problems on the turret vibration testing – predominantly because we went through a lot of analysis work to get to that stage.
“The ammunition handling system integration has been proven as a test rig, and it now needs to be proven repetitively as a battlefield mission to prove the duty cycle. That is going to be the next challenge that we face.”
Lockheed Martin will build a total of 11 demonstration vehicles between 2014 and 2015. It then hopes to secure the main production contract, with the upgrade work likely to be carried out at the facilities of the Defence Support Group in Donnington, Shropshire. “The plan is to carry out the upgrade at the same time as overhaul work at Donnington,” says Armstrong. “That would seem to be a sensible and cost-efficient use of time.”
It is expected that at full production, each Warrior will take between 60 and 90 days for the upgrade to be completed.”