National Instruments prides itself on being a bit different, fostering its own ethos that even includes having a 100-year business plan
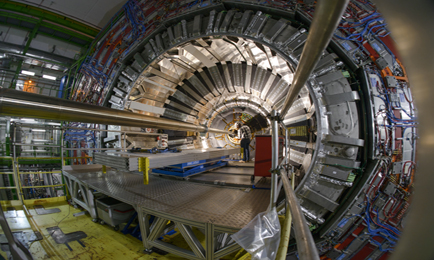
Universal knowledge: NI's equipment and software is crucial to the success of the research at Cern
If you visit Austin in Texas, you’ll see three words that crop up just about everywhere, on signs in bars, emblazoned across T-shirts and on car bumpers. “Keep Austin Weird!” they say, spelling out the locals’ desire to retain the city’s quirky, offbeat appeal.
No wonder Austin is home to the HQ of National Instruments. Weird is probably too strong a word for it. But there’s no doubt that National Instruments, one of the world’s biggest providers of test and measurement equipment, is not your average billion-dollar company.
First, there’s the humble Apple-esque beginnings, with the company having been set up by three University of Texas researchers in a garage in 1976. Remarkably, two of those founders – Dr James Truchard and Jeff Kodosky – are still at the helm, adopting a hands-on approach that has delivered incredible growth. National Instruments now employs more than 7,000 people across 50 countries.
And then there’s the unorthodox values that Truchard and Kodosky have instilled in the organisation. National Instruments prides itself on having a truly long-term strategy, which includes the use of a 100-year business plan to guide it through any tough times. The company also advocates a policy of talent recognition and internal promotion, and regularly features high up in lists of the world’s best places to work. Maybe weird isn’t so bad, after all.
“The 100-year plan is crucial to our core values,” says Francis Griffiths, the University of Wales electrical engineering graduate who joined NI in 1989 and has risen to the position of senior vice-president of regional sales and marketing. “It provides us with a philosophy in terms of our culture, who we are, and what we want to achieve. Dr James Truchard and Jeff Kodosky have both led the development of the 100-year plan. It has served us well.”
It would be easy to dismiss such comments as flowery rhetoric. But there is plenty of evidence of long-term thinking. One of the guiding principles from the days of being a start-up has been a desire to be self-financing, and not being beholden to banks. That has led to a prudent approach to running the business, resulting in a strong cash position: the most recent figures report cash and short-term investment of $393 million.
That, in turn, enables National Instruments to avoid knee-jerk decisions when times are tough. The company fought hard to protect jobs in the aftermath of the economic crisis in 2009, reinforcing the message to staff that it was a committed and stable employer.
“We took a long-term view – as we do in good and bad times,” says Griffiths. “During the downturn, we carried on focusing on innovation, investing in research. As we saw the recovery, we were well-positioned to grow the business.”
With such a refreshingly enlightened approach to business, it is perhaps a surprise that National Instruments retains something of a low profile, being relatively unknown outside the engineering and scientific communities. That obscurity is easy to explain.
While its range of data acquisition, automated test, and embedded control and monitoring equipment underpins some of the biggest and most complex projects in the world, its technology mostly remains in the background, hidden away out of sight. And National Instruments likes it that way.
“We often sit one step behind the applications, but making them possible,” says Rahman Jamal, technical and marketing director Europe, another long-serving executive who has two decades’ experience with the company. “Some of those applications deal with existential matters that have far-reaching consequences. The large hadron collider at Cern, for instance – that will answer searching questions about our place in the universe. And those answers will be supplied using our scientific tools.”
Jamal gives other examples, pointing out how the company’s equipment is helping engineers to answer global grand challenges relating to environmental issues such as water contamination and the development of cleaner energy technologies. Meanwhile, within education he is proud of how the LabView graphical programming software has been designed for use with the Lego Mindstorms robotics platform, encouraging more than two million students worldwide to pursue Stem careers.
From Cern to Lego – such diversity offers another insight into the business philosophy. No one industry sector accounts for more than 15% of the company’s revenue. That distributed set-up, spread across diverse sectors including aerospace, energy, infrastructure, mobile communications, automotive and transport, education, research and consumer electronics, also provides protection against fluctuations in market conditions. Or, as Griffiths puts it, “not having all our eggs in one basket”.
In terms of new opportunities, it is the rapid emergence of what many are calling cyber-physical systems that excites the senior management. This is a snappy name for a host of next-generation ICT systems that are interconnected and collaborating through architecture such as the internet of things, providing people and businesses with a wide range of new applications and services.
These ICT systems are increasingly embedded in all types of goods and equipment, making them smarter and energy-efficient. And they are often endowed with intelligent control, monitoring and data-gathering capability. That’s where National Instruments comes in. “We provide technologies to build cyber-physical systems, offering a platform approach for their construction,” says Jamal.
“There are a number of areas that have the word ‘smart’ in front of them, whether they be smart grids, smart health devices, or smarter factories. They are all interconnected and embedded, and our graphical system design is crucial to that.”
Griffiths and Jamal are passionate about their work. Both have risen up the career ladder as the company has grown. Jamal remembers the day he was interviewed by Truchard, 23 years ago. “The first question he asked me was ‘what is your goal in life?’. That immediately made me think that National Instruments could be the right company for me.
“I want to help people, to touch their lives, and to give motivation to help others. I like helping customers to solve problems. I like the ever-changing impermanence. It’s exciting, surfing on change, rather than trying to stop it.”
Griffiths has similar recollections. After graduation he worked for a company supplying switch mode power supplies which gave him the task of assessing the market and identifying an automated test system. “I met some applications engineers and they demonstrated LabView 1.2 on a MacPlus,” he recalls. “It was so unusual. The software totally blew me away.
“I thought, this is so ahead of its time – so I joined the company. I have since seen LabView evolve and it’s been phenomenal how far it has come. It is such a strong tool for graphical system design.”
Does he think that if NI continues to grow it might lose its distinct ethos? “That won’t happen,” he says. “The 100-year plan will ensure that. We are focused on making a company that’s built to last.
Riders on the wind: testing time for bikes 24/7
Bike manufacturer Specialized has created the world’s first wind tunnel dedicated to cycling, using test and measurement technology from National Instruments to give engineers clear insight into performance levels. The facility, in California, has been designed to allow engineers to assess ways of overcoming the inhibiting effect of drag caused by wind. Other bike makers rely on third-party facilities usually used for automotive and aerospace testing.
The Specialized project team configured a bespoke arrangement of NI hardware and software to develop a measurement and control system. It gives the ability to collate data on parameters such as airflow and to incorporate visual feedback from cameras.
Traditional wind-tunnel testing can be time-consuming and inconvenient. With the bike rigidly bolted to the tunnel, it was difficult to recreate the realistic movement that the machine would experience. The new facility delivers all aspects of aerodynamic testing and, because it allows for continuous movement, it more accurately recreates the dynamic conditions of the real world.
Mark Cote, aerodynamics engineer at Specialized, says: “We’ve put 10 athletes through and it’s a complete game changer. The design is specific for our needs and we can measure very precisely. The test section is big enough for multiple bikes and riders.
“One of the biggest things we’ll be able to do with this wind tunnel is make life better for the commuter. If you’re riding to work, you want to be less sweaty and you want to get there faster to make your meeting.”
Crucial to this success is the test and measurement system. Specialized used NI LabView system design software, PXI hardware and the Vision development module with off-the-shelf components such as cameras. With LabView, Specialized can interface with sensors positioned on the bike and cyclist while engineers monitor the data on an iPad using the NI Data Dashboard for LabView mobile app. Realtime visual data captured by cameras is integrated by the Vision development module.
Aerodynamicist Chris Yu says: “We chose to work with NI in building the wind tunnel because of the ability to integrate a variety of I/O and instrumentation, and the flexibility to adjust variables and change the tests. Being able to test 24/7 will lead to innovations that may not have surfaced otherwise.”